Open-Loop Control vs. Closed-Loop in BLDC Motors
Open loop control in BLDC motors is a method where the BLDC motor operates without feedback on its actual position or speed. Close-loop control in BLDC motors is a method in which the motor operates with real-time feedback on its position, speed, and torque. By understanding the workings and strengths, one can optimize BLDC motor performance.
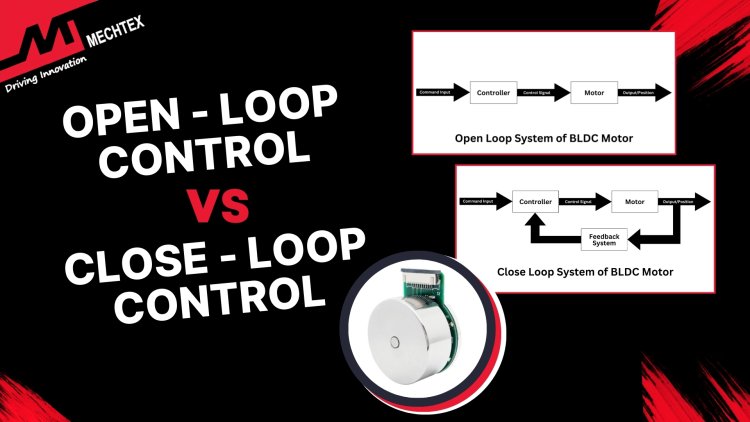
BLDC motors are widely used in industries due to their efficiency, reliability and precision. They offer superior performance over brushed DC motors which makes them ideal for applications like robotics, drones, electric vehicles, and industrial automation.
However, effectively controlling BLDC motors requires a robust control system. The two primary control methods are open-loop and closed-loop control. In this blog, we will explore the working principles, advantages, and applications of both methods, helping one to determine the right control strategy for the application.
BLDC Motor Control
BLDC motors are electronically commutated, unlike brushed DC motors that rely on mechanical brushes. Their control involves regulating speed, torque and direction using electronic controllers. The absence of brushes reduces friction, enhances efficiency, and prolongs motor life.
The BLDC motor relies on precise commutation, which involves switching current through stator windings to generate a rotating magnetic field. Hall effect sensors or sensorless methods detect the rotor position. Controllers use this data to synchronise with the rotor position, ensuring smooth operation.
Field-oriented control (FOC) and Sinusoidal Commutation techniques improve torque accuracy and reduce noise, while trapezoidal commutation offers simpler implementation.
Open-Loop Control
Open loop control in BLDC motors is a method where the BLDC motor operates without feedback on its actual position or speed.
In this method, the controller generates a sequence of electrical pulses based on a fixed commutation pattern. These pulses are applied to the stator winding and create a rotating magnetic field. The rotor is equipped with permanent magnets and aligns itself with the magnetic field and rotates accordingly.
The controller sends predefined signals to the motor windings, assuming the rotor will follow the expected motion regardless of the motor's actual position or speed. This approach simplifies the control system by eliminating the need for sensors or complex feedback mechanisms.
Close-Loop Control
Close-loop control in BLDC motors is a method in which the motor operates with real-time feedback on its position, speed, and torque.
In this method, the position or speed sensors detect the rotor’s actual position and send feedback to the controller. The controller compares this feedback with the desired reference value and makes real-time adjustments to the commutation signals.
This ensures that the BLDC motor maintains the speed and torque even under varying load conditions. This feedback mechanism enhances accuracy, stability, and efficiency, making it suitable for precision applications.
Key Differences Between Open-Loop and Closed-Loop Control
- Control Method
Open-loop control: It sends a fixed command to the BLDC motor without monitoring its actual performance.
Closed-loop control: It continuously measures the BLDC motor output, such as speed and torque and then adjusts the input to maintain accuracy.
- Control Accuracy
Open-loop control: It offers lower accuracy since it cannot correct deviations from the desired speed and position.
Closed-loop control: It ensures high accuracy by continuously correcting errors based on feedback.
- Complexity
Open-loop control: It is simple and easier to implement.
Closed-loop control: It is more complex in design as it requires sensors, feedback mechanisms, and other devices.
- Response Time
Open-loop control: It has a slower response due to load variations.
Closed-loop control: It responds faster and adapts to changes in load effectively.
- Applications
Open-loop control: It is suitable for basic applications such as fans, pumps, and simple motion systems.
Closed-loop control: It is ideal for robotics, CNC machines, and precision applications where stability and accuracy are critical.
Conclusion
Both open-loop and closed-loop control methods have their advantages and are suited for specific applications. Open-loop control is ideal for cost-effective, low-precision systems, while closed-loop control offers superior performance and efficiency in demanding environments. When selecting a control strategy for BLDC motors, consider the application’s accuracy, stability, and efficiency requirements.
By understanding the strengths and limitations of each method, one can optimize BLDC motor performance for various industrial and commercial applications.