Understanding Back-EMF in Stepper Motors
Back-EMF (Electromotive Force) is a voltage generated in the windings of a stepper motor as the rotor moves through the magnetic field. It plays a significant role in the performance and control of stepper motors. Understanding it is crucial for optimising the stepper motor's performance in various applications.
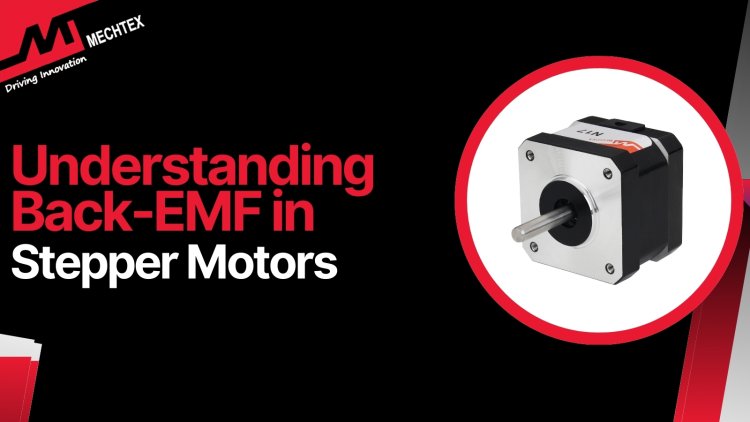
Stepper motors are widely used in applications requiring precise motion control such as 3D printers, robotics, and CNC machines. A crucial phenomenon in the operation of a stepper motor is Back-EMF (Back Electromotive Force). Understanding Back-EMF is essential for optimising the performance of the stepper motor ensuring system stability and implementing advanced techniques.
In this blog, we will explore what back-EMF is, its role in stepper motors, and how it affects their performance.
What is Back-EMF?
Back-EMF (Back Electromotive Force) is a voltage generated in an electric motor due to its motion. It arises due to electromagnetic induction as described by Faraday’s law and its inherent phenomenon in any system involving a rotating coil within a magnetic field.
In a motor, when a current flows through the windings, it creates a magnetic field that interacts with the rotor causing it to spin. As the rotor rotates, the motion within the magnetic field induces a voltage in the winding. This induced voltage is termed "back EMF" because it opposes the applied voltage driving the motor.
Watch the YouTube video by "PhysicsHigh" to learn the relationship between back-EMF and stepper motors.
The back-EMF is directly proportional to the speed of the motor. At startup, when the motor is stationary, there is no back-EMF, ensuring maximum current flow through the windings. As the motor speeds up, the back EMF increases, naturally limiting the current.
The mathematical expression for back-EMF can be given by Eb=Ke⋅ω
Where:
- Eb= Back-EMF (volts)
- Ke= Back-EMF constant (volts/rad/s)
- ω = Angular velocity of the rotor (rad/s)
This self-regulating behaviour is critical for stepper motor performance, influencing the current drawn and efficiency of the system. Back EMF is a key consideration in the design of stepper motors and drives, to ensure stability and efficient operation across various applications.
How Back-EMF Arises in Stepper Motors?
The stepper motor functions by sequentially energising coils to rotate the rotor step by step. As the rotor moves, the relative motion between the rotor and stator magnetic field induces back-EMF in the windings.
This back-EMF acts against the input voltage, which influences stepper motor behaviour. Here are some reasons for the rise of back-EMF in stepper motors:
- Rotor Speed
The back-EMF in the stepper motor is directly proportional to rotor speed. As the rotor spins fast, the relative motion between the rotor and stator magnetic field increases and induces greater back-EMF.
- Magnetic Field Strength
The strength of the stator and rotor magnetic field influences back-EMF generation. A stronger magnetic field induces a large voltage when the rotor moves. This is why high-quality materials and optimised magnetic designs are essential for efficient stepper motor performance.
- Winding Configuration
The design of the coil includes the number of turns which affect back-EMF. More turns create higher induced voltages while the wire gauge and resistance determine energy losses. Optimising winding configuration balances torque, efficiency, and speed capabilities.
- Load Conditions
The load on the stepper motor impacts back-EMF. Heavier loads slow the rotor, reducing back-EMF, while lighter loads allow faster speeds, increasing it.
Role of Back-EMF in Stepper Motors
Back-EMF (Electromotive Force) is a voltage generated in the windings of a stepper motor as the rotor moves through the magnetic field.
This phenomenon plays a significant role in the performance and control of stepper motors. Understanding its role is crucial for optimising motor performance in various applications.
- Speed Detection
Back-EMF is directly proportional to the rotor’s speed which makes it a valuable parameter for speed detection of stepper motors.
By monitoring back-EMF, the rotor’s speed can be determined without the need for additional sensors. This characteristic is beneficial in sensorless control systems where reducing complexity and cost is a priority while maintaining accurate speed control.
- Position Feedback
Variations in back-EMF can reveal discrepancies between the commanded position and the actual position of the rotor.
These variations provide critical feedback in closed stepper motors ensuring precise positioning and reliable operation even under varying load conditions. This makes back-EMF an integral part of enhancing the accuracy of the stepper motor.
- Motor Protection
During rapid deceleration or over-speed conditions, excessive back-EMF can be generated potentially harming the driver circuit. To mitigate this risk, proper design and control strategies are implemented to manage back-EMF levels effectively ensuring safety and longevity of the stepper motor.
- Efficiency Analysis
The magnitude of back-EMF can serve as an indicator of energy conversion efficiency. High-back EMF at a certain speed reflects efficient energy usage, whereas low-back EMF reflects suboptimal performance or mechanical load on the stepper motor.
This makes a back-EMF monitoring tool for evaluating stepper motor performance and identifying areas of improvement.
Effects of Back-EMF on the Performance of Stepper Motor
The effects of back-EMF on the performance of a stepper motor are profound, influencing its speed, torque, efficiency, and overall behaviour. Here's a breakdown:
- Limits on Maximum Speed
As the speed of the rotor of the stepper motor increases, back-EMF also increases which opposes the applied voltage. This opposition reduces the effective voltage available to drive the stepper motor, consequently decreasing the torque.
This establishes a trade-off between speed and torque, ultimately defining a practical limit on the stepper motor's maximum speed.
- Reduction in Torque
At higher rotor speed, the elevated back-EMF reduces current flowing through stepper motor winding. Since torque is directly proportional to the winding current, this results in reduction of torque at a higher speed.
Such limitation impacts the stepper motor's ability to perform in applications that require both high speed and high torque simultaneously.
- Dynamic Behaviour
Back-EMF plays a critical role in the stepper motor’s ability to maintain synchronisation with input pulses. At elevated speeds, an increase in back EMF can cause the stepper motor to lose its synchronisation which leads to reduced potential accuracy.
To counter this behaviour, stepper motor drivers need to be designed to compensate for back-EMF and ensure reliable operation.
- Impact on Efficiency
The magnitude of back-EMF can indicate the efficiency of energy conversion within the stepper motor. When the stepper motor operates within its optimal speed range, the motor generates back-EMF proportional to the input voltage, which is a hallmark of efficient operation.
However, operating outside this range can lead to inefficiencies, heat generation, and energy losses, all of which degrade overall motor performance.
- Effect on Control Systems
Back-EMF serves as a feedback parameter in the sensorless control system. Variations in back-EMF are used to dynamically adjust the applied voltage and current allowing for smooth and accurate operation.
Without proper management, excessive back-EMF can complicate control strategies, particularly at high speed affecting the overall stability and performance of the stepper motor.
Conclusion
Back-EMF is a fundamental aspect of stepper motor operation, influencing speed, efficiency, and accuracy. By understanding its principles, effects, and control methods, engineers can design systems that effectively utilise back-EMF, achieving optimal performance. Whether managing high-speed applications or implementing energy recovery, back-EMF remains a key consideration in stepper motor technology.