How to Calculate Stepper Motor Power and Efficiency
Power in the stepper motor refers to the electrical input converted into mechanical motion, measured as W. Efficiency in stepper motors is the ratio of mechanical power output to the electrical power output expressed as a percentage (%). Calculating both factors are crucial for optimising performance and minimising energy waste.
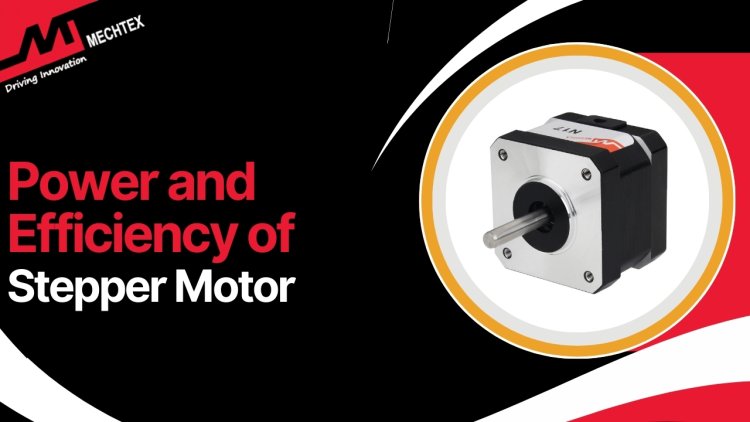
Stepper motors are widely used in automation, robotics and CNC machines due to their precise control and reliability. However, calculating the stepper motor’s power and efficiency is crucial for optimising performance and minimising energy losses. In this blog, we explore what a stepper motor is, methods to calculate its power and efficiency and factors affecting the efficiency of a stepper motor.
What is Stepper Motor?
The Stepper motor is a brushless DC motor that moves in precise steps rather than continuous rotation. It converts electrical pulses into precise mechanical movements making it ideal for applications requiring accurate positioning and speed control.
The working of the stepper motor is based on the principle of electromagnetic induction. The stator consists of multiple windings arranged in phases, and the rotor aligns itself with the energised stator poles. By sequentially energising the stator winding, the rotor moves at fixed angular steps. The common step angle of the stepper motor is 1.8 degrees.
Stepper motors offer several advantages such as high positional accuracy, open-loop control, and high torque at low speed, which makes them suitable for applications like CNC machines, 3D printers, robotics, medical devices, and automation systems where smooth operation is required.
Also Read
Power in a Stepper Motor
Power in the stepper motor is divided into two types: electrical input power and mechanical input power. Understanding both types of power is essential for optimising its performance.
1. Electrical Power
Electrical power in the stepper motor is the energy supplied to the windings to generate magnetic fields that drive motion. It depends upon the voltage, current and number of phases. The power drawn by each phase contributes to the total power input.
Since the stepper motor operates in discrete steps, its power consumption remains relatively stable compared to continuously rotating motors.
The electrical power in the stepper motor is determined by the voltage and current supplied to each phase and is given by the following formula:
Pelec = V x I
Where,
Pelec = Electrical input power (Watts)
V= Voltage supplied to the motor (Volts)
I= Current drawn by the motor (Amperes)
Use the following formula to calculate power for a multi-phase motor:
Ptotal = Pelec x Number of Phases
For Example:
-
-
Voltage (V) = 24 Volts
-
Current (I) = 2 Amperes
-
Number of Phases = 3 (since it's a three-phase stepper motor)
-
Step 1: Calculate the electrical input power for a single phase (Pelec)
Using the formula:
Pelec = V x I
Pelec = 24 V x 2 Amps
Pelec = 48 Watts
Therefore, the electrical input power for a single-phase motor is 48 Watts.
Step 2: Calculate the total electrical power for a multi-phase motor
Now, since it's a three-phase motor, we multiply the single-phase electrical power by the number of phases:
Ptotal = Pelec x Number of Phases
Ptotal = 48 x 3
Ptotal = 144 Watts
Therefore, the electrical input power for a multi-phase motor is 144 Watts.
2. Mechanical Power
Mechanical power in the stepper motor refers to the useful power output that results in rotational motion. It depends upon the torque produced and rotational speed.
Since the stepper motor moves in discrete steps, the output power varies with load conditions and step frequency. The power generated is used to drive loads like conveyor belts, robotic arms, and CNC machines.
The mechanical power calculation considers both torque and angular velocity, to ensure the stepper motor operates efficiently for precision applications.
The mechanical power of the stepper motor is calculated by the following formula:
Pmec = T x ω
Where,
Pmec = Mechanical input power (Watts)
T = Torque produced by the motor (Newton-meters)
ω = Angular velocity (radians per second)
Angular velocity can be determined as:
ω = 2π x N/60
Where N is the speed of the motor in revolutions per minute (RPM).
For Example:
-
-
Torque (T) = 0.5 Newton-meters
-
Angular Velocity (ω) = 50 radians per second
-
Step 1: Calculate the mechanical power (Pmec)
Using the formula:
Pmec = T x ω
Pmec = 0.5 Nm x 50 rad/s
Pmec = 25 Watts
Therefore, the mechanical power of a stepper motor is 25 Watts.
3. Efficiency in Stepper Motor
Efficiency in stepper motors is the ratio of mechanical power output to electrical power output, which is expressed as a percentage (%). It indicates how effectively the stepper motor converts electrical energy into useful motion.
Since the stepper motor operates in discrete steps and consumes power, its efficiency is lower than other motors. Its efficiency depends upon operating speed, torque, and drive method.
The efficiency of the stepper motor is calculated using the following formula:
η = Pmec/Ptotal x 100%
Where,
Pmec = Mechanical input power (Watts) (T x ω)
Ptotal = Electrical input power (Watts) (V x I x Number of Phases)
For Example:
-
- Ptotal = 144 Watts
-
- Pmec = 25 Watts
Calculate the Efficiency (η) of a Stepper Motor
Using the following formula:
η = Pmec/Ptotal x 100%
η = 25/144 x 100%
η = 17.36%
Therefore, the efficiency of a stepper motor is 17.36%
Factors Affecting Stepper Motor Power and Efficiency
Stepper motors typically have lower efficiency compared to other motor types due to inherent losses. Some factors affecting efficiency include:
- Voltage and Current
The input voltage and current determine the power delivered to the stepper motor. Higher voltage can improve torque at high speeds, but excessive current may lead to heat generation, reducing efficiency. Conversely, lower voltage can save energy but may limit performance.
- Motor Design
The type of stepper motor influences its power efficiency. Bipolar stepper motors typically provide higher torque but require more complex control circuitry, while unipolar motors are simpler but less efficient.
- Load Conditions
Power efficiency is highly dependent on the load the stepper motor is driving. Light loads may lead to inefficient power usage, while underload stepper motors often run inefficiently due to poor torque performance.
- Speed and Torque
Stepper motors are most efficient when operating at their rated speed and load. Running at speeds higher than their optimal range can lead to increased consumption and reduced efficiency due to the need for additional current to maintain torque.
- Winding Resistance
The resistance of windings affects the current drawn by the stepper motor. Lower resistance reduces heat generation and improves efficiency, while higher resistance increases power loss as heat.
Factors to improve Stepper Motor Power and Efficiency
Improving the power and efficiency of stepper motors requires addressing several key factors. Some of the factors are:
- Current Control Techniques
Implementing advanced current control methods such as micro-stepping or vector control allows for smoother operation. Microstepping reduces the torque ripple and energy consumption, which leads to better performance.
- Voltage Optimisation
Operating stepper motors at their optimal voltage ensures that they deliver maximum power output while minimising heat losses. Using a power supply that can match the motor's voltage requirements helps in achieving better efficiency.
- Heat Dissipation
Managing heat generation is crucial for efficiency. Using heat sinks or fans to dissipate excess heat will maintain the optimal temperature range and allow stepper motors to run more efficiently without power losses due to overheating.
- Use of High-Efficiency Materials
Selecting magnets and other materials with high-quality ratings, such as low-hysteresis cores or advanced alloys can reduce losses and enhance overall power efficiency.
Conclusion
Calculating stepper motor power and efficiency is crucial for optimising performance and minimising energy waste.
By understanding electrical input power, mechanical output power, and efficiency factors, one can make informed decisions when designing motion control systems. Implementing strategies to improve efficiency can lead to better performance, lower energy consumption, and longer motor lifespan.