Scalar Control vs. Vector Control Technique for Synchronous Motor
Scalar control and vector control are two popular methods used for controlling synchronous motors. Scalar control technique is a method that regulates the magnitude of key variables to achieve the desired performance. The vector control technique is an advanced method used to achieve precise control over speed and torque.
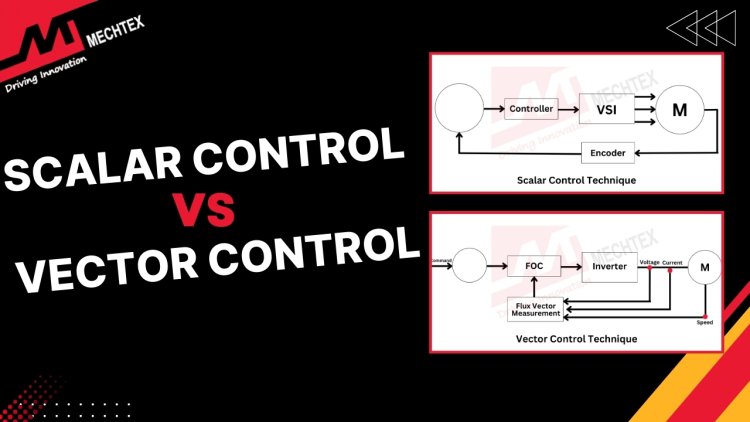
Synchronous motors are the cornerstone of modern and industrial applications. Their high efficiency, precision, and reliability make them ideal for numerous applications. To maximise the benefit of synchronous motors, effective control strategies are essential. The two most common control strategies for synchronous motors are scalar control and vector control.
In this blog, we delve into the principles, advantages, and limitations of each control strategy and offer a comparative analysis to help you better understand their applications.
What is a Synchronous Motor?
A Synchronous motor is an AC motor whose rotational speed is synchronised with the frequency of AC supply. Unlike induction motors, which rely on slip to generate torque, synchronous motors maintain a constant speed regardless of load variation. This makes them ideal for applications requiring precise and constant speed.
The construction of a synchronous motor consists of stator and rotor. The stator is the stationary part of a synchronous motor which produces a magnetic field when powered by an AC supply. The rotor is a rotating part of a synchronous motor equipped with permanent magnets or windings connected to a DC excitation source.
Watch the YouTube video by "JAES Company" to learn about the working of synchronous motor
The working of synchronous motors involves interaction between the rotating magnetic field (RMF) of the stator and the magnetic field of the rotor. Initially, the rotor cannot synchronise with the stator’s magnetic field due to lack of induced torque. External mechanisms like a pony motor or variable frequency drive (VFD) bring the rotor close to synchronous speed. Once the rotor is aligned it locks with the stator’s magnetic field and maintains a synchronous speed.
Synchronous motors are commonly used in conveyors, compressors, mills, and power systems for constant speed regulation.
Also Read
What is a Synchronous Motor? | Construction, Working Principle and Applications
Scalar Control Technique
The scalar control technique for synchronous motors is a basic method that regulates the magnitude of key variables such as voltage and frequency to achieve the desired performance. This technique focuses on controlling the synchronous motor’s steady-state behaviour and making it ideal for applications where high precision and dynamic performance are not critical.
A central aspect of the scalar control technique is the voltage-frequency ratio (V/f), where the supply voltage is adjusted proportionally with the supply frequency. This ensures that the synchronous motor operates within the magnetic saturation limit to maintain consistent torque.
The scalar control technique is typically an open-loop system, which means it does not rely on feedback from sensors for motor speed or position. This technique is a straightforward technique and requires minimal computational resources.
Vector Control Technique
The vector control technique for synchronous motors is also known as the field-oriented control (FOC) technique. It is an advanced method used to achieve precise control over speed and torque.
Unlike the scalar control technique, which regulates the magnitude-based variables, vector control focuses on controlling both the magnitude and direction of the synchronous motor’s electromagnetic field providing superior dynamic performance.
A key feature of the vector control technique is the separation of the synchronous motor current into two components: one for producing torque (q-axis current) and another for controlling the magnetic field (d-axis current). By independently controlling these components in a rotating frame, vector control allows the motor to respond quickly to changes in load or speed.
This technique typically uses feedback from sensors, such as encoders or resolvers to monitor the rotor’s position and speed. The feedback enables real-time adjustments which ensures optimal performance under varying operating conditions.
The high precision and fast dynamic response of vector control make it ideal for demanding applications.
Scalar Control Technique vs Vector Control Technique
Scalar control and vector control are two popular methods used for controlling electric motors, particularly AC synchronous motors. They differ significantly in their control strategies, applications, and performance characteristics. Here's a detailed comparison:
- Control Principle
Scalar Control: Operates based on a steady-state relationship and maintains a fixed voltage-frequency ratio (V/f). It focuses on controlling the magnitude of synchronous motor parameters without considering their dynamic interaction.
Vector Control: Utilises real-time control of synchronous motor current components. It separates torque-producing and flux-producing currents for precise management.
- Dynamic Performance
Scalar Control: Limited to steady state operation, making it unsuitable for applications that require rapid response to load or speed changes.
Vector Control: Offers quick response by dynamically adjusting the current components making it ideal for applications that require quick response to load variations.
- Complexity
Scalar Control: Simple in design and requires minimal computational program and basic hardware.
Vector Control: Complex design involves advanced algorithms, motor modelling, and sophisticated hardware to execute control strategies effectively.
- Accuracy
Scalar Control: Provide precise control over torque and speed of synchronous motor which leads to suboptimal performance in demanding applications.
Vector Control: Deliver highly precise control over speed and torque which is crucial for high-precision applications such as robotics and CNC machines.
- Applications
Scalar Control: Well-suitable for low-performance applications with steady operational requirements such as fans, pumps, and compressors.
Vector Control: Ideal for high-performance applications that require precision such as robotics, and CNC machines.
Conclusion
Both scalar and vector control techniques are integral to the effective operation of synchronous motors. While scalar control offers simplicity and cost-effectiveness, vector control provides precision and dynamic performance. Understanding the strengths and limitations of each technique is crucial for selecting the right control strategy for your specific application.
With technological advancements, the gap between these control strategies continues to narrow, paving the way for smarter and more efficient motor control solutions. Whether you’re designing an automation system or an industrial application, the choice of control strategy can significantly impact performance, efficiency, and overall success.