Advantages and Disadvantages of Brushless DC Motor (BLDC Motor)
BLDC Motor is a type of electric motor that operates on direct current. It is also known as a brushless DC motor. The primary advantages of BLDC motors are: High Efficiency, Long Lifespan, Precise Speed Control. Quiet Operation. Despite Various advantages, some disadvantages are: High Cost, Complex Electronic Control Systems.
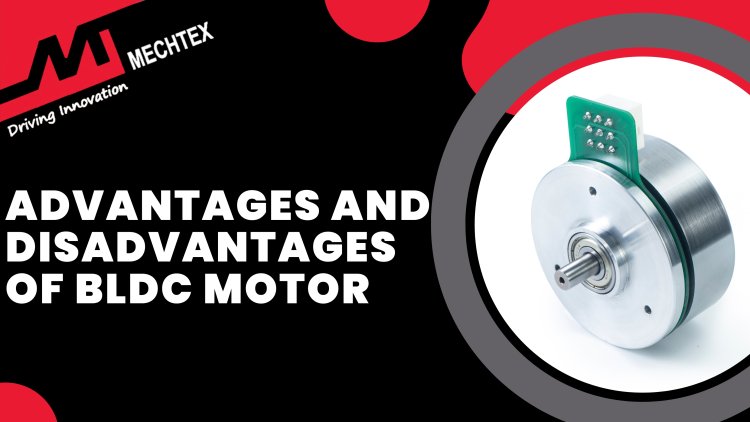
“Brushless DC motors: Efficiency in motion, reliability in operation, and precision in performance, driving force behind the progress of various applications”
In this blog, we explore the advantages and disadvantages of BLDC motors, from shedding light on their remarkable efficiency, reliability, and precision, we will also discuss the challenges they pose in various applications. Whether you're an engineer, or tech enthusiast, join us as we uncover the important benefits of BLDC motors and their impact on industries ranging from automotive to consumer electronics.
What is BLDC Motor?
BLDC Motor is a type of electric motor that operates on direct current. It is also known as a brushless DC motor, unlike traditional DC motors, which use a commutator and brushes to switch the direction of current. BLDC motor uses electronic commutation to switch the direction of the current. This advanced design of BLDC motors eliminates the need for brushes and commutators and increases the efficiency and reliability of these motors.
A BLDC motor consists of a stator, rotor, hall sensors, and motor controllers. The stator is the stationary part of the motor and contains windings. These windings are energised in a specific sequence to generate the magnetic field to interact with the rotor.
The rotor is the rotating part of the motor. It consists of permanent magnets arranged in specific patterns. These permanent magnets interact with the magnetic field produced by the stator and cause the rotor to rotate.
Hall sensors in the BLDC motor detect the position of the rotor and send the information to the BLDC motor controller. Based on this information, the BLDC motor controller regulates the timing and sequence of current passes to the stator’s winding, offering precise speed control and excellent torque, making them suitable for various industrial and commercial applications.
Also Read
Advantages of BLDC Motors
BLDC motors are electric motors that use electronic commutation devices to operate efficiently. BLDC motors offer numerous advantages over traditional brushed motors.
Some of the important advantages of BLDC motors are as follows:
- High Efficiency
The high efficiency of BLDC motors offers numerous advantages to various applications. In industrial applications such as conveyor belts where continuous operation is required, BLDC motor consumes less electrical power for the same mechanical power resulting in more energy saving and less operation cost in production.
In applications such as electric vehicles, drones, and portable devices where long operations are required, the high efficiency of the BLDC motor extends its battery life and improves the user experience.
Micro BLDC motors are commonly used in portable devices and compact applications, offering exceptional performance while maintaining small size and low power consumption.
- Long Lifespan
BLDC motors are designed without the brushes and components that lead to wear and tear which results in a longer lifespan of BLDC motors. This extended life span of the BLDC motor is an advantage to various applications.
In industries such as automotive where reliability is important, BLDC motors offer low maintenance needs and long operational lifespan which ensures vehicles spend less time in maintenance and repair and remain operational for longer periods.
In consumer electronics, BLDC motors provide longer-lasting performance in devices like household appliances, power tools, and many more. The extended life span of the BLDC motor reduced maintenance requirements, and replacement opportunities and improved the user experience.
In renewable energy systems and industrial automation where reliability and efficiency are required in operations. The long lifespan of the BLDC motor minimises downtime and maintenance costs and, maximises system uptime and productivity of the application.
- High Power Density
The higher power density of the BLDC motor means the ability of the motor to deliver mechanical power in relation to its size and weight compared to other types of motor. This feature offers numerous advantages to diverse applications of various industries.
In electric vehicles, drones, and portable electronics where space is constrained, BLDC motors offer high power density with low energy consumption. It results in improving the efficiency and battery life of these devices for long operations.
In industrial automation and robotic systems, BLDC motors with higher power density play a crucial role in meeting their demanding requirements for operation. With greater output torque and faster acceleration relative to their size and weight, these motors enable industrial automation and robotic systems to perform tasks more efficiently and effectively.
In CNC machines, accurate positioning and fast acceleration lead to shorter cutting times and increased productivity of machines.
Large BLDC motors are used in heavy-duty applications such as industrial machinery, providing the necessary torque and power to handle large workloads while maintaining high efficiency.
- Precise Speed Control
Precise speed control is the key advantage of the BLDC motor. It is facilitated by an electronic commutation system. It involves adjusting and controlling the speed of the motor as per application requirements. This precise speed control makes the BLDC motor suitable for various applications.
In applications such as robotics, CNC machines, and medical devices, precise speed control ensures consistent and repeatable movement, which leads to higher precision and accuracy in the performance of applications.
In HVAC systems and electric vehicles, precise speed control of BLDC motors enables optimal airflow regulation and energy utilization, contributing to improved comfort and user experience.
Small BLDC motors are used in compact devices such as fans and pumps, offering efficient speed control in space-constrained environments without compromising performance.
- Quiet Operation
The quiet operation of the BLDC motor is an advantage to various applications as the motor operates at a low noise level for better performance.
In consumer applications such as air conditioners, refrigerators, and fans BLDC motors quiet operation boosts the user experience by reducing the disruptive noise level and creating a more pleasant and comfortable environment.
In healthcare applications such as pumps, analyzers, and ventilation systems BLDC motors quiet operation ensures efficient and reliable performance of applications for patient’s speedy recovery.
In automotive applications such as electric vehicles and hybrid cars, BLDC motors quiet operation results in less vibration and ensures stability and a smooth riding experience for the users.
Disadvantages of BLDC Motors
Despite the offering of numerous advantages to various applications, BLDC motors have some disadvantages that affect the performance of various applications.
Some of the major disadvantages of BLDC motors are:
- High Cost
The high cost of BLDC motors is a significant drawback for various applications. In the consumer electronics and automotive sector where cost efficiency is an important factor, higher investment in BLDC motors may affect the price of the application and limit the market share
Similarly in industrial and commercial applications, their stringent budget makes it difficult to justify the cost of BLDC motors. Even though these motors offer several benefits such as high efficiency, precise speed control, and quiet operation. The company may adopt cheaper alternatives.
- Electronic Control Systems
The integration of electronic control systems in BLDC motors is a disadvantage for various applications.
The electromagnetic interference generated by electronic control systems may interfere with electronic devices and cause operational risks. Compatibility issues of this control system may hinder seamless integration and require additional resources and efforts.
Additionally, The cost of integrating these electronic control systems with the help of software may affect the overall expense of various applications.
Lastly, the specialized skill required for programming, troubleshooting, and maintenance of these control systems increases dependency on them. Any failure in control systems may lead to high maintenance costs and long downtime.
- Sensor Dependency
BLDC Motor control systems require hall sensors and encoders to control the speed and torque of the motor. Relying on this sensor or encoders poses a challenge to BLDC motors across a variety of applications.
In industrial automation, where precision and reliability are important any failure in sensors or encoders can affect the production process and lead to high downtime. Similarly, in medical devices dependency on sensors raises concerns, any failure in sensors or encoders affects the operation of the device and causes risk to the patient.
In an HVAC system, BLDC motors offer various benefits such as energy efficiency and precise control over airflow and the speed of fans. However, dependency on sensors may cause an inherent risk to the comfort of users.
Eg - Inaccurate temperature reading by sensors could lead to inefficient operation of BLDC motors and cause the system to overheat and underheat in indoor spaces of users.
High-torque BLDC motors are used in applications requiring more power and stability, such as heavy-duty HVAC systems or industrial machinery, where reliable torque control is essential for smooth, consistent operation.
- Limited High Speed and Torque
The limited high speed and torque of BLDC motors present numerous challenges to various applications.
In electric vehicles and hybrid vehicles, where maintaining performance at high speed is important, BLDC motors may not deliver sufficient torque and impact the acceleration of the vehicle.
Industrial machinery requires high-speed operation in production. However, the BLDC motor’s limited torque at higher speeds may create complexity in the operation and increase the chances of failures.
In HVAC systems, the BLDC motor’s limited high speed and torque lead to compromised airflow and affect the heating and cooling efficiency of the system.
While in power tools and robotics where rapid movements are required, the BLDC motor’s limited high speed and torque may reduce productivity and affect the performance of the application.
- Heat Dissipation
Heat dissipation of BLDC motors is a challenge for various applications. As BLDC motors operate at high speeds, they generate more heat as compared to other motors. The absence of heat dissipation in BLDC motors affects the efficiency and performance of various applications.
In electric vehicles, heat generated by BLDC motors results in loss of energy and inefficiency. This inefficiency affects the overall performance and results in decreased driving range of vehicles.
In renewable energy systems such as wind turbines or solar tracking systems, maximizing energy conversion is important for optimizing power generation. Any inefficiencies in heat dissipation from BLDC motors affect the efficiency of the overall system and lead to lower electricity output.
In Industrial machinery, where continuous operation is required, poor heat dissipation of BLDC motors leads to degradation of components and reduces the motor’s lifespan which increases the risk of downtime and high maintenance costs.