Load Characteristics of Synchronous Motor
Load characteristics of a Synchronous Motor refer to the motor’s behaviour under varying load conditions. The synchronous motor operates at a synchronous speed regardless of load changes. This characteristic distinguishes synchronous motors from other types of motors.
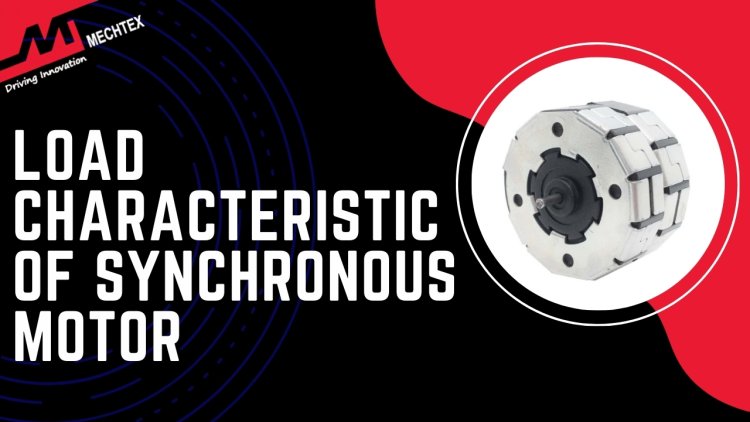
A synchronous motor is a type of AC motor where the rotor’s rotation speed is synchronised with the frequency of the power supply. The construction of a synchronous motor consists of two main components: stator and rotor. The stator is a stationary part of a synchronous motor and creates a rotating magnetic field when power is supplied. The rotor is the rotating part of the synchronous motor which interacts with the stator and generates a magnetic field for rotation. A synchronous motor works when the stator generates a rotating magnetic field using an AC power supply. The rotor interacts with the stator's rotating magnetic field and reaches a specific speed. After reaching a specific speed, the rotor locks itself with the magnetic field and starts rotation.
Unlike induction motors, where the rotor operates at a slower speed than the magnetic field, synchronous motors maintain a constant speed regardless of the load, as long as the load does not exceed the motor’s capacity. Understanding the load characteristics of a synchronous motor and how this motor will work under varying load conditions is important to ensure smooth operation.
In this blog, we'll explore the load characteristics of synchronous motors, including their relationship to power factor, torque, and stability.
Overview of Load Characteristics of Synchronous Motor
In a synchronous motor, load characteristics refer to the motor’s behaviour under varying load conditions. The synchronous motor operates at a synchronous speed regardless of load changes. This characteristic distinguishes synchronous motors from other types of motors and makes them ideal for various applications.
When a synchronous motor operates at varying load conditions, its performance is influenced by several factors such as:
- Torque and Load Angle (δ)
- Power Factor
- Current Draw
Torque and Load Angle
The torque developed in a synchronous motor depends upon its load angle. The load angle is the angle between the rotor’s magnetic field and the stator’s magnetic field. This relationship can be expressed as
T ∝ Vs × Er × sin(δ)
- T is the torque,
- Vs is the stator voltage,
- Er is the rotor’s back EMF,
- δ is the load angle.
At no load, the rotor of the synchronous motor is perfectly aligned with the stator’s magnetic field and the load angle is nearly zero (0). As the load increases, the rotor lags behind the stator’s magnetic field which increases the load angle.
Also Read
Understanding the Torque of Synchronous Motor
Characteristics of Load
Synchronous motors exhibit different characteristics depending upon the load applied. Some important characteristics are:
- At No Load
At no load, the synchronous motor operates with a minimal load angle and draws less current. A synchronous motor runs at synchronous speed, which improves its overall efficiency.
- Increasing Load
As the load increases, the synchronous motor’s load angle increases and its power factor tends to achieve unity and the synchronous motor runs at a synchronous speed.
- Overload
Beyond a certain load, if the load increases excessively, the synchronous motor reaches its pull-out torque point. At this point, the rotor cannot maintain its synchronisation with the stator’s magnetic field and the synchronous motor loses stability, eventually stopping.
Power Factor and Load
One of the key advantages of synchronous motors is their ability to control power factor. This makes them particularly useful in various power factor correction applications. The power factor depends on the various excitation levels of the synchronous motor. Some important excitation levels of synchronous motors are:
- Under excited Operation (Lagging Power Factor)
If the synchronous motor is under-excited, the rotor’s magnetic field is weaker than the stator’s magnetic field and causes a lagging power factor.
- Over-excited Operation (Leading Power Factor)
When the synchronous motor is over-excited, the rotor’s magnetic field becomes stronger than the stator’s magnetic field, resulting in a leading power factor. This operation is useful for compensating for inductive loads in the power system, improving overall efficiency.
- Unity Power Factor
By adjusting the excitation, the synchronous motor operates at the unity power factor. This is the most efficient operating condition of synchronous motors for various applications.
Current Draw vs Load
In a synchronous motor, the relationship between the current draw and load is directly influenced by the synchronous motor field excitation and load demand. Under no load condition, the synchronous motor draws minimal current and primarily becomes reactive to maintain the magnetic field.
When a synchronous motor operates at a constant speed, the motor current increases with load due to high torque requirement. The stator has both reactive and active components. The active component rises as the load increases, reflecting the need for high mechanical power.
Meanwhile, reactive power depends upon the motor’s field excitation. If the motor is under-excited, the stator draws more lagging reactive current and increases the over-current in the motor. Conversely, if the motor is over-excited, it will draw less reactive current and reduce the overall current in the motor.
As the load continues to increase, the AC motor will draw more current to produce higher torque until it reaches the pull-out torque point. Beyond this point, the motor loses synchronism and stalls.
The synchronous motor's ability to regulate power factor through field excitation provides flexibility in current draw, but proper excitation is crucial to avoid excessive current that can lead to overheating or inefficient operation.
Effect of Load on Efficiency of Synchronous Motor
The efficiency of a synchronous motor is influenced significantly by the load applied to it. As the load increases, several factors come into play that affect the performance of synchronous motors. Three different load conditions of synchronous motors are as follows:
- Light Load
When a synchronous motor operates under a light load, its efficiency is very low. This is because the fixed losses such as core loss, friction, and windage loss remain constant. With less power output the ratio of useful power to input power is lower, thereby reducing efficiency.
- Full Load
At or near full load, the efficiency of the synchronous motor reaches its peak. The power input is more effectively utilised for smooth operation and fixed losses become smaller.
- Overload
Operating a synchronous motor under overload conditions results in a significant drop in efficiency. Overload increases the I²R losses (copper losses) in the stator and rotor windings, causing higher heat generation and reduced energy efficiency.
Thus, to maximise efficiency, synchronous motors should be operated close to their rated load conditions.
Types of Stability of Synchronous Motor
Synchronous motors experience different types of stability under load, each affecting their performance. The primary types of stability of synchronous motors are:
- Steady-State Stability
It refers to the synchronous motor’s ability to maintain synchronous speed under small and gradual load variations. A synchronous motor has steady-state stability, after a small change in load, it will return to its synchronous operation without losing synchronism.
- Transient Stability
Transient stability deals with the synchronous motor’s response to sudden and large disturbances. If the synchronous motor returns to synchronism after a significant disturbance without losing stability, it exhibits transient stability.
- Dynamic Stability
Dynamic stability refers to a synchronous motor’s ability to damp out oscillation that occurs due to disturbances or changes in load. A synchronous motor with good dynamic stability will reduce oscillations and quickly settle back into stable operation after a disturbance.
- Voltage Stability
Voltage stability refers to the synchronous motor’s stability in maintaining stable operation when the voltage supply fluctuates. A sudden voltage drop can cause a synchronous motor to lose its synchronism, especially if the excitation system cannot respond quickly.
Each of these stability types plays a critical role in ensuring that synchronous motors function effectively under different load and disturbance scenarios.
Conclusion
Understanding the load characteristics of synchronous motors is essential for optimising their performance in industrial applications. The ability to maintain a constant speed, control power factor, and manage load conditions effectively makes synchronous motors a preferred choice in many sectors. By carefully considering factors like torque, power factor, current draw, and efficiency under load, engineers can ensure optimal motor performance and longevity.