Working Principle of DC Gear Motor
The Working Principle of the DC gear motor is based on the principle of electromagnetism and mechanical leverage. When direct current is supplied to the motor, it flows through the brushes and into the armature winding.
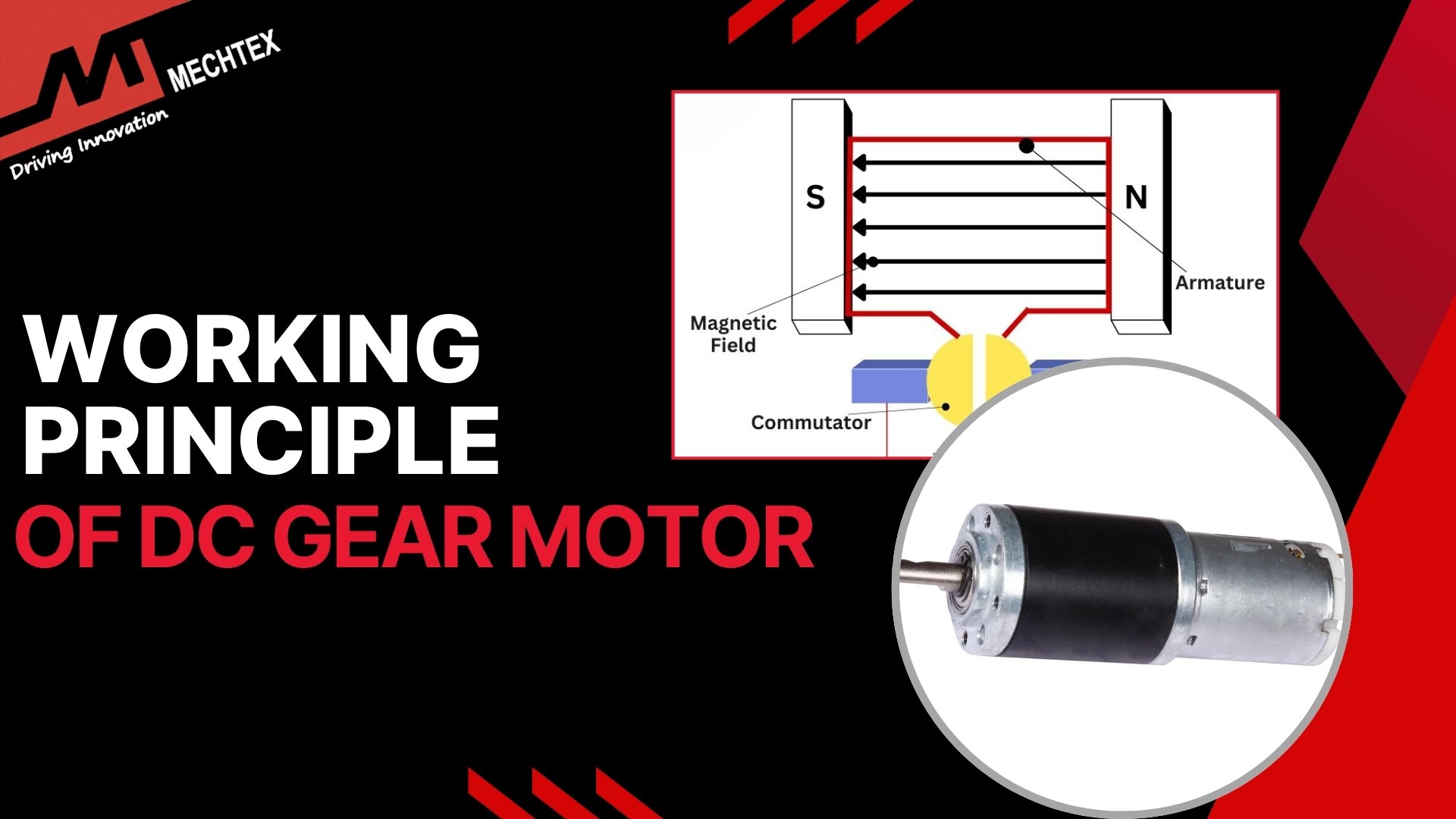
DC gear motors are widely used in robotics, automation, electric vehicles, and household appliances. Their compact size, high torque output, and energy efficiency make them the preferred choice for many motion control applications.
In this blog, we will explore the working principle of a DC gear motor, its components, types, and its advantages in real-world applications.
What is a DC Gear Motor?
A DC gear motor is an integrated electromechanical device that combines a DC motor with a gearbox to deliver high torque at low speeds. It converts electrical energy into rotational motion by reducing the speed and increasing the torque.
The construction of a DC gear motor consists of two main components: the DC motor and gearbox. The DC motor includes components such as stator, rotor, brushes and commutator. All these components work together to create motion.
The gearbox consists of a series of gears, such as spur, helical, or planetary. The role of the gearbox is to modify (reduce) the speed and torque of the DC motor. It also includes a gear train, an output shaft and a protective housing.
The key feature of DC gear motors is their ability to reduce speed and increase torque. Another key feature of DC gear motors is their ability to maintain consistent performance under varying load conditions. Depending upon design and application requirements, they also support features such as reversible rotation, speed regulation, and compact integration into limited spaces.
DC gear motors are commonly used in robotics, automation systems, conveyor belts, electric door locks, automotive actuators, and consumer electronics.
Also Read
Working Principle of DC Gear Motor
The operation of the DC gear motor is based on the principle of electromagnetism and mechanical leverage. When direct current is supplied to the motor, it flows through the brushes and into the armature winding.
As the current flows through the armature, it generates a magnetic field. This magnetic field interacts with the field produced by the stator’s permanent magnet or electromagnet. The interaction of these magnetic fields creates a force on conductors of the armature in accordance with the Lorentz Force Law.
To ensure continuous rotation in one direction, the motor uses a commutator. As the armature rotates, the commutator periodically reverses the direction of current in the winding.
However, a DC motor by itself typically generates high speeds with relatively low torque. But many real-world applications require the opposite—low speed and high torque.
To meet this requirement, a DC motor is coupled with the gearbox. The primary function of the gearbox is to reduce the speed of the motor. In this process of reducing speed, the torque is amplified.
The final output is delivered through the gearbox. The output is slower than but far more powerful than the original motor rotation, making it ideal for a wide range of applications such as industrial automation, robotics, and machinery where both power and precision are crucial.
Advantages of DC Gear Motors
DC gear motors offer a powerful combination of torque, efficiency, and compact design. Whether for robotics, industrial automation, or consumer electronics, these motors offer several performance benefits. Here are the key advantages of DC gear motors:
- High Torque at Low Speeds
As a DC gear motor combines a DC motor with a gearbox. It enables high torque output at low speed, ideal for applications that require precise movement.
- Compact and Space-Saving
The integration of the motor and gearbox makes it compact, which is perfect for space-constrained applications such as robotics, automation equipment, and medical devices.
- Precise Speed Control
DC gear motor allows for fine-tuned speed control through the PWM method, making it ideal for automated and variable-speed systems.
- Energy Efficient
Due to the torque multiplication, DC gear motors operate more efficiently at lower speeds, which conserves power and reduces heat generation.
Conclusion
DC gear motors are essential components in modern motion control systems. Their ability to deliver high torque at low speed in a compact, efficient, and cost-effective package makes them suitable for countless applications. By understanding the working principle of a DC gear motor, one can better leverage this technology to build smarter, more reliable systems.