Sinusoidal Commutation vs. Trapezoidal Commutation in BLDC Motors
Sinusoidal commutation uses smooth sinusoidal currents for quiet, precise motor control. Trapezoidal commutation energises BLDC motor windings in a six-step sequence, offering a simpler, widely used method for effective and efficient motion generation in BLDC motors.
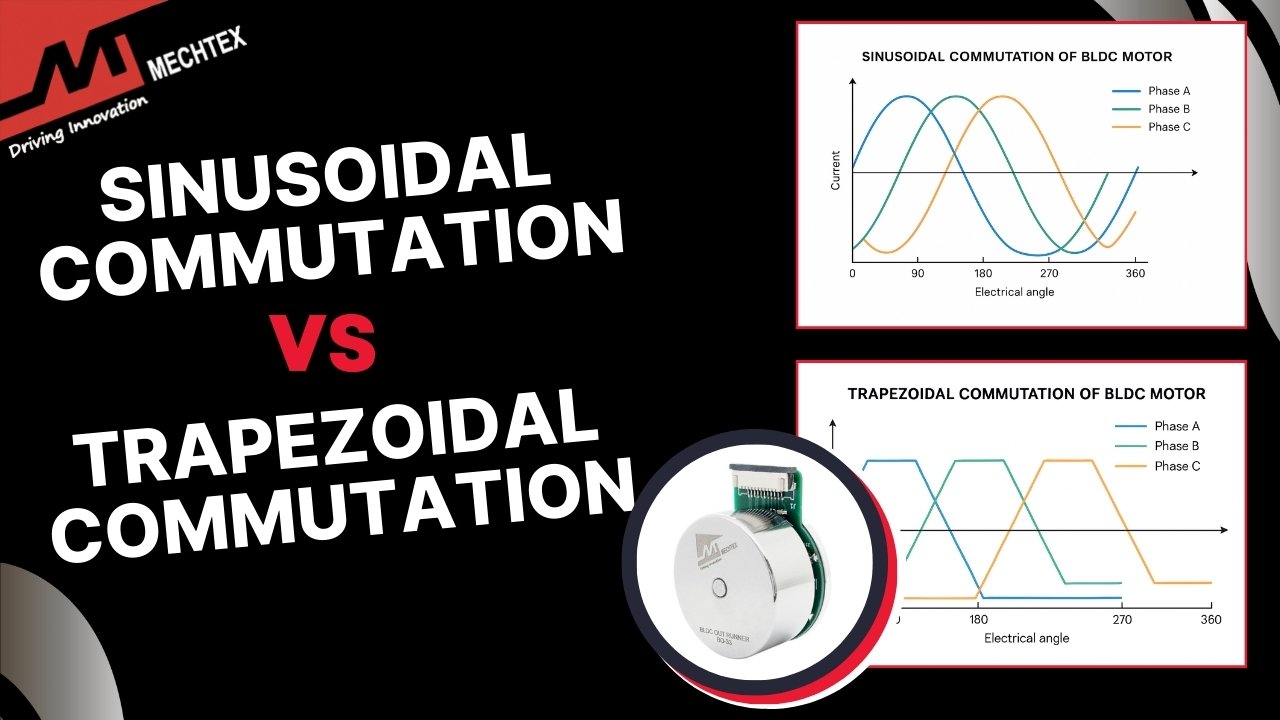
BLDC motors have gained immense popularity across various industries due to their efficiency, reliability and performance. A key aspect that determines how these motors function is the commutation method. This method is used to energise the motor winding for smooth operation.
In this blog, we will explore the different types of commutation methods used in BLDC motors, the key differences between the two methods, their working, and their applications.
What is Commutation in BLDC Motors?
Commutation refers to the process of switching the current in the motor windings to generate a rotating magnetic field (RMF) that drives the rotor. Unlike brushed DC motors, which use mechanical brushes and commutators, BLDC motors rely on electronic commutation, which is managed by an electronic speed controller (ESC).
The construction of BLDC motors includes rotor and stator with three-phase windings. To drive the rotor, the stator windings must be energised in a specific sequence that corresponds to the rotor’s position. This is where commutation plays a vital role. By sequentially energising the stator winding with commutation methods, it helps to drive the rotor smoothly.
Watch the YouTube Video by "MATLAB" to understand more about Commutation in BLDC Motors.
Commutation follows a six-step sequence, where only two of the three phases conduct current at any time. The ESC reads the rotor position either directly and switches the transistor into the inverter circuit accordingly.
Efficient commutation is essential for:
- Smooth operation
- Accurate speed and torque control
- Reduced electromagnetic interference (EMI)
- Maximising motor lifespan
Also Read
Understanding Commutation in BLDC Motors
What is Sinusoidal Commutation?
Sinusoidal commutation is a motor control technique used in BLDC motor systems where the stator windings are energised with smooth, sinusoidal current instead of abrupt signals. The goal is to produce a rotating magnetic field that smoothly interacts with the rotor’s magnetic field for precise and quieter operation.
Unlike trapezoidal commutation, which uses stepwise signals to energise the stator winding, sinusoidal commutation continuously modulates all three phases with sinusoidal waveforms that are 120° out of phase. It minimises torque ripple and electromagnetic noise.
Sinusoidal commutation operates by generating sinusoidal current waveforms in three-phase windings of BLDC motors. These waveforms are synchronised with the rotor’s position to ensure the magnetic field generated by the stator runs smoothly.
The real-time position of the rotor is detected by using sensors such as encoders or resolvers. A microcontroller or digital signal processor uses this feedback to determine the correct phase angle.
It then produces three sinusoidal reference signals, each shifted by 120°, which are converted into PWM signals to control the inverter transistors. The inverter then supplies modulated voltage to the motor windings, shaping the current to follow the sinusoidal pattern.
These continuous adjustments ensure that the magnetic interaction between the stator and rotor remains optimal for smooth and efficient torque production throughout the operation.
What is Trapezoidal Commutation?
Trapezoidal commutation is a widely used technique for controlling BLDC motors. It involves energising the three-phase windings of the BLDC motor in a six-step sequence to produce a rotating magnetic field that interacts with the rotor to generate motion.
In trapezoidal commutation, only two of three windings conduct current at any given time, while the third phase remains inactive. This switching occurs every 60°, completing a full electrical cycle in six steps. This creates a rotating magnetic field with discrete transitions.
The controller determines the rotor position either through a Hall effect sensor or a sensorless technique (using back-EMF detection). Based on the rotor position, it activates specific transistor pairs in the inverter to energise two motor phases with constant current, maintaining a 120° conduction interval.
The switching sequence is repeated continuously, keeping the magnetic field ahead of the rotor and producing torque. The current remains constant during each step, resulting in a trapezoidal waveform that matches the back-EMF profile.
Sinusoidal Commutation vs Trapezoidal Commutation
Sinusoidal and trapezoidal commutation are two key methods for BLDC motor control, differing in waveform, complexity, and performance—each suited to specific efficiency, precision, and cost requirements. Here are the key differences:
- Current Waveform
-
-
- Sinusoidal Commutation: Applies a smooth sinusoidal waveform to all three phases of motors to enable consistent torque production and minimal electromagnetic interference.
-
-
-
- Trapezoidal Commutation: Use a flat-top waveform to energise the BLDC motor windings in discrete steps, causing more abrupt torque and resulting in less smooth operation.
-
- Back-EMF Shape
-
-
- Sinusoidal Commutation: Works best with BLDC motors having sinusoidal back-EMF to match the input current shape of optimal torque performance.
-
-
-
- Trapezoidal Commutation: Suited for the BLDC motors designed with trapezoidal back-EMF to enable simple implementation.
-
- Phase Conduction
-
-
- Sinusoidal Commutation: Energise all three phases of the motor simultaneously with continuously modulated current to ensure better magnetic field alignment for smooth operation.
-
-
-
- Trapezoidal Commutation: Energises only two out of three phases at a fixed time to create a rotating magnetic field in discrete steps for every 60 electrical degrees.
-
- Control Complexity
-
-
- Sinusoidal Commutation: Requires advanced micro-controllers and real-time rotor position trackers, which demand complex software or algorithms to generate synchronised sinusoidal PWM signals.
-
-
-
- Trapezoidal Commutation: Easier to implement with basic control logic, which typically requires hall sensor feedback and less commutation effort for switching phase voltages.
-
- Efficiency
-
-
- Sinusoidal Commutation: Offers high efficiency, especially at low speeds, by maintaining optimal magnetic field alignment and reducing current spikes during operation.
-
-
-
- Trapezoidal Commutation: Provides low efficiency, particularly at high speeds. Current discontinuities also lead to a slight increase in losses.
-
- Applications
-
-
- Sinusoidal Commutation: Ideal for robotics, CNC systems, and medical equipment where smooth motion, accurate control, and minimal noise are essential for safe and high-precision operation.
-
-
-
- Trapezoidal Commutation: Commonly used in fans, pumps, blowers, and tools where simplicity, cost-effectiveness, and acceptable performance are more important than ultra-smooth motion control.
-
Conclusion
The choice between sinusoidal and trapezoidal commutation plays a crucial role in determining the overall behaviour of a BLDC motor system.
While trapezoidal commutation offers simplicity and cost benefits, it comes with compromises in smoothness and noise. On the other hand, sinusoidal commutation delivers precision and smooth operation but requires more complex and expensive control mechanisms.
As BLDC motors continue to power everything from home appliances to industrial robots, understanding these commutation techniques helps engineers and designers make the right choice for their specific needs.