Working Principle of BLDC Motor (Brushless DC Motor): Diagram & Explanation
The working principle of BLDC motors (Brushless DC Motor) is based on the Lorentz force law, which involves the interaction of the stator's magnetic field with the rotor's permanent magnet to rotate the rotor and enable the BLDC motor to produce mechanical power.
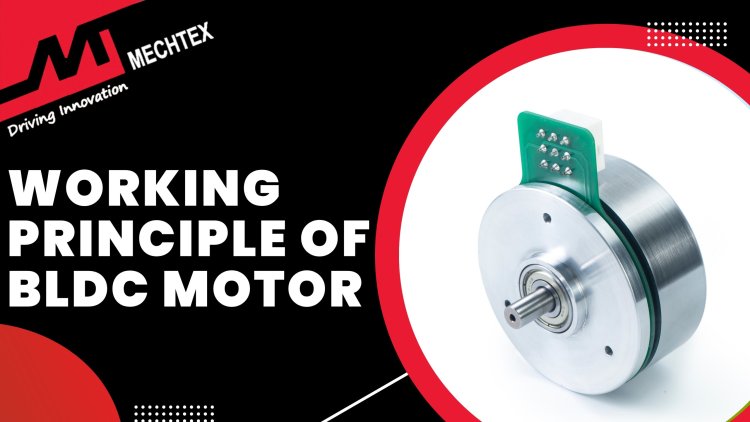
“BLDC motors represent the pinnacle of modern motor technology, by offering efficiency, reliability, and precision at once.
A Brushless DC motor (BLDC) is an advanced electric motor that operates without brushes, offering high efficiency, long life, and precise control. In this blog, we will explore the working principle of BLDC motor, Construction of BLDC motor with diagram, and real-world applications.
What is a BLDC Motor
A BLDC motor is an electric motor that operates without mechanical brushes and commutators found in traditional DC motors. In traditional DC motors, brushes and commutators are essential for directing current to the motor winding. This method involves physical contact of brushes and the commutator, which leads to friction and wear and tear. However, BLDC motors use electronic controllers to manage the direction of current in the stator’s winding. It allows for more precise control, high efficiency and long lifespan of these motors.
A BLDC motor consists of a stator, rotor and electronic controller. The stator is the stationary part of the BLDC motor and consists of 3-phase windings, generate a rotating magnetic field. The rotor is the rotating part of the BLDC motor and consists of permanent magnets. The rotor aligns with the stator and rotates along with the rotating magnetic field, which enables it to produce torque. Electronic controllers are used to switch the direction of current in the stator winding in a specific sequence.
Watch the YouTube Video by "Electrical lectures" about BLDC Motors
The BLDC motor operates with the help of the electronic commutation method instead of using mechanical brushes and commutators. The electronic controller switches the direction of the current into the stator’s winding, which creates a magnetic field. The rotor interacts with the magnetic field of the stator and starts to rotate. The hall sensor detects the position of the rotor and provides feedback to the electronic speed controller. On the basis of feedback, the electronic speed controller sequentially energises the stator’s winding to create a magnetic field and drive the rotor.
BLDC motors offer several advantages over their brushed DC motors. They are highly efficient, as they offer greater power output, which is particularly advantageous in battery-powered applications where energy conservation is crucial.
Additionally, BLDC motors exhibit smoother operation and produce less electromagnetic interference, making them suitable for applications requiring precise motion control and minimal electrical noise.
BLDC motors find widespread use across various industries and applications. BLDC motors power electric vehicles, drones, and actuators, providing efficient and reliable propulsion systems. In robotics and automation, they drive robotic arms, conveyor systems, and CNC machines with precision and agility.
BLDC motors also feature prominently in consumer electronics, powering devices such as computer cooling fans, hard disk drives, and household appliances.
Also Read
Construction of BLDC Motor
A BLDC motor is an electric motor that uses direct current to operate without any brushes or a commutator. Each component of the BLDC motor works together to ensure smooth and efficient operation.
Here are some key components of BLDC motors:
- Stator
It is the stationary part of the motor. It consists of a 3-phase copper winding arranged around the iron core and generates a rotating magnetic field.. When current flows through these windings, it generates a rotating magnetic field that interacts with the rotor’s magnetic field.
- Rotor
It is the rotating part of the motor. It is made up of permanent magnets arranged in alternating north and south poles. The rotor aligns and rotates with the stator magnetic field, which enables torque production. Depending on the design, the rotor may be inside the stator (inrunner) or surround it (outrunner).
- Electronic Speed Controller (ESC)
The ESC is a crucial component in the operation of the BLDC motor. It electronically commutates the motor by controlling the flow of current in the stator’s winding based on feedback from hall sensors.
Also Read
Working Principle of BLDC Motors
Working Principle of BLDC Motors
The working principle of BLDC motors relies on electronic commutation using an ESC (electronic speed controller). It is based on the Lorentz force law. It involves the interaction of electromagnetic fields with their components to produce rotational movement of the motor. It is dependent upon its three main components: rotor, stator, and electronic speed controller.
The stator is the stationary part of the motor and is made up of electromagnets (stator magnets) arranged in a specific pattern. These electromagnets are also known as stator windings.
The number of stator winding and their arrangement determines the speed, torque, and direction of the BLDC motor and are responsible for creating a magnetic field that causes rotation. This winding is connected to a DC power supply and energised in the sequences with the help of electric controllers.
The electronic commutation process energises the stator coil in a specific sequence based on the rotor position, enabling rotation without mechanical brushes.
The rotor is the moving part of the BLDC motor and generates the mechanical power. It is a complex and sophisticated component that consists of a permanent magnet arranged in alternating north and south poles and is surrounded by stator winding.
When stator windings are energised in a specific sequence, it creates a rotating magnetic field. This rotating magnetic field interacts with a permanent magnet in the rotor and causes the rotor to rotate and enabling the BLDC motor to produce mechanical power. This interaction, where the rotor aligns with the stator's rotating magnetic field, is the basis of torque generation in BLDC motors.
The speed and torque of the brushless DC motor can be controlled by adjusting the time and duration of the power supply with the help of a controller. The controller plays a crucial role in the working of the BLDC motor. It uses sensors such as Hall effect sensors or sensorless methods (by using encoders or back-EMF) to detect the position of the rotor.
After detecting the position of the rotor, it energised the stator winding in a particular sequence. This feedback system ensures precise commutation and smooth operation. As the motor spins, it generates back EMF (Electromotive Force), which is used in a sensorless control system to determine rotor position and enhance efficiency.
It also adjusts the current and voltage of the BLDC motor to ensure the motor rotates at a constant speed and torque even under varying load conditions. It not only improves the performance of the motor but also increases the life span of the motor, making them an ideal solution for various applications where control over the speed and torque of the motor requiring efficient speed and torque control.