Incremental vs. Absolute Encoders: A Comprehensive Comparison
An incremental encoder is an electromechanical device which generates pulses relative to a reference point. An absolute encoder is a position-sensing device that provides a unique digital signal for each position to ensure precise motion tracking of the rotor. Each encoder has unique characteristics which make them suitable for various applications.
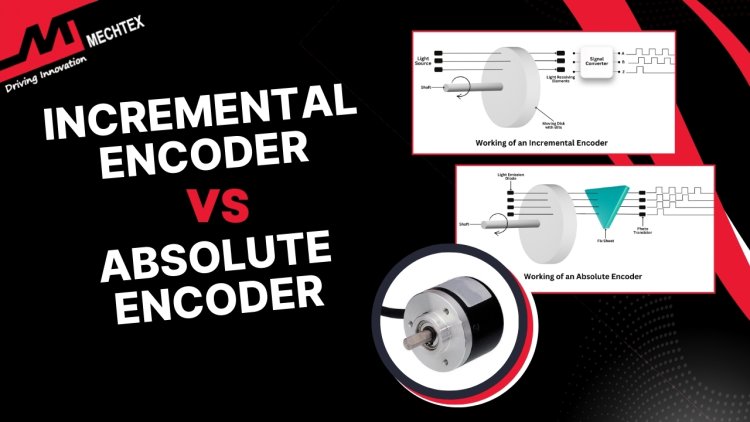
Encoders play a crucial role in motion control systems by providing position and speed feedback for motors, especially in robotics and automation applications. There are two types of encoders: incremental and absolute encoders.
Both the encoders serve the fundamental purpose of tracking rotational movement, but they differ significantly in functionality output signals and applications. In this article, we present a detailed comparison between incremental and absolute encoders, which helps us to understand their advantages, limitations, and best-use scenarios.
What is an Incremental Encoder?
An incremental encoder is an electromechanical device that converts rotational or linear motion into electrical signals to determine the speed direction and position of the rotor. Unlike other encoders, which provide a unique value for each position, incremental encoders generate pulses relative to a reference point.
The incremental encoder consists of a rotating disk with evenly spaced transparent and opaque sections. As the disk rotates, an optical or magnetic sensor detects these patterns, producing a series of pulses. This series of pulses is counted by the controller to determine the motion of the rotor.
It provides two key output signals, A and B, which are quadrature signals, which means they are 90° out of phase. It allows for direction-sensing in the following manner:
- If A leads B, the motion is in one direction
- If the B leads A, the motion is in the opposite direction.
A third signal, Z (Index Signal) is generated once per revolution to indicate a reference position.
Incremental encoders offer several advantages such as high resolution, accuracy and cost effectiveness. These encoders provide real-time feedback on speed and direction, which makes them useful in automation and motion control applications.
What is Absolute Encoder?
An absolute encoder is a position-sensing device that provides a unique digital signal for each position to ensure precise motion tracking of the rotor. Unlike other encoders, which only generate pulses relative to movement, absolute encoders retain position data even after power loss.
Absolute encoders use a rotating disk with multiple tracks, and each track represents a binary or gray code pattern. Optical magnetic sensors read these patterns, and the microcontroller interprets the data to determine the exact position. Since each position has a unique code, there is no need for an external counter or reference point.
Absolute encoders are available in single-turn and multi-turn variants. The single-turn encoder provides position data within one full rotation but resets after completing 360°. In contrast, multi-turn encoders track position across multiple rotations using an internal counter which makes them ideal for complex motion control applications.
Absolute encoders offer several advantages, such as precise position tracking without requiring homing and retention of position data even after power loss. and elimination of cumulative errors common in incremental encoders. However, they are more expensive and complex than incremental encoders and require higher processing power for data interpretation.
Absolute encoders are widely used in robotics, industrial automation, medical devices, aerospace, and CNC machines, where precise positioning is critical.
Key Differences Between Incremental Encoder & Absolute Encoder
Encoders are essential in motion control systems for providing feedback on position, speed and direction. There are two primary types of encoders: incremental encoders and absolute encoders.
Each encoder has unique characteristics which make them suitable for various applications. Here are some key differences between the two encoders:
- Signal Output
Incremental Encoders: Generate pulses as the shaft rotates. Each pulse represents a fixed movement and requires an external counter to track position.
Absolute Encoders: Provide a unique digital code for each position, which allows for direct positioning reading without external counting.
- Position Retention
Incremental Encoders: It loses position reference when the power goes off. A homing sequence is required upon restart.
Absolute Encoders: Retain position data even after power cut-off, which makes them ideal for critical motion applications.
- Resolution and Accuracy
Incremental Encoders: Resolution is defined by pulse per revolution (PPR). High PPR models offer better accuracy but need external counting.
Absolute Encoders: Offer high precision since each position has a unique digital code, which eliminates cumulative errors.
- Interface and Complexity
Incremental Encoders: Simple design, often using two channels (A and B) for quadrature output and optional Z pulse.
Absolute Encoders: Complex design, using parallel or series communication series, which increases difficulty in installation but offers great control.
- Application Suitability
Incremental Encoders: Best suitable for applications requiring relative movement tracking, such as conveyor systems.
Absolute Encoders: Suitable for applications that require precise positioning such as CNC machines, and robotics.
Conclusion
Both incremental and absolute encoders have their unique benefits and limitations. Understanding their differences allows engineers to select the most suitable option based on performance, accuracy, and budget considerations. Whether for industrial automation, robotics, or motion control, choosing the right encoder can enhance system efficiency and reliability.