Differences Between Spur Gear and Helical Gear
Spur gears and helical gears are two common types of gears used in mechanical systems. Both gears serve the same fundamental purpose, but they differ significantly in their tooth design, engagement characteristics, axial thrust and efficiency.
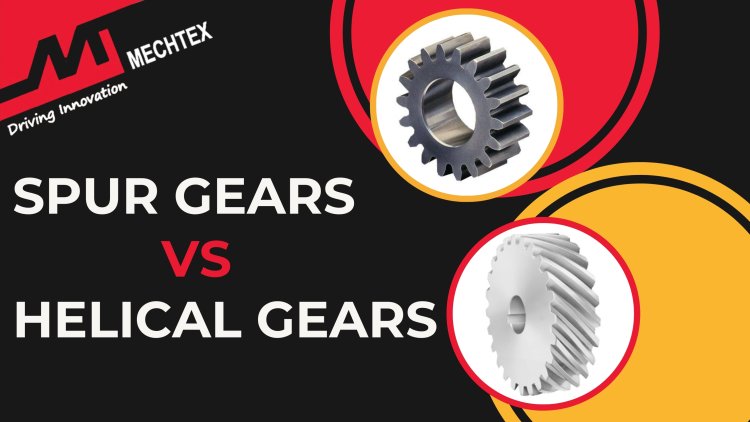
What is Spur Gear?
A spur gear is a fundamental component in mechanical systems widely used for transmitting motion and power between parallel shafts. It is the simplest and most common type of gear. It is characterised by straight teeth that are parallel to the axis of rotation. This straightforward design makes spur gear highly efficient and easy to manufacture.
Spur gear consists of several critical components such as gear teeth, pitch circle, and hub. Gear teeth are the primary component of spur gear. It engages with the teeth of another gear to transmit the motion and power. The pitch circle is the imaginary circle that defines where the teeth theoretically engage with another gear. Its diameter is known as pitch diameter. It is essential for calculating the gear ratios. The hub is the central part of the gear that attaches to the shaft and provides support and stability to the spur gear.
The working principle of spur gear involves the meshing of teeth between two gears. When the teeth of one gear push against the teeth of another gear, it causes the second gear to rotate. This meshing allows the transfer of rotational power and torque from one gear to another. The gears must be properly aligned and spaced to ensure smooth and efficient power transfer.
Spur gears are used in a wide variety of applications due to their simplicity and effectiveness. Common applications include clocks and watches, which are integral to precise timing mechanisms. They are also found in electric screwdrivers for simple gear reductions, washing machines to transfer power within the machine, conveyors for consistent movement and power transfer, and various types of industrial machinery.
Also Read
What is a Spur Gear? | Types, Benefits and Applications
What is Helical Gear?
Helical gears are a type of gear with teeth cut at an angle to the face of the gear forming a helix shape. This angled design allows for smoother and quieter operation as compared to spur gears. Helical gears distribute the load more evenly as multiple teeth are in contact at any given time. It reduces the stress on individual teeth and enhances their load-carrying capacity.
Spur gear consists of several components such as helical teeth, pitch cylinder, and helix angle. Helical teeth are teeth that cut an angle to the gear axis, providing gradual engagement and smooth and quiet operation. The pitch cylinder is an imaginary cylinder that represents the location where the teeth engage. It is similar to the pitch circle of spur gear. It is crucial for determining the gear ratio. The Helix angle is the angle at which gear teeth are inclined relative to the gear axis. Helix angle impacts the load capacity, and efficiency of gears during the operation.
The transmission motion of helical gear is characterised by smooth engagement. As the gear rotates, the teeth engage gradually along the tooth face, resulting in the smooth transition of forces. Unlike spur gears where teeth meet instantly along a single line, helical gears have rolling contact that starts at the one end of teeth and progresses to the other end. This smooth engagement reduces noise and stress over the gears. Additionally, continuous contact with multiple teeth allows for better load distribution and reduces gear slippage which leads to high power transmission.
Helical gears are used in a wide variety of applications such as automotive, industrial machinery, and aerospace due to their quiet operation and ability to handle load at high speed. They are also used in power plants for efficient energy transfer in turbines and generators and in marine propulsion to handle high torque.
Differences Between Spur Gear and Helical Gear
Spur gears and helical gears are two common types of gears used in mechanical systems. Both gears possess some differences over each other.
Here are some common differences between spur gear and helical gear
- Tooth Design
Spur gears feature straight teeth that are parallel to the axis of rotation while helical gears boast teeth that are angled diagonally. This angle tooth design in helical gears creates a gradual engagement between teeth and allows for smooth and quiet operation.
- Contact Pattern
Spur gears have a line of contact between the teeth that leads to higher impact forces and increased wear and tear. Helical gears exhibit a large contact area due to their angled teeth which results in distributing load over broader surfaces and resulting in low stress over the gears.
- Axial Thrust
Spur gears generate no axial thrust as their teeth are mesh along a single plane. However, helical gears due to their angled teeth, exert an axial force on the shaft. This axial thrust requires additional support mechanisms such as thrust bearings to prevent shaft movements.
- Efficiency
Helical gears owing to their smooth engagement and reduced friction, offer higher efficiency. This efficiency translates to less energy loss during power transmission. Spur gears also have high efficiency due to less friction between the teeth. However, the efficiency can decrease with increased speed and load due to the higher impact forces.
- Noise and Vibration
Due to the direct engagement of teeth, spur gears produce higher noise and vibration at high speeds. While helical gears produce low noise and vibration due to the gradual engagement of gears. This makes helical gears suitable for applications such as automobiles that require smooth and quiet operation.
Conclusion
Spur gears and helical gears offer distinct advantages and disadvantages. Spur gears are simple, less expensive to manufacture, and suitable for applications where noise and vibrations are not crucial. Conversely, helical gears provide smoother operation, higher efficiency and lower noise and vibration, making them ideal for quiet and smooth applications. The choice between these gear types ultimately depends on the specific application requirements and design considerations.