How ESCs Work: The Basics of Motor Control
An electronic speed controller (ESC) is a crucial device that controls the speed, direction, and braking of an electric motor. Its operation is rooted in power electronics and digital signal processing to enable precise motor control with real-time responsiveness.
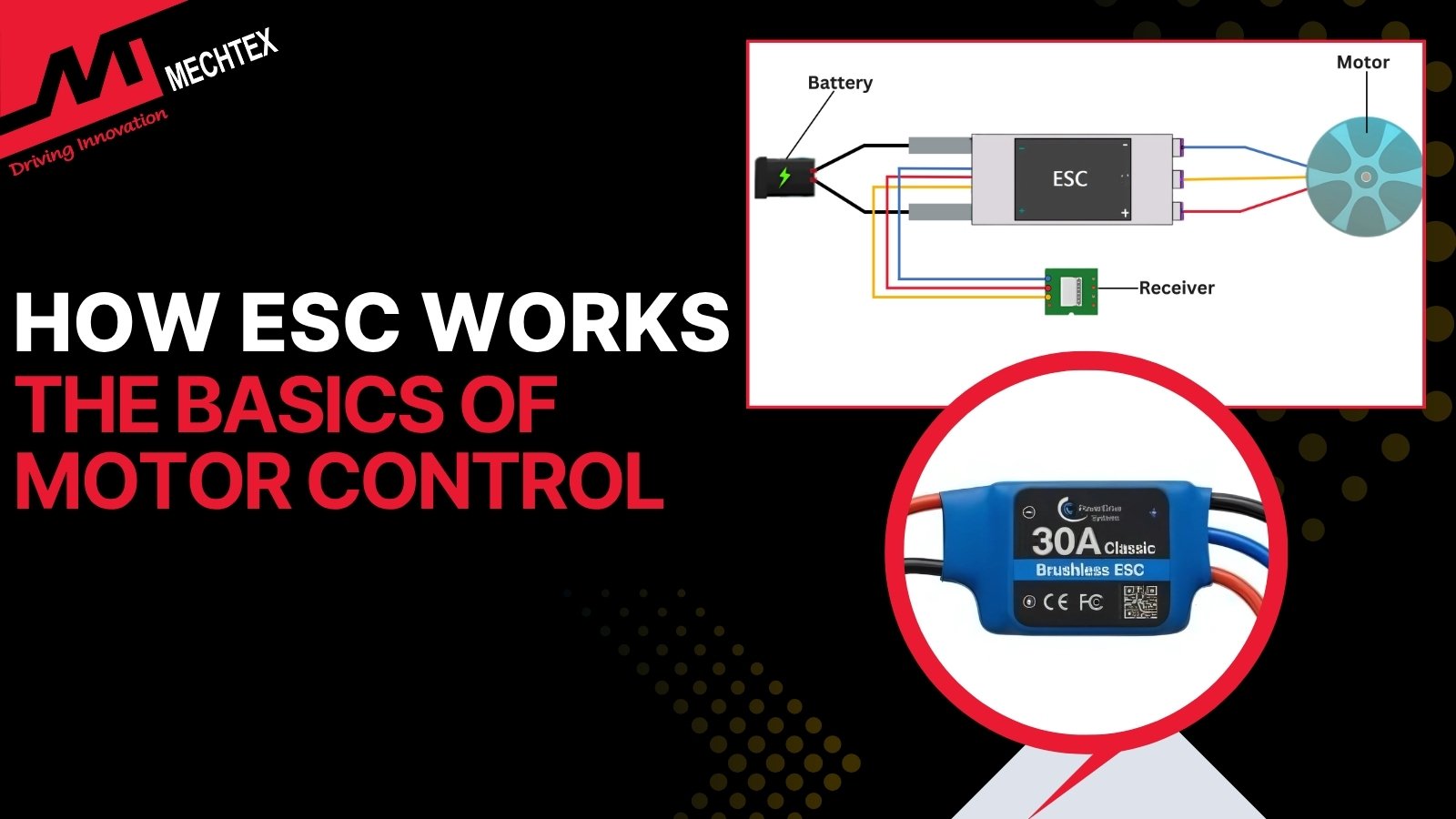
In the rapidly growing world of robotics, drones and based on user electric mobility, the Electronic Speed Controller (ESC) has emerged as a crucial component in motor control systems.
Whether it’s powering a drone, driving an electric vehicle, or operating a robotic actuator, the ESC plays a vital role in ensuring smooth, efficient, and responsive motion.
In this blog, we will explore the fundamentals of ESC, its working, and how it interacts with brushless motors to deliver precise control over speed and direction.
What is an Electronic Speed Controller (ESC)?
An electronic speed controller (ESC) is an essential component used in electric-powered systems such as drones, RC vehicles, e-bikes, and robotics to manage the speed and direction of the electric motor. It acts as a bridge between the power source (battery) and the motor to ensure smooth and precise operation based on user input or programmed instructions.
ESCs are typically designed for two types of motors - Brushed DC motors and Brushless DC motors. In drone applications, brushless ESCs are widely used for their efficiency, reliability and light weight.
ESC works by converting the DC voltage from the battery into a modulated signal (using PWM) to control motor speed. The controller receives signals from the flight controller, throttle, and transmitter to adjust the power of the motor.
Watch the YouTube Video by "Painless360" to learn some basics about ESCs.
It ensures that the motor runs at a desired speed, maintains stability, and responds promptly to changes in commands. It comes in various current ratings and sizes, allowing users to select one that matches their electric motor and application requirements.
In summary, an ESC plays a vital role in controlling motor dynamics, improving system efficiency, and protecting components from electrical stress, making it indispensable for modern electric propulsion systems.
How ESCs Work?
An electronic speed controller (ESC) is a crucial device that controls the speed, direction, and braking of an electric motor. Its operation is rooted in power electronics and digital signal processing to enable precise motor control with real-time responsiveness.
At its core, ESC starts by receiving the pulse width modulation (PWM) signal from the flight controller or transmitter. This signal contains the speed command, which the ESC interprets and converts into high-power signals suitable for driving the motor.
The ESC modulates the DC power from the battery using high-frequency switching of MOSFETs to regulate the voltage and current sent to the motor.
For Brushless DC motors, ESCs use a three-phase output, which carefully time the switching of current through the motor windings to create a rotating magnetic field. This field interacts with the permanent magnets in the rotor and causes it to rotate.
The timing of the switching of the current is either controlled via sensorless techniques, such as back-EMF or sensor-based feedback, hall sensor, to ensure smooth and synchronised commutation.
For Brushed DC gear motors, the process is simple. The ESC adjusts the duty cycle of the PWM signal applied to the electric motor terminals to effectively control the voltage and speed without switching phases.
Modern ESCs also incorporate microcontrollers and firmware, which allows features like soft-start, overcurrent protection, temperature monitoring, low-voltage cutoff, regenerative braking, and telemetry.
It not only enhances motor performance and efficiency but also protects the system from damage due to overloading and overheating.
Key Parameters Controlled by ESCs
An Electronic Speed Controller (ESC) manages multiple parameters to ensure efficient, smooth, and safe operation of electric motors. These key parameters include:
- Motor Speed (RPM)
The primary function of the ESC is to regulate the motor's speed based on input commands. It does this by adjusting the duty cycle of the PWM signal to control the voltage applied to the motor.
- Direction of Rotation
ESCs can change the direction of the motor by altering the energising sequences of motor windings. This is crucial in applications like drones, where reversing thrust enables quick directional changes.
- Throttle Response
ESCs manage how quickly the motor reacts to input challenges, which allows for smooth acceleration and deceleration based on programmed throttle curves.
- Voltage and Current Limits
Advanced ESCs monitor input voltage and output current to protect against over-voltage, under-voltage, and overcurrent conditions that could damage the system.
- Temperature Protection
Built-in temperature sensors allow ESCs to prevent overheating by reducing power or shutting down when thermal limits are exceeded.
ESC Firmware and Protocols
ESC can run on various firmware options depending on the applications. Some popular open-source and commercial firmwares are:
Popular ESC Firmware Options
- BLHeli / BLHeli_S / BLHeli_32
Widely used in high-performance systems requiring fast responses, such as PV drones, RC vehicles, robotics, and aerial cinematography platforms. These firmwares offer smooth throttle response and motor timing control.
- SimonK
This firmware is known for its simplicity and efficiency. SimonK is ideal for small UAVs, educational robotics kits, and hobby-grade applications that prioritise the ease of setup and reliability.
- VESC (Vedder ESC)
A highly configurable open-source firmware designed for electric skateboards, e-bikes, robotics, industrial automation, and research projects. VESC supports advanced control methods.
Common Communication Protocols
- PWM (Pulse Width Modulation)
The most widely used protocol for RC systems, robotics, and basic industrial motor control. Simple to implement, but may have latency compared to the modern alternatives.
- Oneshot125 / Oneshot42 / Multishot
It is a high-speed analogue protocol that offers lower latency than PWM. Ideal for flight controllers in drones, fast-response servo systems, and RC vehicles.
- DShot (Digital Shot)
A digital signal protocol offering precise control without requiring calibration. It is used in racing drones, precision robotics, CNC systems, and other latency-sensitive applications.
- CAN / UART / I2C
Digital series commutation interfaces are common in industrial automation, autonomous systems, research platforms, and smart ESC systems.
Conclusion
ESCs are the backbone of modern electric motion systems. They bridge the gap between digital control signals and raw electrical power, offering precise and reliable motor control. Whether you're flying a drone, powering a robot, or designing an electric vehicle, understanding how ESCs work is essential to unlocking optimal performance.
From basic speed regulation to sophisticated sensor feedback systems, ESCs continue to evolve, fueling innovation across industries.