Sensorless Control Techniques for BLDC Motors
Sensorless control in BLDC motor is a technique which eliminates the need for physical sensors and relies on back-EMF to detect the rotor’s position. This technique improves the system's reliability and makes BLDC motors suitable for a wide array of applications.
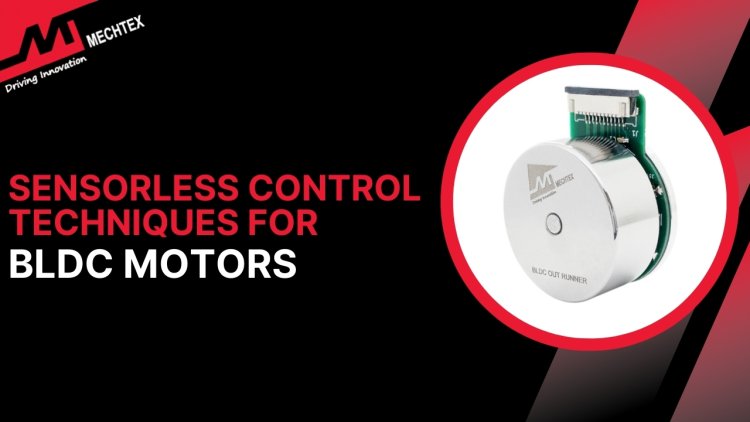
BLDC motors are widely used electric motors in various industries due to their efficiency, compactness, and reliability. Traditional BLDC motors rely on position feedback, typically from Hall sensors. However, modern BLDC motors use sensorless control techniques, which eliminate the need for physical sensors and enhance the motor’s durability. In this blog, we explore fundamentals, benefits, and various sensorless techniques to control BLDC motors.
What is BLDC Motor?
BLDC motor is a highly efficient and reliable DC motor widely used in modern applications. Unlike traditional DC motors which use brushes and commutators, BLDC motors use hall sensors for commutation. This design reduces wear and tear and increases the life span of the BLDC motor.
Construction of BLDC motors consists of stator, rotor and hall sensors. Stator is the stationary part of the BLDC motor and consists of windings. Rotor is the rotating part of the BLDC motor embedded with permanent magnets. Hall Effect sensors or sensorless algorithms, regulate the current to stator windings, generating a rotating magnetic field that drives the rotor.
Watch the YouTube Video by "JAES Company" about the working of BLDC Motors.
The working of BLDC motors is based on Lorentz force law. The electronic controller sends current pulses to stator windings in a specific sequence. This sequence creates a rotating electromagnetic field that interacts with the permanent agents embedded in the rotor. The rotor interacts with the magnetic field and produces smooth and precise motion.
Key advantages of BLDC motors include high efficiency, precise speed control, and high torque-to-weight ratio, making them ideal for applications like drones, robotics, automotive systems, and industrial automation.
Also Read
What is a BLDC Motor| Construction, Working and Applications
What is Sensorless Control Technique
Sensorless control in BLDC motor is a technique which eliminates the need for physical sensors such as hall effect sensors or encoders to detect the rotor’s position. Instead, it relies on back-EMF to infer rotor position and commutation timing. This technique improves the system's reliability and reduces maintenance costs by eliminating additional components.
The fundamental principle of the sensorless control technique is monitoring back-EMF induced in the unenergised phase of the BLDC motor. In a three-phase BLDC motor at any moment, two phases are active and one phase is inactive. By observing the back-EMF in the inactive phase, the BLDC motor controller can determine the zero crossing point, which signals the rotor position relative to the stator.
The controller then uses this information to adjust the switching of current into BLDC motor winding to ensure efficient and smooth operation.
The sensorless control technique is particularly effective in applications where compactness and low maintenance are crucial. Despite its complexity, modern electronics and advanced algorithms have made sensorless control a preferred choice in BLDC motors for industries such as automotive, aerospace, HVAC, and robotics.
Also Read
Back-EMF in BLDC Motors: A Complete Guide
Types of Sensorless Control Technique
Sensorless control techniques for BLDC motors eliminate the need for physical position sensors like hall sensors and rely on indirect methods to determine rotor position. Here are the key types of sensorless control techniques:
- Back-EMF Detection
Back-EMF detection is one of the most commonly used sensorless techniques for BLDC motors. It leverages the back-EMF voltage generated in the unenergised winding of the BLDC motor.
The zero crossing point of the back-EMF signal corresponds to the commutation points which are essential for smooth operation. It is a cost-effective method and relatively easy to implement. However, its performance at low speeds is limited due to the weak back-EMF generated at lower rotational speeds.
- Flux-Linkage Estimation
Flux-linkage estimation technique calculates the rotor position by integrating the difference between the terminal voltage and back-EMF. This method improves performance upon back-EMF detection by offering better performance at low speed.
However, this technique requires accurate BLDC motor parameters, such as resistance and inductance, to determine precise rotor position.
- High-Frequency Signal Injection
This technique involves injecting a high-frequency voltage signal into the BLDC motor winding and analysing the changes. These changes provide valuable information about the rotor position making this method particularly useful for low-speed and zero-speed applications.
- State Observer or Kalman Filter
The state observer including the Kalman filter method estimates rotor position and speed using mathematical models based on BLDC motor parameters.
Kalman filter enhances the robustness of the BLDC motor by minimising the impact of noise and estimate errors. Although, these methods demand advanced computation capabilities making them suitable for applications requiring high precision.
- Sliding Mode Observers (SMOs)
Sliding mode observers technique uses a non-linear control technique to estimate rotor position. They are highly robust against parameter variations and external disturbances making them suitable for demanding industrial applications.
Advantages of Sensorless Control Technique
Sensorless control techniques for BLDC motors offer several advantages, making them ideal for specific applications. These benefits include:
- Cost Reduction
By removing the physical sensors such as hall sensors or encoders, the sensorless control technique reduces the overall cost of the BLDC motor. This makes them an ideal choice for cost-sensitive applications such as consumer electronics, fans, and pumps.
- Compact Design
Without physical sensors, BLDC motor design becomes more simple and compact. This compact design is advantageous in applications where space is limited such as drones, power tools, and other compact industrial machinery.
- Enhanced Reliability
Sensorless system BLDC motor has fewer components which means few points for potential failures. It enhances the reliability of the BLDC motors especially in harsh conditions where sensors might be prone to damage from dust, vibration, or wear.
- High-Temperature Tolerance
Hall effect sensors or encoders can fail in high-temperature environments, limiting the performance of BLDC motors. The sensorless control technique eliminates this limitation and makes it suitable for applications that demand high-temperature operation, such as automotive systems and industrial equipment.
- Wide Speed Range
Sensorless control technique is highly effective across a broad range of speeds, from low to very high. This flexibility allows BLDC motors to perform efficiently in dynamic applications, such as drones or electric vehicles, where varying speed is crucial.
Conclusion
By integrating sensorless control techniques, BLDC motor manufacturers can achieve cost-effective, robust, and efficient motor systems suitable for a wide array of applications. These benefits make sensorless BLDC motors a preferred choice for industries prioritising reliability, compactness, and performance in challenging environments.