Dual Voltage Operation in Synchronous Motors
Dual voltage operation in a synchronous motor refers to the ability to operate at two different voltages while maintaining the performance. It is useful in an environment where the electrical supply of the system may vary. It is a powerful asset for modern industrial and commercial systems.
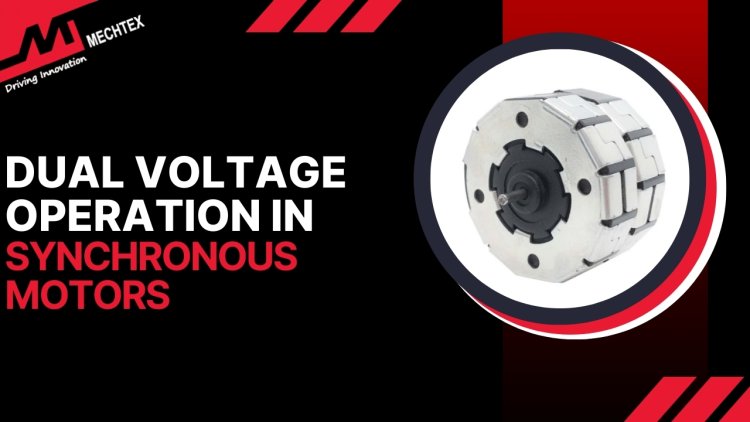
In industrial applications where voltage supply conditions vary or where motors need to be standardised across regions, dual voltage operation in synchronous motors plays a vital role. This operation enables the synchronous motor to operate at two different voltages - one on high and one on low- which offers flexibility, adaptability, and economic advantages.
In this blog, we will explore the fundamentals of dual-voltage operation, how it is implemented in synchronous motors, the internal winding connections, advantages and applications.
What is a Synchronous Motor?
A synchronous motor is an AC motor that operates at a constant speed irrespective of a change in load.
The construction of a synchronous motor consists of two main components: stator and rotor. Unlike induction motors, synchronous motors do not rely on rotor slip, the rotor rotates at synchronous speed with the stator’s magnetic field. This is achieved through either direct current excitation or permanent magnet rotors.
Watch the YouTube Video from "JAES Company" to understand the working of a synchronous motor.
The stator is typically a three-phase winding that generates a rotating magnetic field. When DC power is supplied to the rotor, it creates its own magnetic field, which locks with the stator’s magnetic field and ensures a constant speed under varying loads.
Synchronous motors are known for their high efficiency, power factor correction capability and constant speed operation, which makes them ideal for applications requiring precise and steady speed such as pumps, compressors, conveyors, and industrial machinery.
Also Read
What is a Synchronous Motor? | Construction, Working Principle and Applications
What is Dual Voltage Operation in a Synchronous Motor?
Dual voltage operation in a synchronous motor refers to the ability to operate at two different voltages - commonly on high voltage and low voltage levels while maintaining the performance. This feature is achieved by designing stator windings in a specific way that allows reconfigurations for either voltage, through star (Y) or delta (Δ) winding connections.
For example, A synchronous motor rated for 230V or 460V can operate at 230V in delta (Δ) winding connections and 460V in star (Y) winding connections.
This feature of synchronous motors is especially useful in an environment where the electrical supply of the system may vary. Instead of using different motors for different voltage levels, one dual-voltage synchronous motor can be used to improve the performance of the system.
Winding Configurations for Dual Voltage Operation in Synchronous Motors
In a dual-voltage synchronous motor, the stator windings are designed to allow it to operate at two different voltage levels by changing the connection design. The two most common winding configurations are:
Series-Parallel Connection (Six-Lead Motors):
In this winding configuration, each phase of winding is split into two equal halves. These halves can be connected either in series for high-voltage operation or in parallel for low-voltage operation.
- High Voltage: The two halves of each phase are connected in series to double the voltage across each phase but maintain the same current.
- Low Voltage: The halves are connected in parallel series to reduce the voltage requirement per winding while increasing the current capacity.
Star-Delta Connection (Nine-Lead Motors):
This configuration uses three sets of windings which can be connected in delta design for low-voltage or star design for high-voltage.
- Delta (Δ) Connection: Used for low-voltage operations, as each winding gets full voltage.
- Star (Y) Connection: Used for high voltage operation, as each winding receives only the phase voltage.
Terminal Markings and Wiring for Dual Operation in Synchronous Motors
A typical dual-voltage synchronous motor designed for industrial applications often features 12 terminals to allow flexible configuration for either high-voltage or low-voltage operation. These terminals correspond to a 3-phase, 2-winding per-phase configuration, enabling various wiring arrangements for voltage matching and load requirements.
The 12 terminals are generally categorised into three main groups:
- U1, V1, W1: This represents the start point of each of the three primary phase windings: Phase U, Phase V, and Phase W, respectively. These terminals typically connect to the incoming three-phase supply voltage.
- U2, V2, W2: These are the finishing points of the primary windings. Depending upon the voltage configuration, these terminals (U2, V2, W2) are either connected to each other or the auxiliary windings terminals.
- X1, X2, X3 and Y1, Y2, Y3: These are auxiliary or reconnectable windings ends that belong to the second set of winding in each phase. These additional windings are designed to enable reconnection between series (high voltage) or parallel (low voltage) configurations.
In a low-voltage configuration, each phase winding is split into two parallel paths (U1 to U2 and X1 to X2, for instance), which are energised simultaneously. This lowers the overall impedance and allows higher current flow at lower voltage. In this case, jumpers are used to connect:
- U2 to X1
- V2 to Y1
- W2 to Z1
In the high-voltage configuration, the two windings in each phase are connected in series. For example,
- U2 is connected to X1
- V2 to Y1
- W2 to Z1
Manufacturers such as Mechtex provide standard terminal board diagrams to simplify this process, showing jumper positions and terminal labels.
Advantages of Dual Voltage Operation in Synchronous Motors
Dual voltage operation in synchronous motors offers several practical and economic benefits, making them highly adaptable for various applications. Some key advantages are:
- Flexibility in Installation
Dual voltage synchronous motors can operate on two different voltages which allows them to be installed in facilities with varying power system standards. This flexibility simplifies procurement and installation across multiple locations.
- Ease of System Integration
Whether upgrading, replacing, or integrating equipment into new electrical systems, dual-voltage motors can be adapted easily to match the available supply voltage without altering the mechanical setup.
- Energy Efficiency at Higher Voltages
Operating a synchronous motor at a higher voltage typically reduces current draw, which minimises losses in stator winding and improves the overall performance of the synchronous motor.
- Improved Motor Lifecycle
The ability to operate at dual voltage configuration reduces thermal stress on insulation, leading to extended service life and improved reliability.
Applications of Dual Voltage Operation in Synchronous Motors
Dual voltage synchronous motors are widely used in industries that demand flexibility in power supply configurations, constant speed operation, and high efficiency. Their ability to operate at two different voltage levels makes them suitable for a variety of applications across different sectors. Key applications include:
- Pumps and Compressors
Used in water treatment plants, oil and gas facilities, and HVAC systems, as dual voltage synchronous motors allow adaption to regional voltage standards while maintaining precise speed and power output.
- Conveyors and Material Handling Systems
In automated warehouses or manufacturing lines, synchronous motors ensure constant speed of operation. Dual voltage capability enables use in different plants with varying supply voltages.
- Textile Machinery
In the textile machinery, machines are often relocated between facilities. Dual voltage motors allow seamless voltage compatibility without changing the motor or rewiring the system.
- Rolling Mills and Paper Machines
In heavy-duty processing industries, synchronous motors provide the precise speed needed. Dual voltage operation enables use in global facilities with different power standards.
Conclusion
Dual voltage operation in synchronous motors offers significant operational flexibility and cost benefits. By enabling motors to function under multiple supply voltages, industries gain the ability to standardize equipment, simplify logistics, and adapt to various power supply scenarios without redesigning their systems.
However, this flexibility comes with the responsibility of proper wiring, understanding the excitation system, and maintaining starting performance. With correct implementation, dual-voltage synchronous motors are powerful assets in modern industrial and commercial systems.