Field-Oriented Control (FOC) for BLDC Motors: A Beginner’s Guide
Field-oriented control of BLDC Motor is an advanced control method that regulates the BLDC motor’s magnetic field and current to achieve smooth, precise and efficient operation. It helps BLDC motors to maintain high efficiency across a wide range of speeds, making it indispensable in modern motor applications.
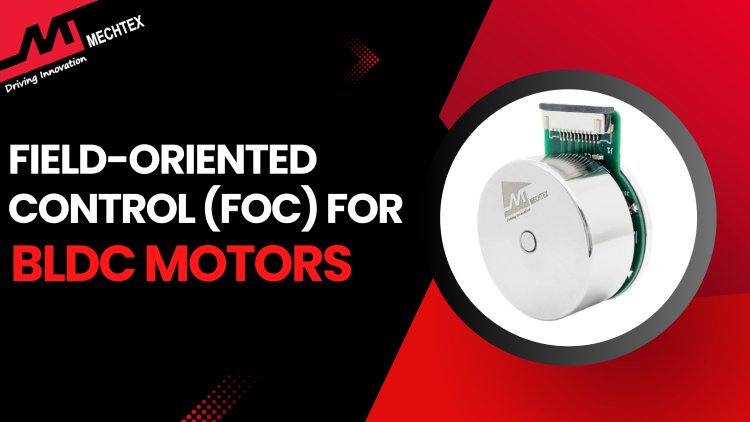
What is a BLDC Motor?
A BLDC motor is an electric motor that operates using electric commutation instead of mechanical brushes and a commutator. It consists of two main components: stator and rotor. The stator consists of copper winding and the rotor consists of permanent magnets. Unlike traditional DC motors, BLDC motors use electronic controllers to switch current direction through stator windings and eliminate the need for brushes.
Watch the YouTube video by "Lesics" to understand the working principle of BLDC Motors
The working principle of the BLDC motor involves interaction between the rotor’s magnets and the stator’s magnetic field. As the current flows through the stator, it creates a rotating magnetic field that causes the rotor to turn. Hall sensors are also often used to track the rotor’s position and send feedback to the controller to enable precise control over the speed and torque.
BLDC motors are known for their compact size, lightweight, high efficiency and long operational life, making them ideal for applications like electric vehicles, drones, HVAC systems, and industrial machinery.
Also Read
What is a BLDC Motor| Construction, Working and Applications
What is the Field-Oriented Control (FOC) of the BLDC Motor?
Field-oriented control of BLDC Motor is an advanced control method that regulates the motor’s magnetic field and current to achieve smooth, precise and efficient operation. Unlike traditional control methods, the field-oriented control (FOC) method aligns the stator current with the rotor’s magnetic field to optimise the speed and torque control for superior performance. It also enables accurate control over BLDC motors resulting in smoother efficiency and better operation at a wide range of speeds.
Watch the YouTube video by "GreatScott!" to know why FOC is used in BLDC Motors.
Key Components of FOC in BLDC Motors
Field-Oriented Control (FOC) in BLDC motors is an advanced control technique used to achieve smooth and efficient motor operation. Here's how each key component of FOC helps in improving BLDC motor operation:
- Clarke and Park Transformations
Clarke transformation converts the three-phase stator current (a,b,c) into two orthogonal components (α, β) in a stationary reference frame. On the other hand, peak transformation further converts these components into rotating reference frames (d, q), aligning them with the rotor’s magnetic field. It simplifies the control by turning AC signals into DC quantities.
- Proportional-Integral (PI) Controllers
Proportional-integral (PI) Controllers regulate the d and q-axis currents by comparing the reference values with the actual motor current. The PI controllers adjust the pulse width modulation (PWM) to maintain the desired current levels.
- Space Vector Modulation (SVM)
SVM is used to generate the optimal switching sequence of the inverter, converting signals into appropriate voltages for motor windings. It enhances the performance of the BLDC motor by reducing the noise and vibrations.
- Inverter
The inverter switches the DC supply to the motor phases based on control signals generated by FOC algorithms. The inverter is responsible for controlling the direction and magnitude of the current flow in each phase of the motor.
- Rotor Position Sensor
Field-Oriented Control (FOC) of BLDC motors requires precise rotor position information obtained from sensors like encoders and other techniques. The rotor position is crucial to synchronise the stator currents with the rotor's magnetic field.
Working of FOC in BLDC Motors
The working of Field-Oriented Control (FOC) of BLDC motors starts by measuring the three-phase current of BLDC motors. These currents are essential for understanding the motor’s current operating state. The three-phase current is transformed into d-axis and q-axis components which simplifies the control process by separating the torque and flux producing currents.
The q-axis current (torque-producing) and d-axis current (flux-producing) are regulated using a Proportional-Integral (PI) Controller. This controller adjusts the BLDC motor’s voltage to maintain the desired operating conditions. The regulated d-axis and q-axis currents are converted back into three-phase currents using inverse Clarke and Park transformations.
The output signals are passed through pulse width modulation (PWM) system, which generates the signals for the motor’s inverter. Finally, the inverter converts the control signals from PWM into three-phase voltage signals that drive the motor and complete the FOC loop.
Also Read
Pulse Width Modulation (PWM) Controls in BLDC Motor
Advantages of FOC in BLDC Motors
FOC offers several benefits that enhance motor performance and control, especially in precision-driven applications. Here are some advantages of FOC in BLDC motor:
- Improved Efficiency
FOC optimises the BLDC motor’s magnetic field reducing losses and improving overall efficiency.
- High Precision
By directly controlling the torque and flux-producing currents, FOC enables highly precise control over the motor’s performance making it ideal for applications like CNC machines and robotic arms.
- Better Response
FOC adapts quickly to changes in load and speed, providing fast and accurate control which is crucial for dynamic applications.
- Wide Speed Ranges
FOC allows BLDC motors to operate efficiently across a broad range of speeds from low RPM to high-speed applications.
Conclusion
Field-Oriented Control (FOC) revolutionises the way BLDC motors are controlled by providing precise and efficient regulation of torque and flux. Its ability to maintain high efficiency across a wide range of speeds, reduce torque ripple, and enhance precision makes it indispensable in modern motor applications, from robotics to electric vehicles.
For engineers and developers working with BLDC motors, understanding FOC is key to unlocking the full potential of these motors in advanced applications. As technology continues to evolve, FOC is set to become even more integral to the future of motor control systems.