Back-EMF on BLDC Motors : A Complete Guide
Back-EMF on BLDC motor is a natural feedback mechanism, that helps the BLDC motor to regulate its speed, optimise efficiency, and enable sensorless control for smooth operation. It provides feedback about the rotor’s position to allow precise control without any external sensors.
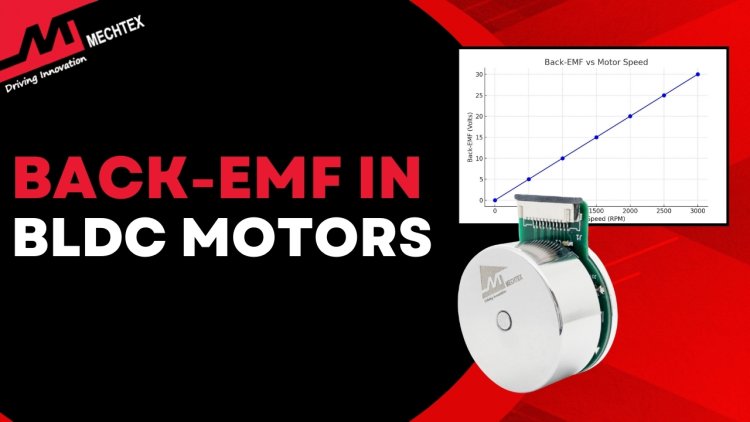
BLDC motor is a modern, advanced electric motor that operates using electronic commutation. Unlike traditional DC motors, which use brushes and commutators, BLDC motors use electronic commutation with the help of Hall sensors and encoders. BLDC motors consist of a rotor made up of permanent magnets, and the stator contains coils that are energised in sequence. This sequencing is controlled through a driver circuit to eliminate the need for brushes and commutators, enabling smooth and efficient operation. It makes BLDC motors ideal for applications where precision, speed control, and long operational life are required.
One of the key concepts that play a crucial role in the smooth and efficient operation of the BLDC motor is the back electromotive force (back - EMF). Understanding back-EMF is essential for optimising the BLDC motor's performance, achieving precise control and ensuring long operational life. In this blog, we will explore what back-EMF is, how it is generated in BLDC motors, its effect, and why it is important in BLDC motor control.
What is Back - EMF?
Back - EMF also known as back electromotive force is a voltage generated in electric motors, especially in BLDC motors due to the motor’s rotation. As the BLDC motor’s rotor turns within a magnetic field, it induces a voltage in the stator’s winding that opposes the applied voltage. It is a consequence of Faraday's Law of Electromagnetic Induction, which states that a change in magnetic flux through a conductor induces an electromotive force (EMF).
In the BLDC motor’s back - EMF is important for the motor’s operation and precise control. It provides feedback about the rotor’s position to allow precise control without any external sensors.
Watch the YouTube video by "Gaurav J - TheElectricalGuy" to know how back-EMF works in BLDC motor
The magnitude of back-EMF is directly proportional to the BLDC motor’s speed as the rotor’s speed increases back-EMF speed also increases. This characteristic limits the speed of the BLDC motor as back-EMF eventually balances out the applied voltage, reducing the current flow. This makes back-EMF an important concept that enables the efficient and compact design of BLDC motors.
Types of Back-EMF Waveforms in BLDC Motors
The waveform of back-EMF in BLDC motors depends upon its design. The two most common types of back-EMF waveforms are:
- Trapezoidal Back-EMF
This is the most common type of back-EMF waveform in BLDC motors with trapezoidal winding distribution. These types of BLDC motors are designed to produce a back-EMF waveform that matches the current applied to windings for smooth commutation.
- Sinusoidal Back-EMF
Some BLDC motors have sinusoidal winding, resulting in a sinusoidal back-EMF waveform. BLDC motors are often controlled using Field-Oriented Control (FOC) for smoother torque characteristics.
Generation of Back-EMF in BLDC Motors
Faraday’s Law of Electromagnetic Induction governs the generation of back-EMF in BLDC motors. As the rotor spins, the magnetic flux link between the rotor’s magnet and the stator’s winding will change. This change in magnetic flux induces a voltage across the stator’s windings proportional to the rotor's speed. The back-EMF waveform in the BLDC motor is typically trapezoidal, corresponding to the commutation method and winding arrangement of the BLDC motor.
The mathematical expression for back-EMF can be given by Eb=Ke⋅ω
Where:
- Eb= Back-EMF (volts)
- Ke= Back-EMF constant (volts/rad/s)
- ω = Angular velocity of the rotor (rad/s)
Let's assume the following values:
Ke​=0.05V/rad/s
ω=200rad/s
Eb​= 0.05V/rad/s × 200rad/s
Eb​=10V
So, when the BLDC motor's rotor rotates at an angular speed of 200 rad/s, with a back-EMF constant of 0.05 V/rad/s, the generated back-EMF is 10 volts. This back-EMF opposes the applied voltage, and its value increases as the speed of the motor increases.
Importance of Back-EMF in BLDC Motor Control
Understanding back-EMF is crucial for designing effective motor control strategies for BLDC motors. Here are some key reasons why back-EMF is important in BLDC motor control:
- Speed Control
The direct relationship between the back-EMF and the rotor’s speed allows for precise speed control in BLDC motors. By measuring the back-EMF, the controller can accurately adjust the BLDC motor’s speed. This ability is important in applications like electric vehicles, drones and industrial automation where precise speed control is required.
- Protection Against Overspeeding
Back-EMF provides an inherent mechanism for protecting BLDC motors from over-speeding. As the motor’s speed increases, the back-EMF rises and limits the amount of current flowing through the motor. This reduces the risk of damaging the BLDC motor’s winding and other components and ensures safe operation.
- Optimising Efficiency
By utilising back-EMF feedback, BLDC motors can operate more efficiently as the controller adjusts the timing of commutation to minimise the power loss during the operation. This improves the overall performance of the BLDC motor and extends its lifespan.
- Regenerative Braking
In some applications, back-EMF is used for regenerative braking, where the energy generated during the break is fed back into the power supply or battery. This feature is important in electric vehicles or battery-powered systems where energy efficiency is important.
Effects of Back-EMF on BLDC Motor Performance
Back-EMF or Back Electromotive Force plays a crucial role in determining the control and performance of BLDC motors. However, it also affects the performance of the BLDC motor. Here are some key effects:
- Speed Regulation
Back-EMF is directly proportional to the BLDC motor’s speed. As the speed increases, the back-EMF rises and opposes the applied voltage. This limits the BLDC motor’s speed and creates a natural balance between applied voltage and back-EMF which results in speed regulation.
- Current Limitation
Back-EMF controls the flow of current into the BLDC motor’s winding. As back-EMF increases with the speed, it reduces the voltage across the BLDC motor and reduces the current. This process ensures that the BLDC motor does not draw excessive current and protects it from overheating and damage.
- Torque Generation
Since the back-EMF opposes the applied voltage, it affects the torque production capacity of the BLDC motor. High Back-EMF at high speed, draws less current and results in low torque production. This inverses the torque-speed relationship of the BLDC motor and makes it non-linear.
- Control Complexity
The presence of back-EMF affects the controllability of the BLDC motor especially in sensorless operations. Sensorless control BLDC motors rely on back-EMF detection for commutation timing. It requires precise algorithms to maintain speed operation and avoid miscommunication at various speeds which makes the controllability of the BLDC motor more complex.
Also Read
Sensorless Control Techniques for BLDC Motors
Conclusion
Back-EMF is a fundamental characteristic of BLDC motors that significantly impacts their operation and control. It acts as a natural feedback mechanism, helping to regulate motor speed, optimize efficiency, and enable sensorless control. While challenges like low-speed control and waveform distortion exist, proper understanding and management of back-EMF can unlock the full potential of BLDC motors in various applications. For anyone working with BLDC motors, appreciating the role of back-EMF is key to achieving optimal performance and durability.