How Spur Gearboxes Work?
Spur gearboxes are the simplest and most commonly used gear systems in mechanical power transmission. Its working principle involves the meshing of gear teeth, to transmit torque and alter the speed or direction of rotational motion between two shafts.
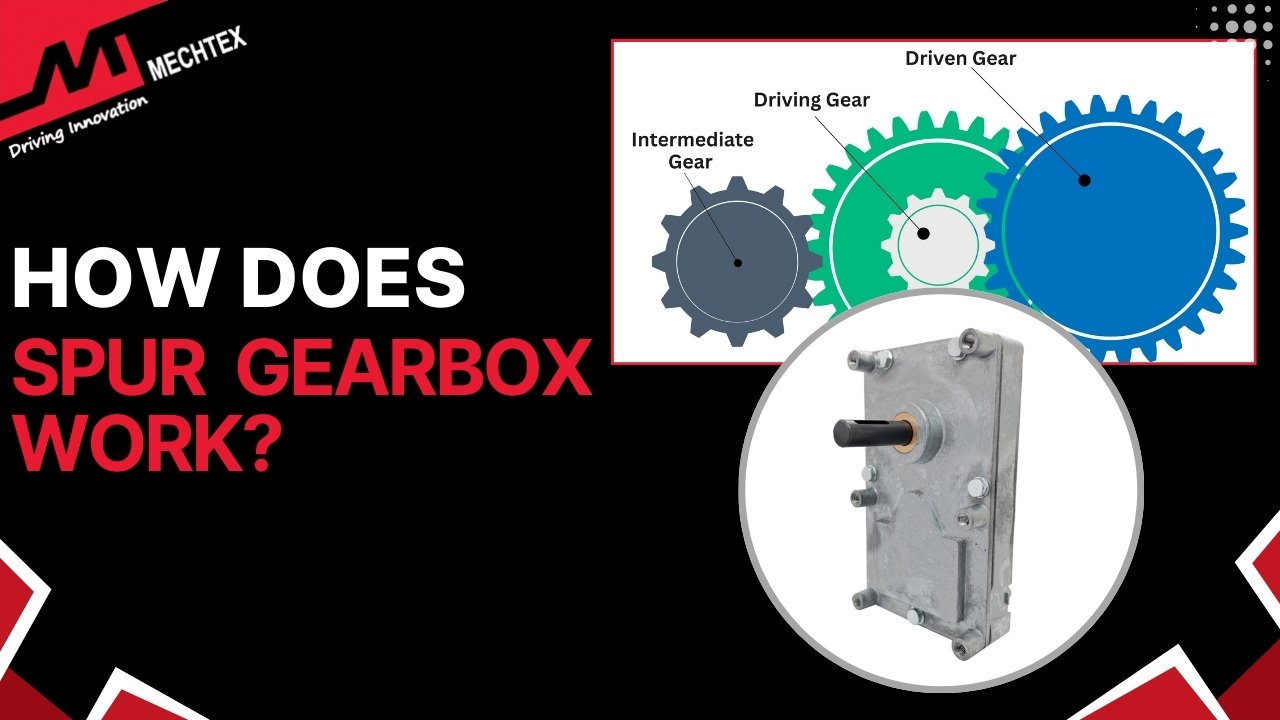
Spur gearboxes are one of the most fundamental and widely used mechanical power transmission systems. They are known for their efficiency and reliability and serve numerous industrial applications such as conveyor belts, packaging machines, automotive and robotic applications.
In this blog, we will explore the components, working principles, advantages and applications of spur gearboxes.
What is a Spur Gearbox?
A spur gearbox is a highly effective mechanical transmission system used to transfer torque and rotational motion between parallel shafts. It derives its name from the use of spur gears, i.e. cylindrical gears with straight parallel teeth that mesh directly to transmit power.
The primary components of spur gearboxes include a driving gear (input gear), a driven gear (output gear), and optional intermediate gears for achieving specific gear ratios. These gears are mounted on parallel shafts and are enclosed within a compact housing that supports proper alignment and lubrication.
Watch the YouTube Video by "ADTW Study" about Spur Gearboxes and its components.
Spur gearboxes are widely appreciated for their mechanical efficiency and their ability to deliver consistent power at high speeds.
One of the main advantages of spur gearboxes is their high torque transmission capability in a relatively compact form. Another advantage is their straightforward design, which allows for easy manufacturing, maintenance, and integration into various machines.
Spur gearboxes are commonly used in material-handling systems, packaging machinery, textile equipment, printing presses, and other industrial automation setups where high precision, low cost, and durability are required.
Working Principle of Spur Gearbox
Spur gearboxes are the simplest and most commonly used gear systems in mechanical power transmission. They operate using spur gears, which have straight teeth and are mounted on parallel shafts.
The primary function of the spur gearbox is to transmit torque and alter the speed or direction of rotational motion between two shafts.
The working principle of a spur gearbox involves the meshing of gear teeth. When the driving gear (input gear) rotates, its teeth engage with the teeth of the driven gear (output gear) and transfer motion and torque.
Because the gear teeth are straight and parallel to the shaft, power transmission is smooth and efficient, especially at moderate speeds.
Since the gear teeth mesh all at once along a straight line, spur gearboxes tend to produce more noise than other gearboxes.
Proper lubrication is also crucial for minimising friction, wear and tear, thereby ensuring long-term operation and making them suitable for many industrial applications.
Advantages of Spur Gearbox
Spur gearboxes are known for their simple design, high efficiency and reliability and offer several performance advantages across various applications. Some of the key advantages are:
- High Efficiency
Spur gearboxes can achieve high efficiency in power transmission. The direct engagement of teeth ensures minimal energy loss due to friction and makes them highly effective for conserving energy in industrial systems.
- Simple Design
The straightforward design of the spur gearbox makes it easy to manufacture and maintain. This simplicity also contributes to robust performance and consistent operation.
- High Load Capacity
Despite their simple design, spur gearboxes can transmit significant torque and handle heavy loads, which makes them suitable for various industrial applications.
- Cost-Effective
Due to standard production methods and the absence of complex shapes and alignments, spur gearboxes are more affordable than other gear systems.
Applications of Spur Gearbox
Spur gearboxes are widely used in various industries due to their simple design, high efficiency, and ability to handle high torque loads. Here are the key applications of spur gearboxes:
- Industrial Automation
Spur gearboxes are widely used in industrial automation for driving conveyor systems, packaging machines, and robotic arms. Their ability to maintain consistent torque and speed makes them ideal for precise and reliable motion control applications.
- Textile Machinery
In textile machinery, spur gearboxes drive looms, spinning machines, and knitting systems. They enable synchronised operation and contribute to the high precision of fabric production by ensuring uniform motion and torque distribution.
- Automotive Systems
Spur gearboxes are found in various automotive components, including manual transmission, differential drives and accessories such as wipers, seat adjusters, and electric windows. They offer compact and effective torque transfer solutions for smooth and efficient operation.
- Printing & Packaging Machines
In the printing and packaging industry, spur gearboxes enable accurate alignment and motion control in systems such as printing presses and labelling machines. This ensures high-speed operation with consistent output quality.
Conclusion
Spur gearboxes are essential components in mechanical power transmission. Their straightforward operation, high efficiency, and cost-effectiveness make them ideal for many industrial and commercial applications.
While they may not be suitable for high-speed or high-load scenarios, their reliability and simplicity continue to make them a preferred choice for engineers and machine designers worldwide.
Whether you're designing a conveyor system, building an automation project, or simply looking to understand how gear mechanisms function, spur gearboxes offer a perfect starting point in mechanical engineering.