Understanding Torque Speed Curves of BLDC Motors
The torque speed curve of the BLDC motor represents the relationship between the BLDC motor’s output torque and speed. It helps in selecting the right BLDC motor for the specific application.
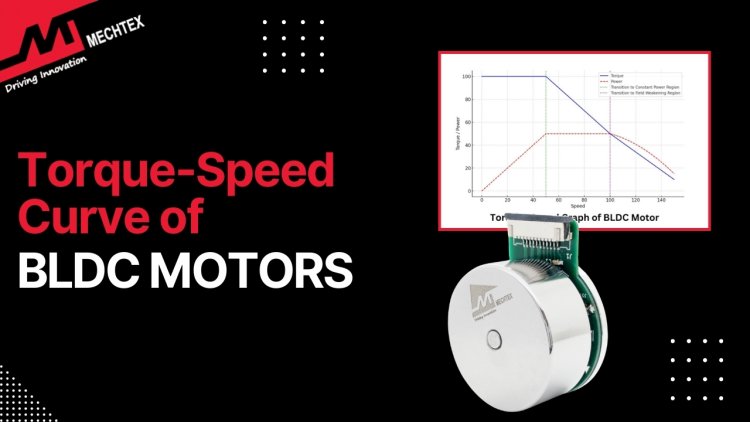
What is a BLDC Motor?
A BLDC motor is an electric motor that operates without brushes and uses electronic commutation instead of mechanical commutation. In a traditional brushed motor, brushes physically contact the commutator, and create friction and wear. A BLDC motor eliminates this issue by using a permanent magnet on the rotor and an electromagnet on the stator. This structure provides a long lifespan and increases the efficiency of the BLDC motor.
Construction of the BLDC motor includes two main components: stator and rotor. Stator is the stationary part of the BLDC motor and contains a series of windings. Rotor is the rotating part of the BLDC motor and consists of permanent magnets.
Watch the YouTube Video by "The Engineering Mindset" to know about the workings of BLDC Motors.
The working of the BLDC motor depends on the current supplied by the controller to the stator’s windings. A controller supplies the current to energise the stator winding and creates a rotating magnetic field. The rotor interacts with the rotating magnetic field and causes rotation. By adjusting the timing and power supplied to the windings of the stator, the controller modulates the speed and torque of the BLDC motor with high precision to achieve smooth operation.
BLDC motors come into two main configurations: Inrunner BLDC motor where the rotor is inside the stator and outrunner BLDC motor where the rotor is outside the stator. They are widely used in applications requiring precise control, like robotics, electric vehicles, and drones, due to their high efficiency, fast response, and low heat generation.
Also Read
What is a BLDC Motor| Construction, Working and Applications
What is Torque?
Torque refers to the rotational force generated by the motor to turn its shaft. In a BLDC motor (Brushless DC motor), torque is produced through the interaction between the rotating magnetic field of the stator and the magnetic field of the rotor.
Key Points to Consider
-
- Torque (T) is measured in Newton-meters (Nm)
-
- In BLDC motors, torque is directly proportional to the current supplied to its windings
-
- Torque produced in BLDC motor is smooth and continuous, especially in sinusoidal and FOC-controlled BLDC motors, which makes them ideal for applications like drones, robotics, and automation where precision is required.
Types of Torque in BLDC Motor
-
- Starting Torque: It is the initial torque required to overcome the inertia.
-
- Rated Torque: It is the continuous torque the motor provides without overheating.
-
- Peak Torque: It is the maximum torque that a BLDC motor can produce.
How to calculate the torque of a BLDC motor?
We can calculate the torque of the BLDC motor using the following formula:
Torque (T) = Kt × I
Where,
-
- T = Torque, measured in Newton-meters (Nm)
-
- Kt = Torque constant, measured in Nm/A or N·m per ampere
-
- I = Armature current, measured in Amperes (A)
Example
If a BLDC motor has - torque constant (Kt) = 0.05 Nm/A and its supplied current I = 6 A,
then,
Torque (T) = Kt x A
T = 0.05 x 6
T = 0.3 Nm
Therefore, torque of the BLDC motor is 0.3 Nm
What is Speed?
Speed refers to the rotational velocity of the motor, and it is measured in RPM (Revolutions per Minute). It indicates how fast the motor shaft is spinning.
In BLDC motors, speed depends upon the applied voltage, load conditions, and control method (open loop or closed loop). Since BLDC motors are electronically commutated and speed is regulated by adjusting the frequency and duty cycle with the help of a PWM signal (Pulse Width Modulation).
Key Points to Consider
-
- Speed (RPM) is increased with respect to the voltage applied to the motor
-
- A high KV rating of BLDC motor means high speed.
-
- Speed control is typically done by using an electronic speed controller (ESC)
-
- Speed is influenced by the load. More load slows the motor unless it compensates by current.
How to calculate the Speed (RPM) of BLDC Motor?
We can calculate the torque of the BLDC motor using the following formula:
RPM = KV x Voltage
Where,
-
- KV = RPM per volt (given in motor datasheet)
-
- Voltage = Supply Voltage (in volts)
-
- This formula gives no load speed, which means the motor is running without any mechanical load.
Example
If a BLDC motor has - KV rating of 1200 KV and is supplied with 11.1 V
then,
RPM = KV x Voltage
RPM = 1200 x 11.1
RPM = 13320
Therefore, RPM of the BLDC motor is 13320
What is the Relationship Between Torque and Speed?
In electric motors, torque and speed have an inverse relationship. As one increases, the other decreases simultaneously. This fundamental principle plays a pivotal role in determining motor performance across various applications.
Torque refers to the force produced by the motors shaft, and speed refers to how fast the motor will spin. The power output of the motor is the product of these two parameters (torque and speed). It means if the torque increases, then the speed must decrease proportionally and vice versa.
In BLDC motor, the torque speed curve clearly illustrates this inverse behaviour. At low speed, the BLDC motor produces high torque, which is essential for starting and lifting the load. As the speed increases, the torque gradually drops due to limitations in back-EMF and current handling capacity.
What is the Torque Speed Curve of BLDC Motor
The torque and speed curve of the BLDC motor represents the relationship between the motor’s output torque and speed. This curve is essential to understand how the BLDC motor performs under varying load conditions and speed. The torque and speed curve of the BLDC motor can be divided into three regions:
- Constant Torque Region
At low to moderate speed, the BLDC motor operates at constant torque. In this region, the BLDC motor can maintain a steady output torque as the speed increases. It is the region where the BLDC motor performs most efficiently.
- Constant Power Region
After reaching a certain speed, the BLDC motor enters the constant power region. After this point, the torque starts to decrease as the speed increases but power remains constant.
- Field Weakening Region
At a very high speed, the BLDC motor enters the field weakening region. At this point, the torque drops sharply as the speed increases and the BLDC motor is no longer able to produce enough torque to overcome load.
The curve is crucial for understanding the brushless DC motors motor efficiency, load handling, and optimal operating speeds. It helps in selecting the right motor for specific applications, ensuring the motor can deliver the necessary torque at the required speed while avoiding overloads or inefficient operation.
Factors Affecting the Torque-Speed Curve of BLDC Motor
The torque-speed curve of a BLDC (Brushless DC) motor is influenced by several factors that impact its performance. Key factors include:
- Supply Voltage
The supply voltage significantly impacts the BLDC motor’s speed and torque. The higher the voltage, the higher the brushless DC motor’s ability to achieve high speed and maintain torque. As the voltage increases the torque at higher speeds remains constant. Conversely, a decrease in supply voltage also decreases both speed and torque.
- Winding Resistance
The electrical resistance and inductance of the BLDC motor play an important role in determining the torque and speed relationship. Higher winding resistance leads to high power losses and reduces the torque. The inductance impacts how quickly the current can build and be supplied to the motor’s winding which influences the BLDC motor’s response at varying speeds.
- Using Back-EMF
Back-EMF is the voltage generated by the rotating motor which opposes the input voltage. As the BLDC motor’s speed increases, the back EMF also increases and opposes the applied voltage to the windings and limits the speed. The design of the motor, including the number of poles and magnetic properties, affects the back EMF characteristics.
- External Load
The external load connected to the BLDC motor directly impacts the torque and speed. A high load requires more torque to maintain a specific speed, which curves downwards. If the load exceeds the motor’s torque capacity at a given speed, the motor may slow down or stall.
- Controller Performance
The performance of controllers affects the torque and speed of the BLDC motor. Advanced controllers optimise the BLDC motor’s torque by adjusting the current and voltage in real-time. Controllers with poor performance can lead to a less efficient torque-speed curve, especially at higher speeds.
Also Read
Back-EMF in BLDC Motors: A Complete Guide
Conclusion
Understanding the torque-speed characteristics of BLDC motors is essential for engineers and designers aiming to match BLDC motor’s performance with application requirements. By analysing torque-speed curves, one can identify the most suitable BLDC motor and optimise system efficiency, reliability, and longevity.