Importance of Back-EMF in Sensorless BLDC Driver Design
Back-EMF is the cornerstone of sensorless BLDC driver design. By accurately interpreting the voltage induced in unpowered motor phases, engineers can achieve reliable rotor position detection without using physical sensors. This not only reduces system cost and complexity but also enhances reliability in demanding environments.
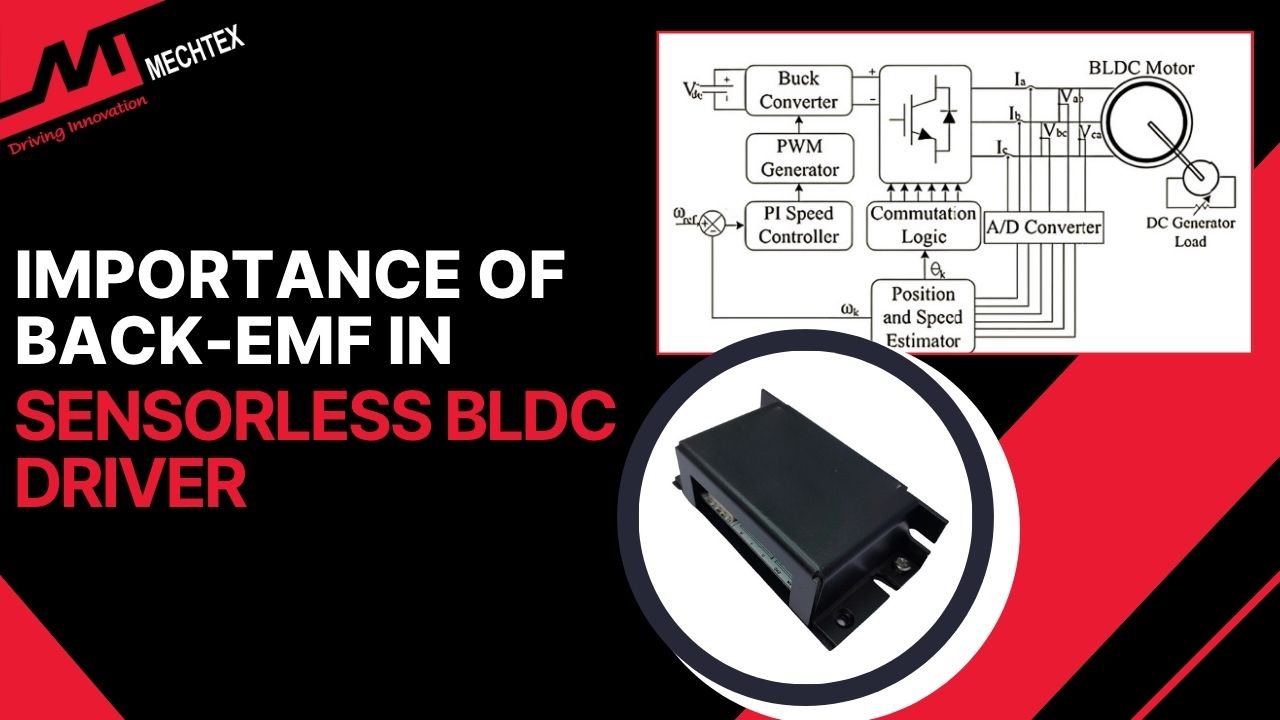
Brushless DC motors (BLDC motors) have revolutionised the modern motion control system with their high efficiency, compact design and long life. Traditionally, BLDC motors use hall sensors to detect the rotor position. However, the hall sensors are replaced by sensorless BLDC drivers.
At the heart of every sensorless BLDC driver is a back EMF (Electromotive Force), a key phenomenon that enables position detection without sensors. Due to their simple algorithm, cost efficiency and high reliability in a harsh environment, BLDC drivers gain immense importance in BLDC motor design.
This blog explores the importance of Back-EMF in sensorless BLDC driver design, its operating principle, techniques for detection, and practical advantages.
What is Back-EMF?
Back EMF (Electromotive Force) is the voltage generated by an electric motor as the rotor turns. It is the key phenomenon for DC motors and Brushless DC motors (BLDC motor).
It occurs due to Faraday’s law of electromagnetic induction, which states that a changing magnetic environment within a conductor induces a voltage. In BLDC motors, as the rotor spins, it cuts across the stator magnetic field and produces a voltage that opposes the applied input voltage. Hence, it is called back-EMF.
Back EMF plays a vital role in DC motor, BLDC motor and AC motors. It is proportional to the motor’s speed and directly related to its construction parameters, such as winding turns and magnetic field strength.
Back EMF (E) = ke ⋅ ω
Where,
E = Back EMF Voltage
Ke = Motor’s constant Back-EMF
ω = Angular Velocity of the Rotor.
At higher speeds, back-EMF increases and effectively reduces the net voltage across the winding and draws limited current. This regulation helps prevent motors from drawing excessive current and improves efficiency.
In summary, Back-EMF is not just a byproduct of motion but a key parameter influencing motor performance, speed control, and energy efficiency.
Role of Back-EMF in Sensorless BLDC Motor Control
In Sensorless BLDC motor control, back EMF (Electromotive Force) act as the primary source to detect the rotor position. Since BLDC motors are known for their precise commutation, it depends on accurate rotor position detection. Therefore, Back-EMF plays an important role in sensorless BLDC motor control.
Key Roles of Back-EMF are:
- Rotor Position Estimation
Back-EMF provides real-time feedback on the rotor’s position by capturing voltage signals induced in the unenergised phase. It enables precise timing for electronic commutation.
- Sensorless Operation
It eliminates the need for hall sensors and simplifies the motor's structure and enhancing its lifespan.
- Speed Feedback
Since back-EMF amplitude is proportional to speed, it provides a secondary benefit of speed estimation, which can be used in closed-loop speed control algorithms.
Techniques for Back-EMF Sensing in BLDC Motors
Back-EMF sensing is a core technique in sensorless BLDC motor control. It allows for accurate rotor position detection without physical sensors.
Since BLDC motors rely on precise commutation for their operation. Back-EMF sensing becomes a crucial parameter for Sensorless BLDC motor control. There are several techniques for back-EMF sensing:
- Zero-Crossing Detection (ZCD)
It is the most commonly used method for back-EMF sensing. It monitors the unenergised phase and detects the point where the back-EMF voltage crosses the reference level.
It is a simple and cost-effective technique, but its accuracy decreases at low speeds due to weak back-EMF signals.
- Terminal Voltage Sensing with Virtual Neutral
In BLDC motors without a neutral point, a virtual neutral is created using resistor network. It allows for an accurate comparison between the unexcited phase voltage and virtual neutral for zero crossing detection.
- Third Harmonic Voltage Integration
It extracts the third harmonic component from all three-phase voltages. Since the third harmonic of back-EMF is in all phases, its integration gives a signal to estimate rotor position.
- Back-EMF Integration Method
Instead of detecting the zero-crossing point, this technique integrates back-EMF over time. This integration results in crossing a threshold at a consistent rotor position.
- Sensorless Trapezoidal Estimation
Use in digital controllers, this technique samples the phase voltage and determines the rotor position based on expected back-EMF waveforms.
Why Back-EMF is Important in Sensorless BLDC Design
- Rotor Position Detection
The main role of back-EMF in sensorless BLDC motor is determining rotor position. In BLDC motor, commutation must be synchronised with the exact rotor position for precise commutation. Sensorless algorithms monitor the back-EMF waveform of the unpowered phase to estimate the zero-crossing point.
- Cost and Reliability Advantage
By using back-EMF as a feedback mechanism, the system eliminates the need for an additional sensor, which reduces cost and design complexity.
- Speed Estimation
Back-EMF amplitude is proportional to the motor speed. It provides a natural and real-time way to estimate and monitor motor speed without an external tachometer. This information is used in feedback loops for close-loop control systems.
- Energy Efficiency
Using back-EMF allows for precise commutation, which improves efficiency and torque of the motor. Poorly timed commutation, inefficient feedback result in high current and decrease the efficiency.
Applications Benefiting from Sensorless Back-EMF Control
Sensorless BLDC motor control using back-EMF has become a preferred choice across various applications due to its low cost, compact design and high reliability. Below are some key applications that benefit significantly from this approach:
- Cooling Fans and HVAC Systems
Sensorless BLDC motor control is widely used in fans, air conditioners, and ventilation units. These systems typically run at a constant speed and make Back-EMF ideal for precise control.
- Drones and UAVs
In Drones and UAVs, every gram matters. Sensorless motor control reduces weight by eliminating hall sensors and connectors. At high operating speed, back-EMF signals are strong and stable, allowing for precise commutation and battery life.
- Pumps and Compressors
Applications like pump and compressors benefit from sensorless BLDC motor control due to their high efficiency and low maintenance. These motors operate in a compact environment where placing physical sensors is impractical.
- Electric Vehicles (EVs) and E-Bikes
Sensorless control is commonly used in low-cost EVs, scooters, and e-bikes. The sensor may be used for start-ups, while sensorless control is used for high speed for better efficiency.
Conclusion
Back-EMF is the cornerstone of sensorless BLDC driver design. By accurately interpreting the voltage induced in unpowered motor phases, engineers can achieve reliable rotor position detection without using physical sensors. This not only reduces system cost and complexity but also enhances reliability in demanding environments.
While challenges like low-speed performance and noise must be addressed through careful design, the benefits of Back-EMF sensing far outweigh the drawbacks.
As control algorithms and processing power evolve, sensorless BLDC motors will continue to drive the future of efficient and compact motion systems.