Construction of DC Motor
A DC motor is an electrical motor that converts electrical energy into mechanical movement with the help of several components, including stator, rotor (armature), commutator, brushes, and windings.
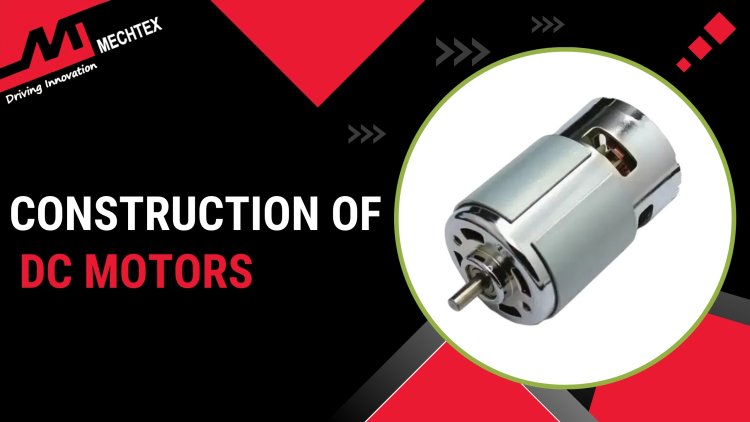
What is a DC Motor?
A DC motor is an electric motor that converts electrical energy into mechanical energy using direct current. Its working is based on the principle of Lorentz's law. As per this law, when a current-carrying conductor is placed within a magnetic field, it experiences a force. This force creates a motion which can be used for various tasks.
A DC motor consists of two main components: stator and rotor. The stator is the stationary part of the DC motor and creates a magnetic field. The rotor is the carrying conductor that rotates within the stator's magnetic field. Brushes and commutators are responsible for reversing the direction of the current to ensure continuous rotation.
There are two different types of DC motors: Brushed DC motors and Brushless DC motors. Brushed DC motors are the simplest and most common type of DC motor. It consists of brushes that are used to maintain electrical contact with the commutator and ensure rotation.
Brushless DC motors are a modern type of DC motor. They are also known as BLDC motors. In BLDC motors, commutation is done electronically using a controller, which leads to greater efficiency and low maintenance requirements.
DC motors offer excellent speed control. Their speed is proportional to the applied voltage, and torque to the current. Thus, by varying voltage and current, precise control over speed and torque can be achieved.
Another advantage of DC motors is their simple design and compact size, which allows them to integrate into a wide range of industrial applications. Furthermore, DC motors are highly efficient and highly responsive. They convert electrical energy into mechanical motion and quickly respond to changes in load, especially at low-speed operations.
DC motors are used in electric vehicles, industrial equipment like conveyors and cranes, and robotics due to their precise speed control and high torque. Additionally, DC motors play a key role in renewable energy systems, converting electrical energy into mechanical power in solar and wind applications.
Construction of DC Motor
A DC motor is an electrical motor that converts electrical energy into mechanical movements based on the principle of electromagnetic field. Its construction includes several components such as stator, rotor (armature), commutator, brushes, and windings. Understanding these components is essential to exploring the workings of DC motors. Here are the key components of a DC motor:
- Stator
It is the stationary part of the DC motor and is responsible for generating the magnetic field. It consists of two or more magnetic poles. These poles are made up of either permanent magnets (in miniature motors) or electromagnets (in large motors). The stator establishes the north and south poles, which interact with the rotor to produce torque.
The stator consists of field windings. These field windings are wound around the stator poles. When current flows through these windings, it creates a strong magnetic field which interacts with the rotor and creates movement. These field windings are connected in either series or parallel combinations with rotors to achieve different motor characteristics.
- Rotor
It is the moving part of the DC motor. It is also known as an armature. It consists of a cylindrical core made up of laminated steel. Different slots are made at the core of the rotor to accommodate the windings.
These windings are made up of copper wire and wound at the slots of the core of the rotor. When current flows through these windings, it creates a magnetic field around the rotor, interacts with the stator and creates a rotational movement.
- Commutator
The commutator is an important component of DC motors. It ensures continuous rotation of the motor by reversing the direction of current flows through armature (rotor) windings. It is a split-ring device connected to the windings of the armature and rotates along with it. It is made up of segmented copper rings, which allows the brushes to make contact.
Whenever the armature (rotor) crosses a magnetic pole, it reverses the direction of the current through the windings and maintains the torque of the motor. This reversal of the current keeps the force applied on the rotor in the same direction and ensures smooth rotation.
- Brushes
It is typically made up of copper or graphite and used to transfer the current from an external power source to the commutator. Brushes are mounted on the motor’s housing and make a sliding contact with the commutator. It maintains an electrical continuity between the stationary external power source and the rotating armature (rotor).
Due to the friction between the brushes and the commutator, brushes wear out over time and require frequent replacements. It also creates some noise and leads to power losses.
- Yoke
It is the outer frame or housing of the DC motor. It provides protection to the internal components of the DC motor. Many DC motors are made up of cast iron or steel to enhance their structure. It also serves as a path for the magnetic flux created by the field windings, which helps to direct the magnetic field within the motor.
- Bearing and Shaft
The rotor of the DC motor is mounted on the shaft and rotates with the bearing. This bearing reduces friction and ensures smooth rotation. The motor’s mechanical output is delivered through the shaft, which can be coupled with the gear or wheel depending upon the application.
- Inter-Pole
Inter-poles are small auxiliary poles placed between the large poles of a DC motor. These poles are designed to improve the commutation between the commutator and brushes by reducing the spark that occurs with brushes. It can be achieved by creating a local magnetic field that counteracts the voltage caused by the armature windings and enhances the motor’s efficiency.
Working of a DC Motor
A DC motor operates by converting electrical energy into mechanical motion. The stator generates a magnetic field, while the rotor (armature) carries the windings. When direct current is supplied to the rotor windings, it creates a magnetic field, interacts with the stator and causes rotation.
The key component of the DC motor is the commutator, which switches the direction of the current in rotor windings to ensure continuous rotation. Brushes make electrical contact with the commutator and generate torque, which is proportional to the current supplied.
Conclusion
DC motor is a versatile motor that converts direct current electrical energy into mechanical motion, making it indispensable across various industries. Its ability to provide efficient and precise control of speed and torque allows it to be utilised in numerous applications, from small electronic devices to large industrial systems.
Their efficiency, reliability, and ease of control also allow them to be integrated into a wide range of systems, helping to power the modern world. Understanding the basic construction of DC motors enables better design and integration in various technological fields.