Star Winding vs Delta Winding Configurations in BLDC Motors
In the star winding configuration of the BLDC motor, three stator windings are connected at a central point and form Y shape. In the delta winding configuration, three stator windings in a closed loop resemble a triangle. It significantly impacts the performance, efficiency, and application suitability of BLDC Motor.
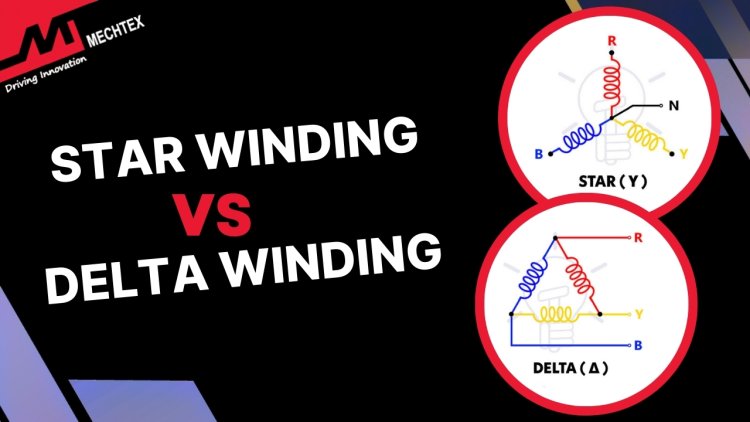
BLDC motors are widely recognised for their efficiency, reliability, and compact design. A critical aspect of BLDC motor design is that their performance is influenced by winding configuration.
There are two types of winding configurations in BLDC Motor - Star (Y) or Delta (∆). These configurations determine the electrical and mechanical characteristics of the BLDC motor and impact its torque, speed and efficiency. In this blog, we will delve into the differences between Star and Delta configurations, their advantages, and their applications.
What is BLDC Motor?
A BLDC motor is a highly efficient and reliable electric motor that has become essential in modern applications. Unlike traditional DC motors, which use brushes and a commutator. BLDC motors rely on electronic commutation which is controlled by an external driver or controller. This design improves the BLDC motors durability and performance and makes them ideal for various applications.
The construction of BLDC motors consists of rotor, stator and hall sensors. Rotor is the rotating part of the BLDC motor and consists of permanent magnets. The stator is the stationary part of the BLDC motor and consists of windings. Hall sensors are used to detect the position of the rotor and optimise the performance of the BLDC motor.
Watch the YouTube Video by "Sabins Civil Engineering" to learn about the working of BLDC Motor.
The working of the BLDC motor is based on the interaction between the stator and rotor. When stator windings are being energised in a specific sequence with the help of a controller, it creates a rotating magnetic field. This field interacts with the rotor to generate the torque required for movement. Hall sensors detect the position of the rotor and provide feedback to the controller for precise control of speed and torque.
BLDC motors offer numerous advantages. They are highly efficient, provide excellent torque, and operate quietly. Due to their features, BLDC motors are used in a wide range of applications, including drones, electric vehicles, industrial automation systems, robotics, and home appliances.
Also Read
What is a BLDC Motor| Construction, Working and Applications
What is Star (Y) Winding Configuration?
The star winding configuration of the BLDC motor is also known as the Y Configuration of the BLDC motor. It is the most common type of stator winding in Brushless DC motors. In this winding type, the three stator windings are connected at a central point called the neutral point, forming Y shaped electrical connection. The other ends of the windings are connected to the BLDC motor terminals interfacing with the electronic speed controller for operation.
This configuration is suitable for BLDC motors to deliver high efficiency at low speed. This design inherently reduces the phase voltage applied to the windings, which results in better torque performance under low-speed conditions. This characteristic makes BLDC motors ideal for applications requiring precision and smooth control, such as industrial automation, medical equipment, and robotics.
Another advantage of the star configuration is its thermal performance. By drawing less current for a given output, the BLDC motor operates with less heat which improves its reliability and lifespan.
While the star configuration excels at low-speed torque and efficiency, it may not achieve high-speed performance. Nevertheless, its advantages in controlled environments make it a popular choice for applications prioritising torque, smoothness, and thermal stability.
What is Delta (∆) Winding Configuration?
The delta winding configuration is another important type of winding configuration in BLDC motors. It connects the three stator windings in a closed loop resembling a triangle (∆). In this configuration, each winding end is connected to other winding windings beginning and creating a continuous circuit. Unlike the star configuration, the delta setup has no neutral point.
This winding configuration is advantageous for high-speed operation and applications requiring high power output. The phase voltage in the delta configuration equals the line voltage which leads to increased current flow through the windings. As a result, delta-configuration BLDC motors generate higher torque at higher speeds compared to star-configuration BLDC motors.
However, the delta configuration has some trade-offs. The higher phase current can lead to greater heat generation and making thermal management crucial to prevent overheating. Additionally, the efficiency of a delta configuration at low speeds may not match that of a star configuration, as it draws more current for the same torque.
Therefore, Delta winding configurations are commonly used in applications requiring robust performance at high speeds, such as compressors, pumps, high-speed fans, and certain drone applications.
Star vs. Delta Winding Configuration in BLDC Motors
Both Star (Y) and Delta (Δ) winding configurations are widely used in Brushless DC motors. Each configuration affects the motor's performance, efficiency, and application suitability differently. Here are some key differences between star and delta winding configurations:
Connection Layout
- Star (Y) Configuration
One end of each winding is connected to a common neutral point, forming a star shape.
- Delta (∆) Configuration
Windings are connected in a closed loop with no neutral point, forming a triangle.
Voltage and Current
- Star (Y) Configuration
The phase voltage is lower than the line voltage. It results in a lower phase current.
- Delta (∆) Configuration
The phase voltage equals the line voltage, leading to a higher phase current compared to the star winding configuration.
Torque and Speed
- Star (Y) Configuration
Provides higher torque at low speed due to the better efficiency at low RPM. It makes BLDC motors ideal for applications requiring precise low-speed control.
- Delta (∆) Configuration
Deliver better torque at high RPM due to increased phase voltage which makes them suitable for higher-speed applications.
Efficiency
- Star (Y) Configuration
More efficient at low speed due to low copper losses and better current distribution.
- Delta (∆) Configuration
More efficient at high speed due to the high torque and power demands.
Applications
- Star (Y) Configuration
Used in applications requiring smooth operation, low starting torque and high efficiency such as robotics, and fans.
- Delta (∆) Configuration
Common in high-speed, high-power applications such as electric vehicles, and industrial machinery.
Choosing the Right Winding Configuration for Application
The selection of a winding configuration for a BLDC motor depends on the application requirements. Some Key factors are:
- Load Characteristics
For low load and high precision applications, star (Y) winding configuration is preferred. For high load and high torque applications, delta (∆) winding configuration is preferred.
- Speed Requirements
Star (Y) winding configuration is suitable for low-speed applications. Delta (∆) winding configuration is ideal for high-speed applications.
- Efficiency Needs
For long-term operation and minimal losses, the star (Y) winding configuration is superior. For better efficiency in high load conditions, the delta (∆) winding configuration is suitable.
- Power Supply
If the available power supply provides line voltage, star (Y) winding configuration is ideal. Power supply with high voltage line, delta (∆) winding configuration is suitable.
Conclusion
The choice between Star and Delta winding configurations in BLDC motors significantly impacts performance, efficiency, and application suitability. Star configurations excel in low-speed, precision-demanding applications, while Delta configurations shine in high-speed, high-torque scenarios.
Understanding these distinctions enables engineers and designers to optimise BLDC motor performance for specific use cases. Whether for robotics, aerospace, or industrial machinery, selecting the right winding configuration ensures optimal performance and reliability.