Understanding the Hall Effect Sensors in BLDC Motors
Hall Effect sensors play a crucial role in the operation of BLDC motors by providing real-time feedback on rotor position. They detect the rotor position and provide feedback to the controller to energise the correct winding of the stator to ensure smooth operation.
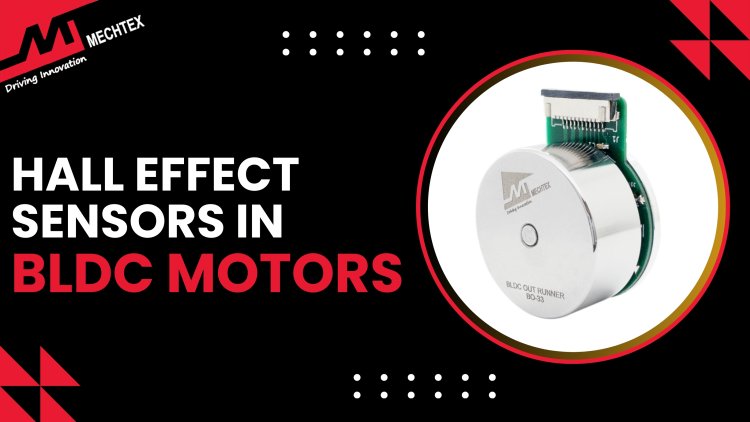
What is a BLDC Motor?
A BLDC motor is an electric motor that operates without brushes, which offers a significant advantage over brushed DC motors. Unlike brushed DC motors, where brushes are used to switch the direction of the current. BLDC motors rely on the electrical commutation method to switch the direction of current which eliminates the wear and tear caused by brushes and increases the lifespan of the motor.
The key difference between the brushed DC motor and the brushless DC motor lies in their structure. BLDC motors have permanent magnet rotors and stators equipped with electromagnets instead of brushes and commutators.
Watch the YouTube video by "JAES Company" for a better understanding of how BLDC Motors works.
The working principle of the BLDC motor involves the interaction between the magnetic fields of the rotor and stator. The controller switches the flow of current in the stator winding to create a rotating magnetic field which causes the rotor to spin. One of the key components of the BLDC motor is the Hall effect sensor. It detects the position of the rotor according to the magnetic field and ensures optimal performance, precise speed control, and smooth operation.
BLDC motors are widely used in applications where efficiency and precision are paramount, including electric vehicles, drones, robotics, and industrial automation systems, offering improved performance and reliability.
Also Read
What is a BLDC Motor| Construction, Working and Applications
What are the Hall Effect Sensors in BLDC Motor?
The hall effect sensor in a BLDC motor is a key component used to detect the rotor’s position. This information about the position is required to energise the phases of the motors during the operation to ensure efficient and smooth rotation.
Hall effect sensors of BLDC motors operate on the principle of the hall effect discovered by Edwin Hall in 1879. According to this principle, when a current-carrying conductor is placed in a magnetic field, a voltage is generated perpendicular to the direction of the current and magnetic field.
In BLDC motors, hall effect sensors are placed near the stator of the motor at specific angular intervals. In a three-phase BLDC motor, three hall sensors are placed 120 degrees apart. These sensors are positioned in such a way that they detect the rotor’s position and help the controller to energise the specific phases of the motor.
In BLDC motors, the rotor generates the magnetic field and moves. As the rotor moves, it alters the magnetic field around the hall sensor and enables it to detect the rotor position. After detecting the rotor position, hall sensors provide feedback to the controller to energise the correct winding of the stator at the right time.
Based on the hall sensors reading, the controller performs commutation to energise the phases of winding and create a magnetic field. With the help of commutation, the rotor aligns with the rotating magnetic field of the stator and ensures smooth operation. Without precise information from the Hall sensors, the BLDC motor would struggle to operate efficiently.
Advantages of Hall Effect Sensor in BLDC Motor
The hall effect sensor in the BLDC motor provides several key advantages that contribute to the efficiency, precision, and durability of the motor. Here are the main advantages of the hall effect sensor in BLDC motor:
- Accurate Positioning Feedback
The Hall effect sensor provides real-time and precise information about the rotor’s position. This information ensures proper energising of the motor’s winding and leads to smooth and efficient operation. Without accurate information about the rotor’s position, the BLDC motor may suffer and lead to inefficient performance.
- Reliable Commutation
In the BLDC motor, the commutation is based on the rotor’s position. The hall sensors replace the need for brushes and energise the windings of the stator in specific sequences to ensure smooth operation.
- Speed Control
The hall sensor provides continuous feedback about the rotor’s position and allows for precise speed control. The controller adjusts the voltage and current based on the rotor’s speed and enables fine control over the speed variation.
- Direction Sensing
The hall effect sensor detects the direction of the rotor’s movement. It is crucial for applications such as electrical vehicles and robotics that require directional movements.
- High Durability and Low Maintenance
Hall Effect sensors are solid-state devices with no moving parts, making them highly durable. They can operate reliably in harsh environments, including exposure to dust, moisture, and vibrations, common in industrial and automotive applications. They also eliminate the need for mechanical commutation (like brushes), the motor which leads to less maintenance, making it a cost-effective solution for long-term use.
Limitation of Hall Effect Sensor in BLDC Motor
While Hall effect sensors offer many advantages in BLDC motors, they also have several limitations that should be considered while using BLDC motors:
- Limited Accuracy at High Speed
At high speeds, the response time of the Hall effect sensor may not be fast enough to detect the rotor’s position. This can result in incorrect commutation and affect the motor’s performance.
- Temperature Sensitivity
Hall effect sensors can be affected by changes in temperature. Extreme heat may alter the sensor's output and affect its sensitivity which leads to inaccurate position detection.
- Magnetic Interference
Hall sensors operate on the basis of the magnetic field. However, they can be affected due to interference from external magnetic sources. This interference can cause incorrect readings or false commutation signals, potentially leading to motor malfunctions or inefficient operation.
- Additional Space Requirement
Hall Effect sensors require physical space within the motor, which can complicate the design of compact or space-constrained applications. The integration of sensors, wiring, and connections may add complexity to the motor design and assembly process.
Conclusion
Hall Effect sensors play a crucial role in the efficient operation of BLDC motors by providing real-time feedback on rotor position. This enables precise commutation, smoother startup, and better speed control. While there are some challenges with temperature sensitivity and cost, their advantages far outweigh the limitations in most applications.
Understanding the role of Hall Effect sensors is key to appreciating how BLDC motors deliver their outstanding performance across a wide range of industries. By leveraging these sensors, industries like robotics, electric vehicles, and automation benefit from the high efficiency and control that BLDC motors provide.