A Comprehensive Guide to Electronic Speed Controllers (ESC)
An ESC (Electronic Speed Controller) is an essential component to drive an electric motor. It regulates the speed, direction, and braking of the electric motor by adjusting the power supplied to the battery. They are used in drones, robotics, and industrial automation applications.
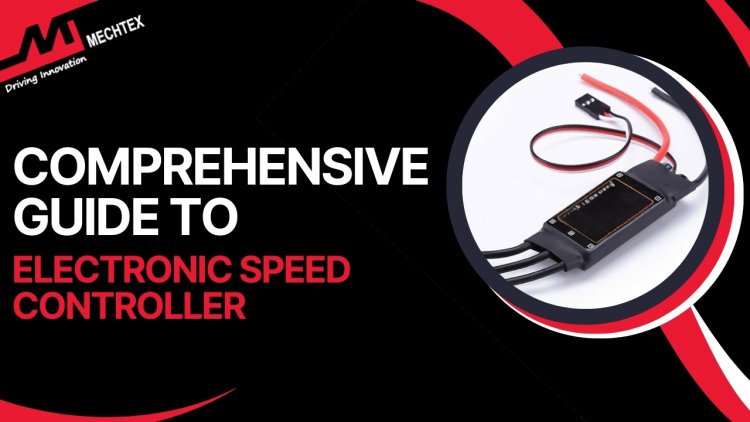
ESCs (Electronic speed controllers) play a crucial role in modern motor control systems, particularly in drones, RC vehicles, and industrial automation. They regulate motor speed, direction, and braking by processing signals from the controller, making them an essential component of brushless DC motors and brushed DC motors. In this blog, we will explore ESCs, their working principles, types, and applications.
What is an ESC (Electronic Speed Controller)?
An electronic speed controller (ESC) is an essential component in an electric motor-driven system, particularly in drones, electric vehicles, and industrial automation. It regulates the speed, direction, and braking of the brushless DC motor (BLDC) and brushed DC motor by adjusting the power supplied to the battery.
ESCs serve as an interface between the power source and the motor, ensuring smooth acceleration and deceleration while preventing voltage and current fluctuation that could damage the system. They typically receive signals from microcontrollers, remote receivers, or flight controllers and translate them into precise motor responses.
Watch the YouTube Video by "Painless360" to learn some basics about ESCs.
A key feature of ESCs is their ability to provide pulse-width modulation (PWM) control, which allows efficient and accurate motor speed adjustments. Additionally, modern ESCs include safety features such as overcurrent protection, thermal shutdown, and low-voltage cutoff to enhance reliability and longevity.
ESCs are available in different specifications based on voltage and current rating, making it crucial to choose the right one for the motor and application. The selection depends on factors like motor type, power requirements, and operating environment.
Working of ESC (Electronic Speed Controller)
An ESC (Electronic Speed Controller) is a crucial component in motor-driven applications. It regulates motor speed, direction and braking using Pulse-Width Modulation (PWM).
The ECS first processes the input signal received from a flight controller or remote receiver. This signal is typically in the form of PWM pulse ranging between 1000µs (0% throttle) and 2000µs (100% throttle). The ESC interprets the signal to determine the required speed and power output of the motor.
Once the signal is processed, the ESC converts the DC power supply from the battery into a three-phase AC output required for BLDC motors. This conversion is achieved through MOSFETs arranged in an H-Bridge or 3-phase bridge circuit, which rapidly switches the power supply to different motor winding ensuring smooth operation.
Advanced ESCs also feature braking and direction control. Some models include active braking (regenerative braking) to improve efficiency while reversing the phase sequence, which allows bidirectional motor control, making ESCs suitable for robotics and automated systems.
Types of ESCs (Electronic Speed Controllers)
ESC (Electronic Speed Controller) regulates the speed, direction and braking of electric motors, particularly in drones, RC vehicles, and industrial automation. ESCs are broadly classified based on control methodology and motor compatibility:
- Brushed ESCs
Brushed ESCs control conventional brushed DC motors. They work by varying the voltage supplied to the motor and adjusting speed using Pulse Width Modulation (PWM). These ESCs are simple, cost-effective, and easy to integrate but have lower efficiency and require frequent maintenance.
- Brushless ESCs (BLDC ESCs)
Designed for BLDC motors, Brushless ESCs use microcontrollers to switch power electronically between the motor phases. They are highly efficient, durable, and preferred in drones, robotics, and industrial automation. They are classified into two types:
-
-
- Sensored BLDC ESCs: Use the hall effect hall sensor to determine the rotor position ensuring smooth and precise control ideal for industrial applications and robotics.
-
-
-
- Sensorless BLDC ESCs: Estimate rotor position using back-EMF which reduces complexity and cost. These are common types of ESCs used in drones and RC models but may struggle at low speeds.
-
- Linear ESCs
Linear ESCs control motor speed by dissipating excess energy heat. They are inefficient and get overheated easily but are used in applications where electromagnetic interference (EMI) must be minimised.
- Switching ESCs
Switching ESCs use high-frequency PWM to regulate motor speed efficiently. They generate less heat and are widely used in drones, RC vehicles, and industrial applications.
How to Choose the Right ESC
Choosing the right Electronic Speed Controller (ESC) depends on several key factors, including motor type, voltage, current rating, and application. Here’s a step-by-step guide:
- Motor Compatibility
-
- Brushed Motors: They require simple ESCs with two output wires.
- Brushless Motors: They need more advanced ESCs with three output wires with sensor-based or sensorless control.
- KV Rating: Higher KV motors require high-frequency switching ESCs.
-
- Voltage Rating (V)
The ESC should match the voltage of the battery. For example, if you are using a 2S–6S LiPo battery, you need to choose an ESC that supports the respective voltage range.
It is important to ensure that the ESC can handle the highest voltage your system operates, to avoid any damage or performance issues.
- Current Rating (A)
Choosing an ESC with an appropriate current rating is crucial for safety and efficiency. The ESC should have a current rating that is at least 20% to 30% higher than the maximum current drawn by the motor.
- Features & Protocols
-
- BEC (Battery Eliminator Circuit): Powers the receiver and servos.
- DShot/PWM: Digital protocols like DShot offer more precision over traditional PWM.
- Active Braking (Regenerative Braking): Useful for drones and electric vehicles.
-
- Application-Specific Considerations
The specific application will influence the choice of the ESC. For drones, a lightweight ESC with a high refresh rate and Dshot support is essential for better control and efficiency. While in RC cars, an ESC supports reverse functionality for added manoeuvrability. Is required.
Conclusion
Electronic Speed Controllers (ESCs) are vital for efficient and precise motor control across various applications. Understanding their types, features, and selection criteria ensures optimal performance and longevity for your system. Whether in drones, robotics, or industrial automation, choosing the right ESC enhances control, stability, and efficiency.