How Does a Planetary Gearbox Work?
The planetary gearbox is a compact and highly efficient mechanical transmission system that transfers torque and speed between the driving source and output load. It works on a unique gear system where multiple gears (planet gears) revolve around the central gear (sun gear).
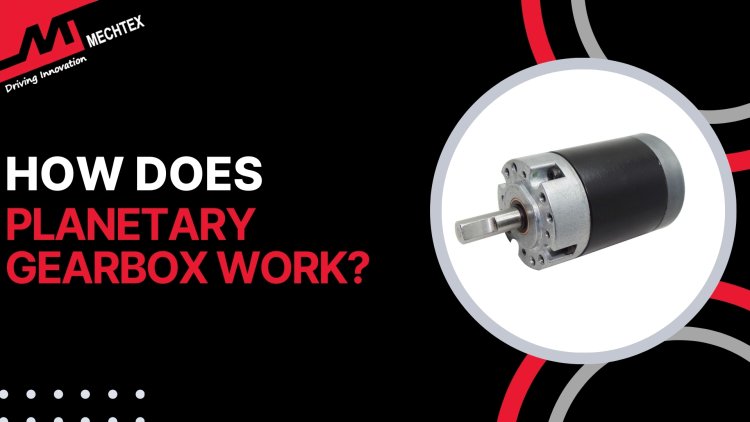
Planetary Gearboxes are essential components of modern mechanical systems where compact size, high torque and efficient power transmission are required. These gearboxes are used in a variety of applications, such as robotics, automation, automotive systems, and industrial machinery.
In this blog, we will explore the working principle, design, advantages and applications of planetary gearboxes in detail.
What is a Planetary Gearbox?
The planetary gearbox, also known as the epicyclic gearbox, is a compact and highly efficient mechanical transmission system that transfers torque and speed between the driving source and output load.
It is named after the arrangement of its internal gears, which resemble the motion of planets around the sun.
The components of the planetary gearbox include the sun gear, planet gear, planet carrier, and ring gear.
The Sun gear is the central gear. It is positioned at the centre and surrounded by multiple planet gears. Planet gears are the multiple gears that revolve around the sun gear. The ring gear is an outer ring with internal teeth that mesh with the planet gears. The carrier holds the planet gears and allows them to rotate around the sun gear.
Watch the YouTube Video by "Sabin Civil Engineering" to learn more about planetary gearboxes.
Planetary gearboxes are valued for high torque density, compact size, and load distribution. Since the load is shared across multiple planet gears, they can handle higher torque than other gear systems of similar size.
Planetary gearboxes are widely used in robotics, automotive transmissions, conveyor systems, and industrial automation. Their ability to provide precise torque control and high reduction ratios in a compact space makes them suitable for electric actuators and servo stabilizers.
Also Read
Planetary Gearbox | Introduction and Construction
Working Principle of a Planetary Gearbox
A planetary gearbox operates on a unique gear system where multiple gears (planet gears) revolve around the central gear (sun gear).
The working of the planetary gearbox begins with the sun gear. Sun gear is connected to the input shaft. When the sun gear rotates, it drives the surrounding planet gears. These planet gears not only rotate on their own axes but also revolve around the sun gear.
As they rotate, they engage with the internal teeth of the stationary or rotating ring gear to distribute the load across multiple contact points effectively. The multiple-gear arrangement allows the gearbox to handle higher torque than traditional gear systems.
Depending upon the configuration, different components of planetary gearboxes, such as sun gear, ring gear, or planet carrier, can be held stationary or used as input or output. This flexibility enables the planetary gearbox to deliver various gear ratios.
For example, when the sun gear acts as an input, the ring gear is fixed, and the planet carrier is the output. It results in high torque and low-speed output. Conversely, if the planet carrier is the input and the sun or ring gear is the output, it can generate high-speed, low-torque motion.
In conclusion, the planetary gearbox operates on the principle of distributing torque through multiple meshing gears within a compact structure. Its versatility in achieving different gear ratios, combined with its ability to handle high loads, makes it an essential component in various modern mechanical systems.
Advantages of Planetary Gearboxes
Planetary gearboxes have unique configurations of sun gear, planet gears and ring gears which offer several advantages and make them ideal for various applications such as industrial automation, robotics, and motion control applications. Some of the key advantages are:
- High Torque Density
The planetary gearbox can transmit high torque in a compact size. Multiple planet gears share the load, which allows for greater torque handling.
- Compact Design
Because of the co-axial design (input and output shafts are aligned), planetary gearboxes are more compact than traditional gear systems with small torque output.
- High Efficiency
Due to multiple gears and balanced load sharing, the planetary gearbox offers high efficiency in a single-stage configuration.
- Versatile Gear Ratios
Planetary gearboxes can be configured in various stages to achieve a wide range of gear ratios.
- Reduced Backlash
In precision applications such as robotics or automation, minimal backlash is essential. Planetary gearboxes are designed to maintain low backlash levels.
Applications of Planetary Gearbox
Planetary gearboxes are used in a wide range of industries due to their compact design, high torque output, and efficiency. Below are some key applications:
- Industrial Automation
Used in robotics, conveyor belts, pick and place systems and CNC machines for precise speed control and high torque in compact space.
- Electric Vehicles (EV)
Planetary gearboxes are ideal for EV powertrains, offering efficient torque transfer, compactness and reduced energy losses.
- Medical Equipment
Used in surgical robots, diagnostic machines, and mobility devices requiring silent, vibration-free, and reliable operation.
- Solar Trackers
Employed in a solar panel rotation system for reliable, high-torque motion under changing loads.
Conclusion
Planetary gearboxes are a marvel of engineering, delivering high torque, compact size, and versatility in performance.
Their unique configuration allows for balanced load distribution, efficient power transmission, and multiple gear ratio options. Whether used in robotics, industrial machinery, or electric vehicles, planetary gear systems continue to power innovation across sectors.