Working Principle of Synchronous Motor
A synchronous motor is a type of AC motor that operates on the principle of synchronism. In this principle, the rotor is synchronised with the frequency of the AC supply and rotates. When the rotor rotates, the EMF creates a magnetic field and causes the rotor to rotate at constant speed.
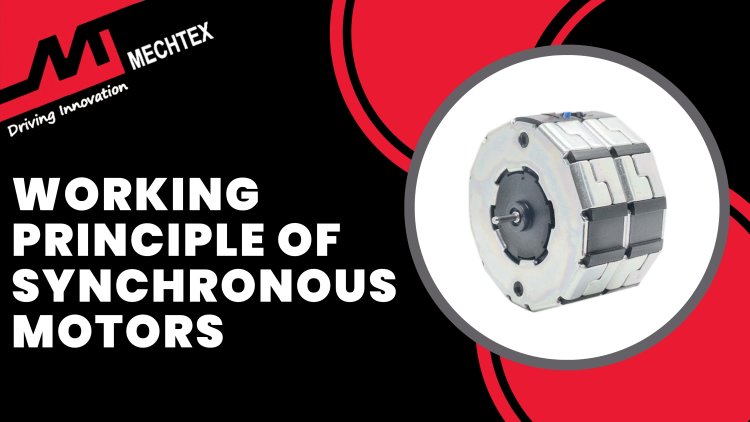
"In synchronous motors, the interaction of magnetic fields ensures rotation stays in perfect rhythm with the alternating current, a testament to precision engineering."
Synchronous motors are a remarkable innovation in electrical engineering, as they combine the elements of both induction motors and direct current motors to deliver exceptional performance and versatility. In this blog, we will uncover the workings principle of synchronous motors, also shedding light on how they synchronize their rotation with the frequency of the alternating current (AC) power supply. Whether you're a beginner or an expert, read this blog to demystify the workings of synchronous motors and appreciate their vital role in powering various applications in the world!
What is a Synchronous Motor?
A synchronous motor is a type of AC motor that operates at a speed directly proportional to the frequency of current supplied. It helps the synchronous motor to maintain synchronous speed regardless of changes in load.
Unlike induction motors, which rely on the principle of electromagnetism and experience a change in speed due to a change in load. However, synchronous motors maintain their synchronous speed with the frequency supply irrespective of changes in load making them ideal for applications that require constant speed control such as clocks, timers, and various industrial processes.
The construction of a synchronous motor includes two main components: stator and rotor. The stator is the stationary part of the motor and consists of three-phase windings similar to the induction motor. While the rotor is the rotating part of the motor, it can be either a salient pole or cylindrical.
Check out a Video by "Electrical Deck" about synchronous motors.
Synchronous motor works on the principle of interaction between the stator and rotor. When a three-phase AC supply is provided to the windings of the stator, they generate a rotating magnetic field (RMF) which interacts with the magnetic field of the rotor, locks the rotor and causes it to rotate at synchronous speed.
However, unlike induction motors, synchronous motors are not self-starting. At idle conditions, the rotor’s magnetic field experiences alternating torque due to the rotating magnetic field (RMF) of the stator, which is insufficient to initiate the rotation of the rotor. To start the rotation, auxiliary methods such as damper windings or an external motor are used to bring the rotor up to synchronous speed before DC excitation is applied.
Also Read
What is a Synchronous Motor | Construction, Working Principle and Applications
Mechtex MTR5 is a 2.1W synchronous motor with voltage options spanning 12V, 24V, 48V, 110V, and 230V and 1.35 Ncm torque at 50/60Hz rated frequencies, making it well-suited for industries such as Pumps and Actuators, and Industrial Machinery.
Working Principle of Synchronous Motor
The working principle of a synchronous motor is based on the concept of synchronism. In this principle, the rotation of the rotor is synchronised with the frequency of the alternating current (AC) supply. Similar to other AC motors, synchronous motors also consist of a stationary part called the stator.
The stator contains wire coils, supplied with an alternating current (AC) supply. When these coils are energised with an AC supply, they produce a rotating magnetic field. This rotating magnetic field helps the rotor to rotate.
The rotor is the rotating part of the motor. It contains either electromagnets or permanent magnets arranged in specific patterns. These magnets are then arranged with a rotating magnetic field produced by the stator. As a result of this interaction, the rotor starts to rotate.
The most important feature of synchronous motors is their ability to maintain constant speed. They have the ability to synchronise the rotation of the rotor with the frequency of the AC supply.
When a three-phase AC supply is provided to the stator, it gets energised and creates a rotating magnetic field (RMF). Then, the DC excited rotor interacts with the rotating magnetic field (RMF) and then locks itself, which causes the rotor to rotate at constant speed. This constant speed is known as synchronous speed.
The Formula for Synchronous Speed - Ns = 120 x f / P,
where
- f is the frequency of the AC supply
- P is the number of poles in the motor.
This formula shows that the speed of a synchronous motor is inherently related to the frequency of the AC power supply, which is typically 50Hz or 60Hz.
Mechtex has a 110V Synchronous motor and a 230V Synchronous Motor that operates at 50Hz or 60Hz frequency. These synchronous motors are used in various industrial machinery, pumps, compressors, wind turbines, and daily life applications.
However, precise speed control is achieved by adjusting the frequency of the AC supply. By increasing or decreasing the frequency of supply, the motor speed can be adjusted to meet the requirements of specific applications.
In some synchronous motors, an additional DC supply is required for the rotor winding to create the magnetic field produced for synchronisation. This process is known as excitation. It helps synchronous motors to maintain their synchronisation with the AC power supply. However, synchronous motors are not self-starting.
How to Start a Synchronous Motor
A synchronous motor is not self-starting as its rotor requires an external source to rotate at synchronous speed. At a standstill condition, the stator of a synchronous motor generates a rotating magnetic field, which results in the creation of alternating torque for the rotor.
Hence, the rotor experiences no motion. Therefore, in order to bring the rotor into motion, various starting methods are used to start a synchronous motor. Some of the key methods are:
- Damper Winding (Amortisseur Winding)
In this method, copper bars are embedded in the rotor poles, forming a squirrel cage-like structure called damper winding. When the motor starts, it operates as an induction motor using this winding to generate torque. As the rotor reaches near synchronous speed, DC excitation is applied to the field winding and allows it to lock with synchronous speed.
- Pony Motor (Auxiliary Motor)
In this method, a small external motor is coupled with the shaft of the synchronous motor. This external motor is called a pony motor or auxiliary motor. These motors are used to bring the synchronous motor near to the synchronous speed. Once the synchronous motor reaches the synchronous speed, the pony motor is disconnected from the synchronous motor. The DC excitation is applied to the rotor winding of the synchronous motor to maintain its synchronous speed.
- Variable Frequency Drive (VFD)
A variable frequency drive (VFD) is used to start a synchronous motor by gradually increasing the supply frequency from zero to its rated value. This controlled acceleration of frequency allows the rotor to speed up and reach its synchronous speed. Once the rotor reaches its synchronous speed, a DC excitation is applied to allow the synchronous motor to run efficiently.
Also Read
Why Synchronous Motor is not Self-Starting
Types of Synchronous Motors
Synchronous motors are classified based on rotor construction and excitation method. These types cater to various industrial applications where constant speed and high efficiency are essential. Types of Synchronous Motors are:
- Reluctance Synchronous Motor
This synchronous motor uses a rotor with variable reluctance. The rotor aligns with the rotating magnetic field to minimise the reluctance, which makes it suitable for low-power applications used for precision control tasks.
- Permanent Magnet Synchronous Motors (PMSM)
This synchronous motor has permanent magnets embedded in the rotor to create a rotating magnetic field. This eliminates the need for external excitation and produces a constant magnetic field. This motor offers high efficiency, compact design and excellent performance. PMSM motors are widely used in applications that require precise control, such as robotics, electric vehicles, CNC machines, and HVAC systems.
- Hysteresis Motor
This synchronous motor uses a rotor made up of hard magnetic materials that retain magnetism. In this motor, the torque is generated through the hysteresis effect as the rotor lags behind the stator field. It offers smooth, silent and vibration-free operation with any DC excitation, which makes them ideal for applications like electric clocks, timing devices, audio equipment, and precision instruments.
Also Read
Applications of Synchronous Motor
A synchronous motor is an electric motor that operates at a constant speed with the frequency of AC supply irrespective of change in load, which makes it ideal for various applications.
Here are the most common applications of synchronous motor
Synchronous motor plays an important role in driving industrial machinery such as conveyor systems, mixers, extruders, machine tools, printing presses, and packaging machinery, where constant speed operation is essential for efficiency.
- Power Generation Pump
Synchronous motors are used in power plants to drive large generators or pumps and improve the power factor correction to enhance the efficiency of the power generation plants.
- Pumps
Synchronous motors are used in the pump system to drive the rotor of the pump and maintain constant fluid flow.
- Clock and Timer
Synchronous motors are used in clocks and timers to ensure accurate time-keeping over extended periods without any fluctuations.
Also Read
Applications of Synchronous Motor