Introduction to Encoders
An encoder is an electromechanical device that converts motion into electrical signals. They are classified into several types based on their working principles and output signals. Encoders are widely used across multiple industries.
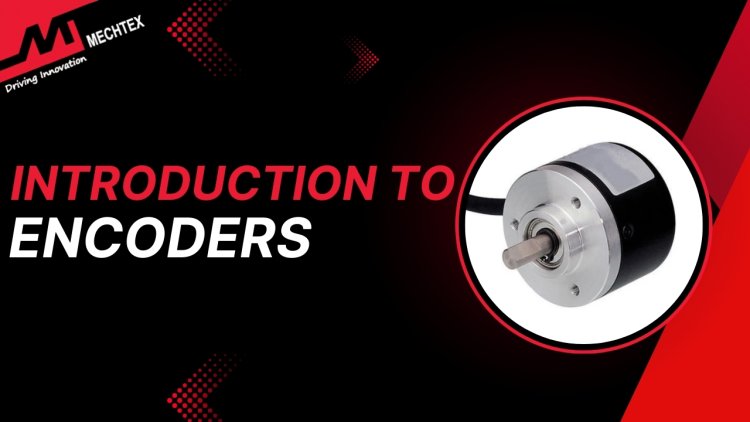
Encoders play a crucial role in automation, robotics, and other motor control applications. They serve as feedback devices that provide precise information about the position, speed, and direction of the rotor to the drivers.
In this blog, we will explore the fundamentals of encoders, their types, working principles, applications, and key selection criteria.
What is an Encoder?
An encoder is an electromechanical device that converts motion into electrical signals for measurement, monitoring, and controlling the position, speed, and direction of the rotor. It provides real-time feedback on parameters such as position, speed and direction, which enables precise motion control in various systems. Encoders are commonly used in automation, robotics, CNC machines, and motor control systems.
Watch the YouTube video by "JAES Company" to know more about Encoders
At its core, an encoder translates mechanical movement into digital analogue signals that can be processed by controllers or microprocessors. This conversion helps ensure accurate positioning, synchronisation, and operational efficiency in motor-driven applications.
By integrating encoders, systems can achieve better repeatability, reduced errors, and optimised performance. The choice of an encoder depends on factors like required resolution, environmental conditions, and system integration needs. Regardless of the application, encoders play a fundamental role in modern motion control and automation technology.
Types of Encoders
Encoders are devices that convert motion into electrical signals for position, speed, or direction control. They are classified into several types based on their working principles and output signals. Here are the main types of encoders:
- Incremental Encoders
Incremental encoders generate pulses as the shaft rotates, indicating a change in position. The controller counts these pulses to track movement, requiring a reference position to start.
These encoders offer high resolution and accuracy making them ideal for applications needing precise motion control.
- Absolute Encoders
Absolute encoders provide values ensuring accurate position tracking even after power loss. Each shaft position is assigned a distinct digital code, allowing immediate position retrieval without requiring a reference reset.
These encoders are available in single-turn and multi-turn versions, offering precise positioning across a wide range of applications. They are more expensive than incremental encoders, as they can retain position data which makes them ideal for critical automation, robotics, and industrial control systems.
- Optical Encoders
Optical encoders use a light source rotating disk with transparent and opaque sections and a photodetector to generate signals. As the shaft rotates, the disk modulates the light beam, producing an electrical signal that represents motion.
These encoders offer high resolution and accuracy, which makes them ideal for precision applications such as automation, robotics, and motor control systems.
- Magnetic Encoders
Magnetic encoders use a rotating magnet and magnetic sensor to detect the changes in magnetic fields and convert them into position data. Unlike optical encoders, they do not rely on light, which makes them more robust in challenging conditions.
These encoders are highly resistant to dust, dirt and vibrations, which makes them ideal for harsh environments. Their durability ensures reliable performance in industrial, automotive, and outdoor applications where optical encoders may fail.
Working of Encoder
An encoder is a device used to convert motion into electrical signals to determine the position, speed, or direction of the rotor in various applications. The encoder detects the movement of an object and converts that movement into electrical signals.
The encoders typically consist of mechanical components that move with the object whose position is being monitored. As the component moves, it interacts with a sensing mechanism that detects the changes in position, speed and direction of the rotor.
This sensor generates an electrical signal based on the detected movement. The signal is then transmitted to the control system, which processes the information to determine the precise position or speed of the object.
Encoders may generate digital signals such as pulses or analog signals depending upon the type of encoder. These signals are used by the control system to track the movement and make adjustments as needed.
Applications of Encoder
Encoders are widely used across multiple industries. Some common applications include:
- Robotics
Encoders help robots determine joint angles, speed and positioning to enable precise movements and automation.
- CNC Machines
In CNC machines, encoders provide accurate position feedback to ensure precise machining.
- Automotive Industry
Encoders are used in vehicle speed sensors, throttle position sensors, and steering angle sensors to enhance vehicle control.
- Industrial Automation
Encoders are integral to conveyor systems, packaging machinery, and automated assembly lines for motion control.
- Medical Equipment
Medical devices such as MRI machines and robotic surgical systems use encoders for accurate positioning and control.
Factors for Selecting the Right Encoder
When selecting the right encoder for a system, several factors must be considered to ensure optimal performance and compatibility. Here are some key factors:
- Resolution
The encoder’s resolution determines the number of positions per revolution. A higher resolution provides finer control. Therefore, select the encoder based on the required precision for your application.
- Type of Output Signal
Encoders can produce analogue or digital signals. Digital signals, such as quadrature signals (A, B, and sometimes Z), are commonly used for precise position feedback, while analogue signals are better for applications requiring continuous data.
- Shaft Type
Encoders come with different types of shafts such as solid, hollow, or shaftless. Ensure the encoder shaft matches the system's mechanical interface and load capacity requirements.
- Interface Compatibility
The encoder’s output interface must be compatible with the system’s controller or other devices.
- Application Type
Different encoders suit different applications. Incremental encoders are suitable to provide rotational position feedback and absolute encoders are suitable to provide unique position value even after power loss.
Conclusion
Encoders are essential components in motion control applications, providing precise feedback for position, speed, and direction. Understanding the different types of encoders and their working principles helps in selecting the right encoder for specific applications. Whether in robotics, CNC machines, or industrial automation, encoders ensure efficiency and accuracy in modern technology.
By selecting the right encoder, industries can achieve better control, reliability, and performance in the systems. As technology advances, encoders will continue to evolve, offering even greater precision and versatility.