Thermal Management in Synchronous Motors
Synchronous motors experience heat generation due to electrical and mechanical losses. By understanding heat generation sources and implementing cooling strategies like air or liquid cooling, heat sinks, and electronic thermal protection, industries can enhance synchronous motor performance while minimising downtime.
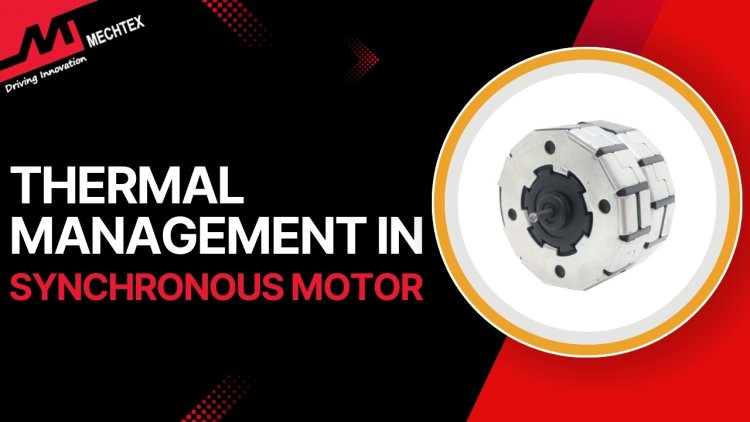
Synchronous motors are widely used in industrial applications due to their high efficiency, precision in speed control, and ability to maintain constant speed under varying load conditions. However, thermal management is important for the optimal performance and longevity of synchronous motors.
In this blog, we will explore the source of heat generation, the impact of thermal stress, and effective cooling techniques for synchronous motors.
Sources of Heat Generation in Synchronous Motors
Synchronous motors experience heat generation due to electrical and mechanical losses. Excessive heat generation can impact the efficiency, lifespan, and performance of a synchronous motor. The primary sources of heat generation in synchronous motors are:
- Copper (I²R) Losses
These losses occur in the stator and rotor winding of synchronous motors due to electrical resistance. The generation depends upon the square of current (I2) and resistance (R). In wound rotor synchronous motors, additional losses arise from rotor excitation currents.
- Iron (Core) Losses
Iron losses consist of:
-
-
- Hysteresis Losses: Repeated magnetization and demagnetization of the stator windings cause molecular friction and heat, which in turn result in hysteresis loss.
- Eddy Current Losses: These include circulating current in the stator core that generates heat which is proportional to the square of supply frequency.
-
- Friction and Windage Losses
These losses arise from bearing friction and air resistance (windage). These losses increase with rotor speed and air turbulence contributing to heat build-up.
- Stray Load Losses
This is an unpredictable loss resulting from harmonics, leakage flux, and slot effects generating minor but significant heat in synchronous motors. Proper cooling, efficient design, and quality materials help minimise these losses and ensure optimal synchronous motor performance.
Impacts of Excessive Heat on Synchronous Motor Performance
Synchronous motors are widely used in industrial applications due to their efficiency and precise speed control. However, excessive heat can significantly impact their performance leading to reduced efficiency, increased wear and motor failure. Some impacts of excessive heat on synchronous motors are as follows:
- Increased Copper Losses
It is one of the primary impacts of excessive heat on synchronous motors. High temperatures cause a rise in the resistance of stator and rotor winding and lead to I²R losses. This results in high power consumption and reduces the overall efficiency of the synchronous motor.
- Deterioration of Insulation
The insulation materials in synchronous motor winding degrade when exposed to high temperatures for a prolonged time.
This degradation increases the risk of short circuit and winding failures which not only reduces the synchronous motor’s lifespan but also leads to frequent maintenance and higher operational costs.
- Demagnetisation of Rotor Poles
Excessive heat also impacts the rotor, especially the motor with permanent magnet rotors. High temperature can lead to demagnetisation of the rotor which reduces the synchronous motor’s torque output and affects its overall performance.
- Bearing Damage and Lubrication Breakdown
Overheating negatively affects synchronous motor bearings by breaking down the lubricants. When lubricants are exposed to high temperatures, they lose their viscosity, which leads to increased friction and premature bearing wear.
This can cause mechanical failures, increased vibrations, and eventual motor breakdown.
- Reduced Torque and Performance Instability
Overheating affects the synchronous motor torque and potentially causes it to lose synchronisation. This is especially critical in applications where precise speed control is necessary for maintaining operational accuracy.
Effective Thermal Management Techniques for Synchronous Motor
Effective thermal management is crucial for ensuring the reliable operation and longevity of synchronous motors. Here are several techniques commonly used to manage the heat generated during their operation:
- Cooling Systems
-
- Air Cooling: The simplest form of cooling where fans or blowers are used to circulate air over the synchronous motor’s surface to dissipate heat.
- Liquid Cooling: It is a more effective method of cooling where coolants circulate through a jacket around the synchronous motor to absorb and carry away heat.
-
- Heat Sinks
These are the passive heat exchangers attached to the synchronous motor surface designed to increase surface area for heat dissipation. They help to lower the synchronous motor operating temperature, particularly in high load conditions.
- Insulation Materials
High-performance insulation materials can prevent excessive heat build-up inside the synchronous motor. These materials help to maintain a stable operating temperature and prevent thermal degradation of motor windings.
- Temperature Sensors and Monitoring
Synchronous motors often include temperature sensors within the winding or stator. These sensors feed real-time data to the controller which adjusts the motor's performance or activates cooling systems to prevent overheating.
- Motor Design Improvements:
-
- Improved Ventilation: Enhance the design of synchronous motor housing which allows for better airflow and prevents hot spots.
- Use of Low-Loss Materials: Employing materials that minimise core losses and friction reduces the overall heat generation in the synchronous motor.
-
Conclusion
Effective thermal management in synchronous motors is vital for maintaining efficiency, reliability, and longevity.
By understanding heat generation sources and implementing cooling strategies like air and liquid cooling, heat sinks, and electronic thermal protection, industries can enhance synchronous motor performance while minimising downtime.
Investing in advanced thermal management techniques ensures the durability and efficiency of synchronous motors in demanding applications.