Step Angle and Resolution in Stepper Motors: Facts Every Engineer Should Know
Step Angle is the angular displacement of the rotor from one step to another and is measured in degrees. While Stepper motor resolution refers to the smallest angular movement of the motor shaft. These parameters directly impact positioning accuracy, system smoothness, and control dynamics of the stepper motor.
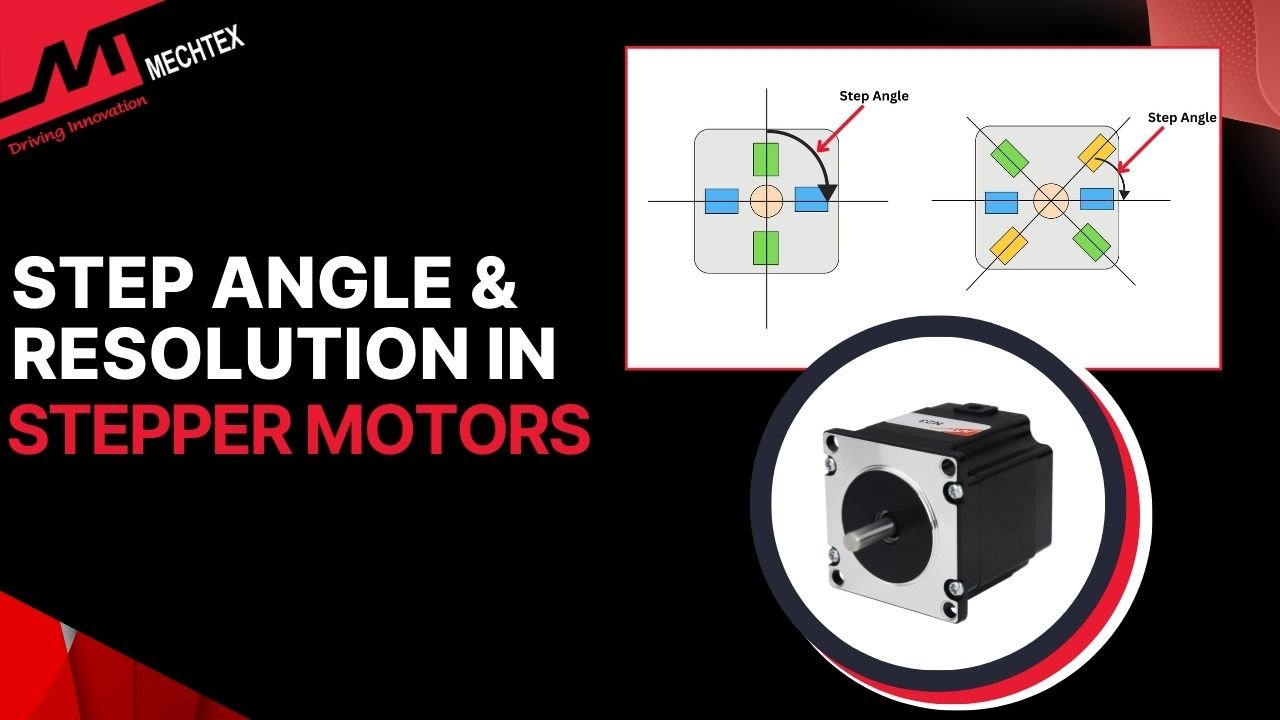
Stepper Motors are a popular choice in precision motion control applications such as 3D printers, CNC machines, medical devices and robotics. A critical component that defines the performance of a stepper motor in these applications is its step angle and resolution.
In this blog, we will explore what step angle and resolution mean, how they’re calculated, what affects them, and how they influence the performance of stepper motors. Whether you are an engineer who is looking to design a stepper motor, understanding step angle and resolution is essential to maximise its performance.
Overview of Stepper Motors
Stepper motors are electromechanical devices that convert electrical pulses into precise mechanical movements. They are known for their ability to move in fixed angular steps and are widely used in applications such as 3D printers, CNC machines, medical devices and robotics that require accurate positioning control.
The working of stepper motors is based on the electromagnetic principle. It consists of a rotor (made up of permanent magnets) and a stator that consists of multiple windings.
When electrical pulses are supplied to these windings in a specific sequence, they generate a magnetic field. These fields interact with the rotor and cause it to move in discrete steps. By adjusting the pulse frequency, one can control the stepper motor’s speed and allow for precise rotation without any feedback systems.
A critical parameter defining a stepper motor’s precise rotation is the step angle. It is the angle by which the rotor moves with each pulse. Typical step angles range from 0.9° to 7.5°, with smaller angles indicating higher precision.
Another factor which closely linked to the precise movement of the stepper motor is its resolution. It represents the number of steps the stepper motor takes to complete a full rotation.
In summary, stepper motors offer controlled movement through defined step angles and resolutions, enabling high-precision positioning without feedback systems, making them a reliable choice for open-loop control systems.
What is Step Angle?
The step angle is a fundamental parameter in stepper motors, which defines how much the motor shaft rotates with each input pulse to its windings.
It represents the angular displacement of the rotor for one step and is measured in degrees. It also determines the resolution and precision of the motor for fine control over positioning.
The formula to calculate the Step Angle is:
Step Angle (θ) = 360° / (Number of Phases × Number of Rotor Teeth)
The above formula explains that the step angle depends on the internal design, such as the number of stator phases and the number of rotor teeth (or poles).
For Example,
If a stepper motor has 2 phases and 50 rotor teeth, then the step angle of the stepper motor will be,
Step Angle (θ) = 360° / (Number of Phases × Number of Rotor Teeth)
Step Angle (θ) = 360°/ (2x50)
Step Angle (θ) = 3.6°
The Step Angle of the stepper motor will be 3.6°
The common step angles for stepper motors are 1.8° (most common in hybrid stepper motor), 0.9° (Used where finer resolution is needed). and 7.5° or 15° (Found in simple permanent magnet (PM) stepper motors.)
Importance of Step Angle in Stepper Motor
- Precision
Small step angles offer high precision. E.g., a stepper motor with 1.8° step angle moves 200 steps for one revolution (360°), to provide fine control.
- Resolution
It is inversely proportional to the step angle of the motor and offers better resolution.
What is Stepper Motor Resolution?
Stepper motor resolution refers to the smallest angular movement of the motor shaft and is determined by the number of steps it takes to complete one full 360° rotation.
It is expressed in steps per revolution (SPR) or degrees per step. The higher the number of steps per revolution, results in finer the resolution and precise the movement.
The stepper motor resolution can be calculated using the following formula:
Resolution (degrees per step) = 360° / Number of Steps per Revolution
For Example,
If a stepper motor has 200 steps per revolution,
Resolution (degrees per step) = 360° / Number of Steps per Revolution
Resolution = 360° / 200
Resolution = 1.8° per step
Stepper motor resolution is crucial for applications that require precise positioning, such as 3D printers, CNC machines and robotics. Higher resolution results in smooth motion and accurate control without any feedback system.
Importance of Step Angle and Resolution in Engineering Applications
Step angle and resolution are two critical parameters in a stepper motor, which significantly influence the performance of the stepper motor in applications requiring precise control.
Understanding its importance is essential for selecting the right stepper motor for automation, robotics, and instrumentation tasks.
- Precision and Accuracy
-
- Smaller step angles, such as 0.9° or 1.8°, make fine movement of the stepper motor and result in higher resolution.
-
- It allows for accurate positioning without any feedback system and makes them ideal for applications such as CNC machines, 3D printers, and laser cutters.
-
- Repeatability
-
- High resolution ensures that the stepper motor returns to the exact position each time, when it receives the same number of pulses.
-
-
-
- It makes stepper motors reliable for automated testing equipment and pick-and-place machines where consistent movement is essential.
-
- Speed vs Precision Trade-off
-
- A stepper motor with small step angles offers better precision but provides low speed.
-
-
-
- In contrast, a stepper motor with large step angles is suitable for applications where speed is important than precision.
-
- Ease of Control
-
-
- With step angles and resolution, engineers can design a simple open-loop system by using pulse signals for precise positioning.
-
-
-
- It is suitable for applications like camera gimbals, antenna positioners, and syringe pumps, where precise positioning is essential.
-
- Cost-Effectiveness
-
- High-resolution stepper motors eliminate the need for external encoders or sensors in many positioning systems.
-
-
-
- This reduces system complexity and cost, making them ideal for budget-sensitive engineering designs.
-
Conclusion
Understanding step angle and resolution is essential when working with stepper motors. These parameters directly impact positioning accuracy, system smoothness, and control dynamics.
Engineers must carefully analyse application needs to select appropriate motor specifications. While higher resolution offers better accuracy, it comes at the cost of complexity and potential torque limitations.
By balancing step angle, resolution, and control strategy (like microstepping), engineers can unlock the full potential of stepper motors in precision motion systems.