Understanding Commutation in BLDC Motors
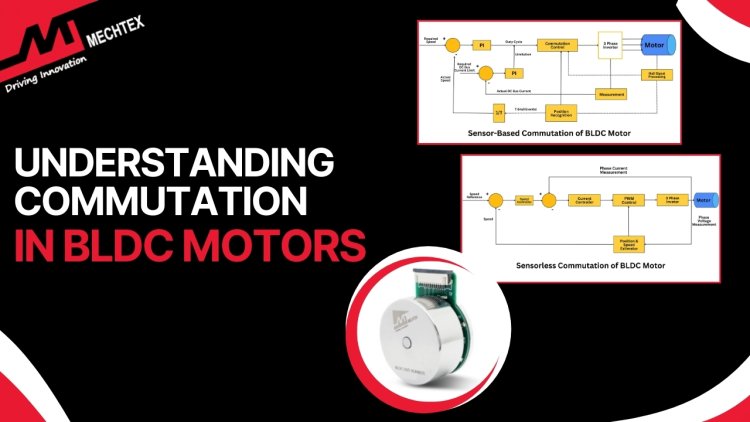
BLDC motors are widely used in industrial automation, robotics, EVs, and consumer electronics due to their high efficiency, reliability and low maintenance requirements. Unlike brushed DC motors, BLDC motors require electronic commutation to control the direction and speed of rotation.
In this article, we explore the fundamentals of commutation of BLDC motor, its type, and its impact on performance.
What is Commutation?
Commutation in a BLDC motor refers to switching current through the motor winding to maintain continuous rotation. Unlike brushed DC motors, which use mechanical brushes and commutators, BLDC motors use electronic commutation with semiconductor switches such as MOSFETs or IGBTs.
The commutation sequence is determined according to the rotor position, which is typically detected using hall sensors or sensorless techniques such as back-EMF. The controller energises the specific winding in a precise order and generates a rotating magnetic field that interacts with the rotor to produce motion.
Watch the YouTube Video by "Jantzen Lee" to understand how commutation helps BLDC Motors.
Efficient commutation ensures smooth operation, reduces torque ripple, and provides optimal performance. Poor commutation timing leads to increased losses, reduces efficiency, and causes overheating.
By precisely controlling the switching intervals, BLDC motors achieve high efficiency, reliability, and durability, making them ideal for applications in robotics, drones, electric vehicles, and industrial automation.
Types of Commutation in BLDC Motors
Commutation in a Brushless DC (BLDC) motor refers to the process of switching current through the motor windings. It is classified into two main types based on how the rotor position is detected and how the current is switched through the windings:
-
Sensor-Based Commutation
Sensor-based commutation in a BLDC motor relies on position sensors, typically hall sensors, to determine the rotor position and control the switching of current in stator windings accordingly.
Unlike sensorless control, which estimates rotor position through back-EMF, sensor-based commutation provides real-time feedback using hall sensors to ensure precise and reliable operation even at low speed.
The working principle of sensor-based commutation involves placing three hall sensors 120 degrees apart from the stator. As the rotor’s permanent magnet passes these sensors, they generate distinct signals that inform the BLDC motor controller about the rotor position.
The controller then sequentially energises the stator winding in a six-step commutation process to ensure continuous rotation.
This method eliminates the need for complex estimation algorithms and ensures smooth operation, making it ideal for applications requiring consistent torque delivery, such as robotics, industrial automation, and electric vehicles.
Advantages
-
-
- Accurate Position Detection: It enables precise communication and smooth operation.
- Reliable at Low Speeds: It works efficiently at low speeds to enable precise movements.
- Better Torque Control: Provides stable torque output without estimation errors.
-
Disadvantages
-
-
- Increased Cost: Additional sensors and wiring are required, which increase manufacturing expenses.
- Space Constraints: Not suitable for compact applications, as it requires additional space for sensor placement.
- Potential Sensor Failures: Sensors can degrade over time, requiring maintenance.
-
-
Sensorless Commutation
Sensorless commutation in BLDC motors eliminates the need for physical position sensors like hall effect sensors and relies on the back-EMF technique to determine rotor position.
Since the back-EMF is generated as the rotor moves through the stator magnetic field, it serves as a natural feedback signal for commutation, which allows precise switching of the stator windings without external sensors.
The working of sensorless commutation involves monitoring back-EMF in the unenergised phase of the BLDC motor. Since only two phases are actively energised at any time, the third phase remains open and allows back-EMF to be measured.
By analysing these signals, the controller accurately determines the rotor position and initiates the correct phase-switching sequence.
Advantages
-
-
- Reduced System Cost: It eliminates the need for hall sensors and wiring, which reduces the overall manufacturing cost.
- Improved Reliability: It eliminates sensor-related failures, which enhances its performance and makes it work well in harsh environments.
- High-Speed Efficiency: At high RPM, back-EMF control ensures smooth operation and enables efficient power conversion with minimal energy loss.
-
Disadvantages
-
-
- Poor Low-Speed Performance: At low speed, it is difficult for back-EMF to detect the rotor’s position, which affects the overall commutation process.
- Advanced Control Algorithms Needed: It requires additional algorithms such as Zero Crossing Detection (ZCD) or Extended Kalman Filters (EKF,) which increase computational requirements for the motor controller.
- Load Variability Challenges: Rapid load changes can disrupt back-EMF sensing accuracy.
-
Also Read
Sensorless Control Techniques for BLDC Motors
Importance of Commutation in BLDC Motor Performance
Commutation is a crucial factor in the performance of Brushless DC (BLDC) motors, as it governs the proper sequencing of current flow through the motor windings, ensuring smooth operation, efficiency, and torque generation. Key Aspects of Commutation in BLDC Motors are:
- Precise Control of Torque and Speed
Proper commutation ensures that the current flow aligns with the rotor position to optimise torque production. Any misalignment can cause torque ripple and create inefficiency, which affects the overall performance of the BLDC motor.
- Efficiency and Power Consumption
Efficient commutation minimises energy losses and reduces heat generation. Proper alignment enhances power utilisation and makes BLDC highly efficient.
- Smooth Operation and Reduced Noise
Well-timed commutation enables smooth phase transition, which reduces vibrations and noise. Poor commutation timing causes jerky motion and mechanical stress, which impact the BLDC motor’s efficiency, durability, and operational stability.
- High-Speed Capability
Electronic commutation enables BLDC motors to achieve more speed than brushed DC motors without mechanical wear. Speed is efficiently controlled by PWM or advanced techniques like Field-Oriented Control (FOC).
Conclusion
Commutation is a critical aspect of BLDC motor operation, dictating performance, efficiency, and reliability. While sensor-based commutation provides accurate rotor position feedback, sensorless methods offer cost-effective solutions for various applications. Understanding the fundamentals of commutation helps engineers design optimised BLDC motor control strategies tailored to specific industry needs.