Why Synchronous Motor is not Self Starting
A synchronous motor is an AC motor that operates using an AC supply. It is not self-starting as it requires external means to bring the rotor to near synchronous speed before it can be synchronised to the power supply. Several starting procedures, such as using pony motors, damper windings, and coupling with a small DC machine, are used to start a synchronous motor.
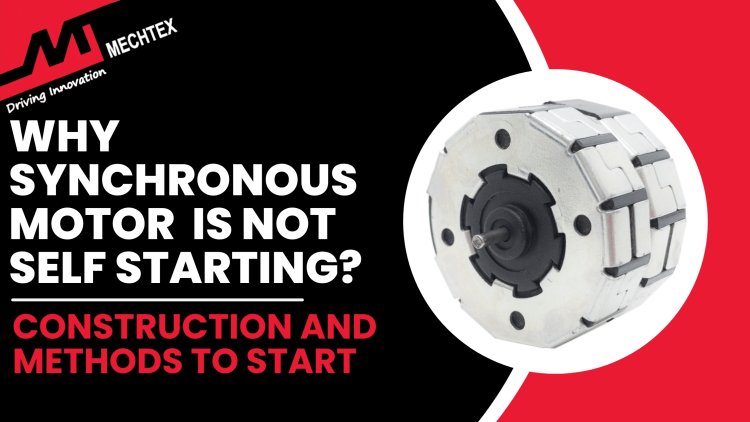
What is a Synchronous Motor?
A synchronous motor is an AC motor that runs at a constant speed synchronised with the frequency of the AC supply. Unlike Induction motors, which experience a slip during the operation. The synchronous operate at a synchronous speed regardless of variation in load. This key feature makes synchronous motors ideal for various industrial applications.
The construction of a synchronous motor consists of two main components: stator and rotor. The stator is the stationary part of the motor and generates a rotating magnetic field. The rotor is the rotating part of the motor which interacts with the stator’s rotating magnetic field and creates movement.
The working principle of a synchronous motor is based on the interaction between the magnetic fields of the stator and rotor. When AC power is supplied to the stator, it creates a rotating magnetic field. At the same time, the rotor is excited with DC power using external sources and creates a magnetic field. Then the rotor interacts and locks itself with the stator’s magnetic field to ensure synchronous speed movement.
The speed of the synchronous motor is determined by the frequency of the AC supply and the number of poles in the motor using the following formula:
Ns = 120xƒ/P
where,
ƒ is the frequency of supply and P is the number of poles of the motor.
Synchronous motors are widely used in applications where constant speed is essential, such as industrial machines, robotics, conveyors, and precision automation systems. Their ability to maintain a steady speed under varying loads makes them ideal for such environments. Additionally, they are used in power factor correction applications to improve the efficiency of power systems.
Construction and Working of Synchronous Motor
A synchronous motor consists of the following components. Read ahead to find out how a synchronous motor functions. Check out the video below by "learnchannel" for a better understanding of how synchronous motors work.
-
Stator
The stator is the stationary part of the motor and consists of a set of electromagnets, typically evenly spaced around the inner circumference. These electromagnets are energized with AC voltage, creating a rotating magnetic field.
- Rotor:
The rotor is the rotating part of the motor and contains a set of permanent magnets or electromagnets. In the case of permanent magnets, they establish a fixed magnetic field. For electromagnets, the rotor field can be excited using direct current (DC) to create a magnetic field.
- Synchronisation:
The synchronous motor rotor must be designed to rotate at the same speed as the rotating magnetic field of the stator. The speed of the rotating magnetic field (synchronous speed) is determined by the frequency of the AC supply and the number of pole pairs on the stator.
- Magnetic Interaction:
When the stator's rotating magnetic field interacts with the fixed magnetic field of the rotor, they try to align with each other due to the magnetic attraction and repulsion forces. This alignment exerts torque on the rotor, causing it to rotate.
- Constant Speed:
As long as the synchronous motor is connected to a stable AC power supply and the load on the motor is within its capabilities, the rotor will maintain synchronisation with the rotating magnetic field of the stator. Thus, the motor will operate at a constant speed, the synchronous speed, regardless of the load.
- Starting:
Synchronous motors need some method to bring them up to synchronous speed when they are initially turned on since they cannot start on their own. This can be done using auxiliary devices like a small induction motor (synchronous motor starting as an induction motor) or external means like DC excitation to establish the rotor's magnetic field before synchronization.
Also Read
Working Principle of Synchronous Motor
Why is a Synchronous Motor not Self-Starting?
Unlike induction motors, which are self-starting due to the rotating magnetic field produced by the stator, synchronous motors require external means to start. AC synchronous motors consist of a stator with three-phase windings and a rotor that is excited by a DC supply. The three-phase windings in the stator create a rotating magnetic field, while the DC supply provides a constant flux.
However, the torque produced on the rotor of a synchronous motor is pulsating and not uni-directional. This pulsating torque is a result of the varying polarity of the rotor and stator poles. At any given instant, the rotor and stator poles can have the same polarity (N-N or S-S), causing a repulsive force on the rotor.
Where,
Nr= North Rotor Pole
Sr= South Rotor Pole
Ns= North Stator Pole
Ss= South Stator Pole
In the next instant, the polarity can be N-S, resulting in an attractive force. However, due to the inertia of the rotor, it remains in a standstill condition and is unable to rotate in any direction. The direction of the instantaneous torque on the rotor reverses after a half cycle, further preventing the motor from starting on its own.
Methods for Starting Synchronous Motors
One key limitation of synchronous motors is that they are not self-starting. Unlike induction motors, synchronous motors require external means to bring the rotor to near synchronous speed before they can be synchronised to the power supply. Let's explore the reasons behind this limitation and examine the different methods used to start synchronous motors.
-
Using Pony Motors:
The pony motor method involves using a separate motor, known as a pony motor, to drive the main synchronous motor up to near synchronous speed. The pony motor is initially used to bring the rotor to a speed close to the synchronous speed. Once the rotor is near synchronous speed, the main motor is synchronised to the power supply.
The DC excitation is then switched on, causing the rotor field and stator fields to "lock in" and establish magnetic locking. At this point, the pony motor can be disconnected, and the main motor continues to run at synchronous speed.
-
Utilizing Damper Windings:
Another method to start a synchronous motor is by utilising damper windings. When the three-phase supply is switched on, the motor initially runs up as a normal squirrel cage induction motor. The damper windings, also known as amortisseur windings, consist of short conductors embedded in the rotor.
These windings provide starting torque to the motor and help it reach synchronous speed. Once the motor reaches synchronous speed, the DC excitation is applied to the rotor, and the motor operates as a synchronous motor.
-
Coupling with a Small DC Machine:
In some cases, a small DC machine can be coupled with the synchronous motor to enable starting. The DC machine is initially made to act as a DC motor, driving the synchronous motor. This helps bring the synchronous motor to near synchronous speed.
Once the rotor is close to synchronous speed, the DC excitation is switched on, and the synchronous motor continues to run at synchronous speed.
-
Using External Means to Rotate the Rotor:
Another approach to starting a synchronous motor is by using external means to rotate the rotor at a speed near or equal to the synchronous speed. This can be achieved by using an external device such as a diesel engine to drive the rotor. Once the rotor is rotating at the desired speed, the DC excitation is applied, and the motor enters synchronous operation.
Starting Procedure for Synchronous Motors
To start a synchronous motor, a specific procedure needs to be followed.
Here is a general step-by-step guide:
1. Provide a three-phase AC supply to the stator windings of the synchronous motor. This creates a rotating magnetic field rotating at synchronous speed (Ns).
2. Use an external means, such as a diesel engine, to drive the rotor at a speed very close to or equal to the synchronous speed. This ensures that the rotor is rotating in the same direction as the rotating magnetic field.
3. Switch on the DC supply to the rotor, which creates rotor poles. At a particular instant, the stator and rotor, unlike poles, will face each other, and their magnetic axes will be near each other. This results in a force of attraction between the poles, pulling them into magnetic locking conditions.
4. Once magnetic locking is established, the rotor and stator poles continue to occupy the same relative positions. The rotor experiences a uni-directional torque in the direction of the rotating magnetic field, causing it to rotate at synchronous speed.
5. Once synchronism is achieved, the external device used to rotate the rotor can be removed. The rotor will continue to run at the same speed as the rotating magnetic field, thanks to magnetic locking.
It is important to maintain the DC excitation of the rotor from a DC power supply as long as the motor is operating to ensure the magnetic locking is maintained.
Synchronous motors offer several advantages in terms of efficiency and control. However, their self-starting limitation necessitates the use of external means to bring the rotor to near synchronous speed before synchronization with the power supply can occur.
Methods such as using pony motors, damper windings, coupling with a small DC machine, or employing external means to rotate the rotor are employed to start synchronous motors. By following the proper starting procedure, synchronous motors can be successfully brought to synchronous speed and operate efficiently in various industrial applications.
Mechtex synchronous motors have several advantages such as high efficiency, low operating cost, constant speed, and easy synchronization with AC supply making them a reliable solution for various applications. If you also want your application to work at a constant speed with high efficiency. Explore our range of AC synchronous motors. We provide tailor-made synchronous motors with gearboxes if required.