Winding Configurations of a Stepper Motor
There are four primary types of stepper motor windings - unipolar, bipolar, star and delta winding configuration. Each winding type and configuration of a stepper motor play a pivotal role in determining stepper motor performance and suitability for specific applications.
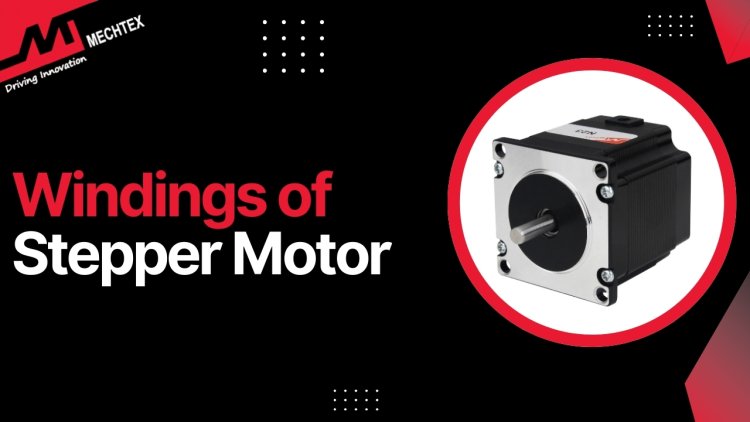
Stepper motors are versatile choices in applications requiring precise control of position and speed. The winding configuration in the stepper motor significantly influences its performance, efficiency and application.
In this blog, we dive into the types of stepper motor windings, their configurations, and how these factors affect their performance.
What is a Stepper Motor?
A Stepper motor is an electric motor that divides a full rotation into small, discrete steps. It provides precise control over position, speed, and acceleration without needing a feedback system, making stepper motors ideal for applications requiring high precision.
The construction of a stepper motor consists of two main components: stator and rotor. The stator is made up of electromagnets arranged in a circular pattern, while the rotor is made up of a permanent magnet or a soft magnetic core that sits inside the stator.
Watch the YouTube video by "The Engineering Mindset" to learn about stepper motors.
Working the stepper motor involves energising different coils in sequence to generate a magnetic field that interacts with the rotor. As coils are energised in precise order, the rotor moves in small defined steps.
Stepper motors are widely used in applications requiring precise motion control, such as 3D printers, CNC machines, robotics, and camera systems. They are also employed in automated manufacturing for tasks like positioning, controlling valve positions, and actuators.
Also Read
What is a Hybrid Stepper Motor?
Winding Configurations of Stepper Motor
There are four primary types of stepper motor windings: unipolar, bipolar, star and delta winding configuration. Each type has distinct characteristics suited for different applications.
- Unipolar Windings
Unipolar stepper motors have unipolar windings with a center tap and current flows in one direction through each half of the coil. These motors typically have 5, 6 or 8 wires. The center tap allows the stepper motor to operate with a simple driving circuit, as current flows in one direction at a time.
This configuration makes unipolar stepper motors easier to drive, as they have few components and less electronic control. This makes them ideal for applications where simplicity and ease of control are more important than maximum torque.
- Bipolar Windings
Bipolar stepper motors have coils without a center tap and current flows in both directions through each winding. These motors have 4 wires. To drive bipolar stepper motors, a complex driver circuit is required to reverse the direction of current through coils.
Bipolar stepper motors are known for their high torque as both halves of the coils are used for each phase resulting in more efficient use of the coil windings. They are ideal for applications that require higher performance and efficiency.
- Star Configuration
In this configuration, each stepper motor winding is connected at a common point for a “Y” shape. The common point is typically connected to a power supply and the ends of the windings are connected to a control circuitry.
This setup is common in small stepper motors for providing a balance of power and control.
- Delta Configuration
In the delta configuration, the windings are connected in a triangle shape. Each phase is connected to two other phases, forming a closed loop.
This configuration provides higher efficiency and more power output but is more complex to implement.
Impacts of Winding Types and Configurations on Performance
The choice of winding type and configuration impacts several performance parameters:
- Torque Output
Bipolar windings provide high torque due to full copper utilisation. This configuration influences torque ripple with five-phase motors offering smooth operation.
- Efficiency
Bipolar windings are more efficient, especially for applications requiring high torque. While unipolar windings are less efficient due to partial winding utilisation but are simple to control.
- Heat Generation
Heat dissipation is a concern in both winding types. A Stepper motor with bipolar winding may generate more heat due to higher current demand, necessitating effective cooling mechanisms.
- Cost and Complexity
Stepper motors with unipolar winding are cost-effective and easy to drive making them suitable for simpler applications. While bipolar winding stepper motors are more expensive but offer superior performance in demanding applications.
Factors for Choosing the Right Winding Configuration
When selecting a stepper motor winding and configuration, consider the following factors:
- Load Requirement
For high-torque applications, bipolar stepper motors are the go-to choice due to their ability to deliver high torque compared to unipolar stepper motors. Similarly, a five-phase phase-winding stepper motor provides smooth operation and makes it ideal for demanding tasks.
- Control Complexity
Unipolar stepper motors are easy to control because they require simple drive circuitry which makes them suitable for suitable low precision applications. On the other hand, bipolar stepper motors require more sophisticated drivers and control algorithms which offer enhanced precision and efficiency for applications that require high precision.
- Size Constraints
Compact applications require unipolar stepper motors which save space while maintaining adequate performance. For large applications, bipolar stepper motors are used for high torque and precision.
- Energy Efficiency
For applications that require power consumption, bipolar stepper motors are best as they operate with high efficiency, and convert more input power into torque. For applications where power consumption isn’t a concern, unipolar stepper motors offer simpler setups at the cost of reduced efficiency.
Conclusion
The winding type and configuration of a stepper motor play a pivotal role in determining its performance and suitability for specific applications. Unipolar winding excels in simplicity and cost-effectiveness, while bipolar and multi-phase winding provides higher torque, efficiency, and precision. By understanding the trade-offs and application requirements, one can select the optimal stepper motor for its needs, ensuring efficient and reliable performance.