Winding Configurations in Synchronous Motors
The stator is the stationary part of a synchronous motor and consists of windings that produce a rotating magnetic field (RMF) for movement. They are classified based on their arrangements and connections.
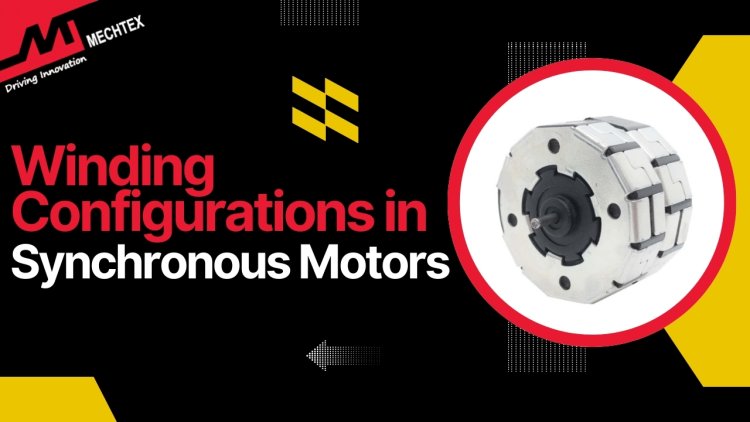
The winding configuration of the synchronous motor plays a pivotal role in its performance, efficiency, and suitability for different applications. Synchronous motors are extensively used in various industrial applications due to their ability to operate at constant speed and provide high torque under varying load conditions.
Understanding the different winding configurations of synchronous motors is essential to optimise their use in industrial and commercial settings.
Overview of Stator Winding of Synchronous Motor
The stator is the stationary part of a synchronous motor and consists of windings that produce a rotating magnetic field (RMF) for movement. This RMF interacts with the rotor and generates torque. The stator windings are made up of copper or aluminium conductors insulated to withstand high voltages and loads. The stator windings are classified based on their arrangements and connection. Different types of stator windings are:
- Single-layer vs. Double-layer windings
- Lap vs. Wave windings
- Distributed vs. Concentrated windings
- Star vs Delta Connection
Single-layer vs. Double-layer Windings
Single-layer Windings
In single-layer windings of synchronous motors, each slot of the stator core contains only one coil side. This winding configuration is simpler to design and manufacture, making it cost-effective for various applications.
Single-layer winding exhibits low manufacturing complexity and material usage. However, they may produce higher harmonic content than double-layer winding. This winding configuration is ideal for small synchronous motors with moderate performance requirements.
Advantages
- Simplified Manufacturing
- Low Cost
- Compact Design
Disadvantages
- Higher Harmonic Content
- Lower Performance
- Uneven Slot Utilization
Double-layer Windings
In the double-layer winding of the synchronous motor, each slot of the stator contains two side coils belonging to the different phases. This winding configuration reduces harmonic distortion and improves torque and power factor.
With better slot utilisation, double-layer winding allows a more compact design and efficient heat dissipation. This makes them ideal for applications requiring precision, reliability, and high efficiency.
Advantages
- Enhanced Performance
- Flexibility in Design
- Improved Cooling
Disadvantages
- Complex Manufacturing
- Higher Winding Resistance
- Increased Fault Risk
Lap Windings vs. Wave Windings
Lap Windings
In the lap-winding configuration of a synchronous motor, the coil ends are connected to adjacent commutator segments forming loops or laps. This winding configuration is suitable for low-voltage,high-current applications due to its ability to handle large current loads.
It also provides uniform current distribution and reliable performance making it ideal for high-speed applications.
Advantages
- High Current Capacity
- Uniform Current Distribution
- Easy Maintenance
Disadvantages
- Higher Resistance
- Limited for High Voltage
- Lower Efficiency
Wave Windings
The wave-winding configuration of the synchronous motor connects the coil ends to the commutator in a sequential pattern, spanning multiple slots before looping back, forming a wave-like structure. This winding configuration is ideal for high voltage, low current applications as it reduces winding resistance and improves efficiency.
Wave winding configuration is compact and provides better voltage regulation which makes them ideal configurations for high-speed synchronous motors.
Advantages
- High Efficiency
- Better Voltage Regulation
- Enhanced Electromagnetic Performance
Disadvantages
- Complex Manufacturing
- Less Current Capacity
- High Mechanical Stress
Distributed Windings vs. Concentrated Windings
Concentrated Windings
The concentrated winding configuration of the synchronous motor involves winding all the coils in a single slot and creating a compact design. This configuration simplifies manufacturing and reduces material usage which makes it cost-effective for low-voltage, high-current applications.
This configuration generates high harmonic distortion which leads to more torque ripple and reduces the efficiency of the synchronous motor.
Advantages
- Compact Design
- Lower Material Usage
- Suitable for Low-Voltage, High-Current Applications
Disadvantages
- Higher Harmonics
- Poor Voltage Regulation
- Increased Losses
Distributed Windings
The distributed winding configuration of the synchronous motor involves placing coil windings across multiple slots and spreading them evenly around the stator. This configuration reduces harmonic stress and increases synchronous motor’s efficiency to provide smooth and consistent torque.
Distributed winding configuration is ideal for medium to high-speed synchronous motors by offering better voltage regulation and reduced losses compared to concentrated windings.
Advantages
- Improved Voltage Regulation
- Smooth Torque Delivery
- Better Thermal Management
Disadvantages
- Increased Size
- Higher Initial Cost
- Maintenance Complexity
Star vs. Delta Connections
Star (Y) Connection
It is a three-phase winding connection where one end of each coil is linked to a common point, while other ends are connected to the supply lines.
This winding configuration reduces the voltage across each winding by a factor of √3 making it suitable for high-voltage applications.
Advantages
- Reduced Voltage per Winding
- Lower Starting Current
- Balanced Load
Disadvantages
- Lower Power Output
- Reduced Torque
Delta (Δ) Connection
It is a three-phase winding connection where each end is connected to each other in a loop and forms a triangle. This winding configuration allows the full-line voltage across each winding enabling higher torque and power output.
Delta connection is ideal for low-voltage, high-current applications and provides better fault tolerance.
Advantages
- Higher Torque and Power Output
- Better for Low Voltage Applications
Disadvantages
- Higher Starting Current
- Less Efficient for High Voltage Applications
Impact of Winding Configurations on the Performance of Synchronous Motor
Winding configurations significantly influence the performance of synchronous motors by affecting parameters like torque, efficiency, power factor, and thermal performance.
Below is an exploration of the impact of winding configuration on the performance of synchronous motors:
- Torque Characteristics
Double layer, distributed and wave winding configurations improve torque and enhance the overall performance of the synchronous motor.
- Harmonic Reduction
Distributed and double-layer winding configuration reduces harmonic stress and improves the efficiency of synchronous motors.
- Power Factor
Star winding connection enhances power factor at high voltage while delta winding connection provides better utilisation in voltage applications.
- Thermal Management
Advanced windings like distributed designs improve heat dissipation, extending motor life.
- Application Suitability
The choice of winding configuration and connection affects suitability for specific applications, such as low vs. high-power operations.
Conclusion
Stator winding configurations are a cornerstone of synchronous motor design, dictating their performance, efficiency, and suitability for various applications.
Understanding differences between the single-layer vs. double-layer, lap vs. wave, and distributed vs. concentrated windings enables engineers to make informed decisions.
With ongoing advancements in materials and manufacturing, the potential for optimising winding configurations continues to expand, paving the way for more efficient and versatile synchronous motors.