Open-Loop vs. Closed-Loop Control in BLDC Motor Drivers
Open-loop control is a fundamental technique used in BLDC motor drivers where the system operates without feedback. A closed-loop control technique in the BLDC driver ensures precision by continuously monitoring and adjusting the speed and torque of the BLDC motor based on real-time feedback.
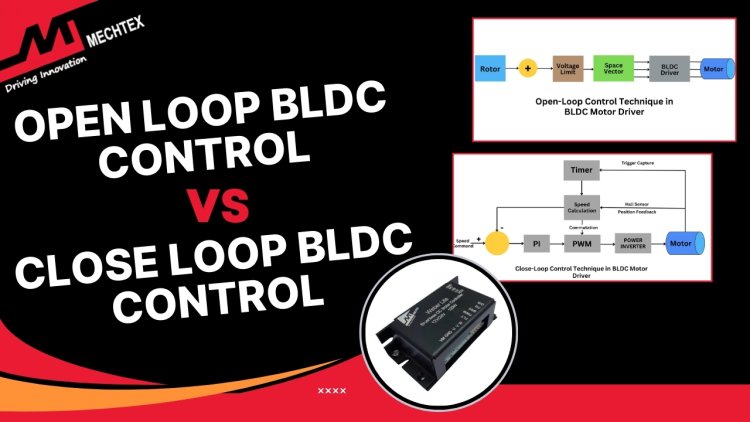
BLDC motors are widely used in industrial automation, electric vehicles, robotics and other applications due to their high efficiency, reliability, and precise control. The performance of the BLDC motor depends upon the type of control method used for its speed and torque. Two primary control techniques are: open-loop and closed-loop control techniques.
In this blog, we will explore the fundamentals of each technique and its differences, advantages, and applications.
What is a BLDC motor Driver?
A BLDC motor driver is an electronic circuit that controls the operation of a BLDC motor to ensure energy-efficient commutation for speed and torque regulation. Unlike brushed DC motors, BLDC motors (Brushless DC Motors) require external commutation using ESCs (Electronic Speed Controllers) or drivers. The driver ensures precise current switching in the motor windings for smooth and efficient operation.
The working principle of the BLDC motor driver involves converting DC power into three-phase AC signals. It energises the stator windings in sequence based on the rotor’s position. The driver also controls the voltage and current supplied to the BLDC motor using the PWM (Pulse Width Modulation) Technique. While advanced BLDC motors also use field-oriented control (FOC) to regulate the speed and torque of BLDC motors.
BLDC motor drivers offer several advantages, such as high efficiency, low maintenance, and precise control. They reduce energy losses due to the absence of brushes and increase the operational life of BLDC motors. Additionally, they allow for compact design with high power density, which makes them ideal for BLDC motors use in electric vehicles, drones, and industrial automation where precision is required.
Also Read
Understanding the Basics of BLDC Drivers
Open-Loop Control Technique in BLDC Motor Drivers
Open-loop control is a fundamental technique used in BLDC motor drivers where the system operates without feedback. In this technique, the controller sends predefined signals to the BLDC motor without monitoring its actual position and speed. The motor receives a sequence of electrical pulses based on a fixed algorithm and assumes that the motor will respond as expected under given conditions.
In an open-loop system, the BLDC motor driver supplies a sequence of voltage signals to the BLDC motor windings according to the fixed commutation pattern. This commutation is typically implemented using a microcontroller or motor driver that follows a predetermined timing scheme.
The switching of the stator windings is based on the estimated rotor position which is either assumed from the initial condition or calculated using open-loop estimation methods
Unlike the close-loop control technique, the open-loop control technique does not rely on position or speed sensors. Instead, it operates with a fixed-duty cycle and frequency of PWM (Pulse Width Modulation) technique to regulate the speed of the BLDC motor.
One key aspect of the BLDC motor driver's open-loop control technique is that it typically operates efficiently when the load conditions remain stable and predictable. However, any change in load or external conditions can lead to variations in actual speed and performance, as the system does not correct these changes.
Close-Loop Control Technique in BLDC Motor Drivers
A closed-loop control technique in the BLDC driver ensures precise speed and torque regulation by continuously monitoring and adjusting BLDC motor performance based on real-time feedback.
Unlike the open-loop control technique, which operates without feedback, the close-loop technique uses sensors to measure parameters such as speed, position, and current.
In the close-loop control technique, the feedback mechanism plays a crucial role in operation. Sensors such as hall-effect sensors or encoders provide real-time data about rotor position and speed. In the sensorless technique, back-EMF detection is used to monitor the position and speed of the rotor.
The control algorithms such as the PID controller process the measured speed and position of the rotor and compare it with reference input. Based on this comparison, the necessary adjustments are required to minimise error and maintain desired performance.
The controller then modifies the PWM (Pulse Width Modulation) signals sent to the inverter, adjusting the voltage and current supplied to the motor. This ensures smooth commutation and optimized motor operation.
Open-loop Control vs Closed-Loop Control
BLDC motor (Brushless DC Motor) can be driven using an open-loop or closed-loop control technique depending upon the application’s precision, efficiency, and other parameters. Here is a detailed breakdown of the key differences between both the techniques:
1. Feedback Mechanism
-
-
-
- Open-loop Control: Operates without a feedback mechanism. The controller sends a fixed voltage or PWM signal to the BLDC motor, without verifying its actual speed and position.
-
- Close-loop Control: Use feedback mechanisms such as hall sensors, encoders, or sensorless techniques to monitor the BLDC motor performance and adjust the signals accordingly.
-
-
2. Speed and Position Accuracy
-
-
-
- Open-loop Control: Lacks real-time data, which makes it prone to speed fluctuations, especially under varying load conditions.
-
- Close-loop Control: Ensures accurate speed and position control by adjusting the BLDC motor’s input signals as per the data from the controller.
-
-
3. Load Handling Capability
-
-
-
- Open-loop Control: Cannot compensate for external disturbance. A change in load condition affects the speed and torque of the BLDC motor.
-
- Close-loop Control: Actively adjusts to varying load conditions. A change in load cannot affect the speed and torque and provide a stable performance.
-
-
4. Efficiency and Power Consumption
-
-
-
- Open-loop Control: Less efficient as it operates at predefined parameters without optimising power usage.
-
- Close-loop Control: Adjust the power output based on the feedback received from the controller which improves the efficiency and reduces energy wastage.
-
-
5. Cost and Complexity
-
-
-
- Open-loop Control: This technique is simple to implement and cost-effective as it requires fewer components.
-
- Close-loop Control: More complex and expensive as it requires additional feedback sensors and control algorithms.
-
-
Conclusion
Both open-loop and closed-loop control strategies play essential roles in BLDC motor applications.
Open-loop control offers simplicity and cost-effectiveness but lacks precision and adaptability. A closed-loop control, on the other hand, provides enhanced accuracy, efficiency, and adaptability, making it suitable for advanced automation and dynamic applications.
Understanding their differences helps engineers and designers choose the best control method for their specific needs, ensuring optimal performance in BLDC motor-driven systems.