Explore the different stepping modes of a stepper motor
There are three common stepping modes: full-step mode, half-step mode, and micro-stepping mode, which allow precise positioning and accurate control over rotor movement and make stepper motors suitable for various types of applications.
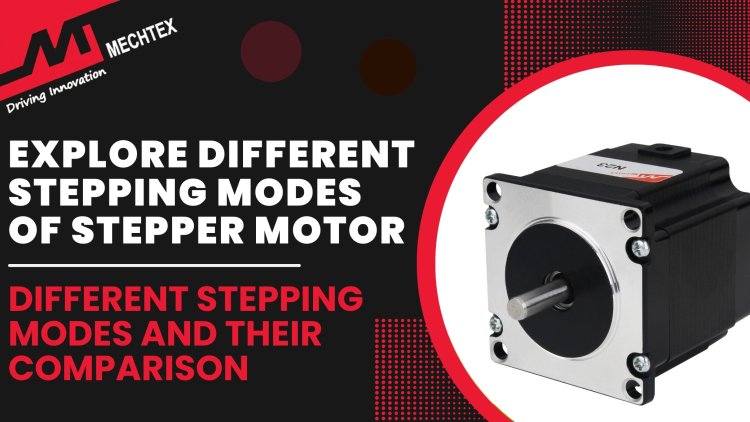
“With stepping modes, each step becomes a pillar of controlled seamless motion and setting the pace for accuracy and reliability."
Ever wondered how 3D printers and CNC machines achieve such precise and accurate movements? All thanks to the stepper motors. As the hands of the clock move at an accurate angle similarly stepper motor moves with discrete steps at a specific angle.
This motor follows a unique step pattern and angle to achieve accuracy and reliability. In this blog, we will cover what is a stepper motor, its different types of stepping modes, and how to select a stepper motor with the right stepping mode for seamless operation.
What is a stepper motor?
A stepper motor is a type of electric motor that converts electrical energy into mechanical movement. Unlike other electric motors, which continuously rotate when power is supplied, stepper motors move in discrete steps. Each step corresponds to a specific angle and allows precise control over the speed and position of the motor. For example, a clock's minute hand accurately points to specific minute markers every minute.
A stepper motor typically consists of a stator containing coils and a rotor composed of permanent magnets or multiple magnetic poles. The coils in the stator are arranged in pairs or specific configurations. When electric current flows through the coils of the stator, it creates a magnetic field. The rotor interacts with the magnetic field of the stator experiences a force, and starts rotating.
The working principle of the stepper motor is based on electromagnetism. When current flows through the stator windings, it generates a magnetic field that interacts with the poles of the rotor and causes it to rotate. Unlike other motors, that rotate continuously a stepper motor moves in discrete steps. Each step corresponds to a specific angle of rotation which is 1.8° per step.
The movement of the stepper motor is controlled by a stepper motor driver. It sends electrical pulses to the stator’s coil on correct timing and order. Each pulse from the stepper motor driver corresponds to each step of the motor, which allows for precise control over the motor’s position, speed and torque.
Stepper motors offer several advantages that make them ideal for precision motion control applications. One key advantage is their ability to provide high torque at low speeds allowing them to maintain precise positioning.
Another advantage is their ability to operate an open-loop system. It means they position the loads without any feedback devices such as encoders. Another advantage of stepper motors is their reliability due to their simple design, which results in minimal maintenance requirements and long operational lifetimes.
These advantages make the stepper motor an ideal choice for applications such as CNC machines, 3D printers, and robotic arms, where both accuracy and strength are required.
Also Read
How Hybrid Stepper Motor Works
Types of Stepper Motors
Stepper motors come in various types, sizes and configurations with specific characteristics suited for different applications. The main types of stepper motors are:
- Permanent Magnet (PM) Stepper Motor
A permanent magnet stepper motor consists of two main components: stator and rotor. The stator consists of windings arranged in specific sequences and the rotor is made up of the permanent magnet. When stator windings are energised, they create a magnetic field and attract the poles of the rotor causing it to move at a specific angle. PM stepper motors are also known for their simple design, low cost, and high torque at low speed. They are used for applications where precision is required such as 3D printers, CNC machines and many more.
- Variable Reluctance (VR) Stepper Motor
The stator of the variable reluctance (VR) stepper motor consists of a series of windings, while the rotor is made up of a non-magnetised soft iron core. When stator windings are energised in a specific sequence, the rotor moves to minimise the magnetic reluctance and align itself with stator poles. VR stepper motors are used in applications where high speed and high precision are required, such as in robotics, actuators, and automotive devices.
- Hybrid Stepper Motor
A hybrid stepper motor combines the features of both Permanent magnet (PM) stepper motor and Variable Reluctance (VR) stepper motor. Its rotor typically consists of a permanent magnet with toothed iron laminations, and the stator has winding poles with matching teeth. When the windings of the stator are energised in sequence, it creates a magnetic field. The rotor interacts with the magnetic field of the stator and moves at a specific angle. It helps to provide finer movement resolution, allowing for more precise control. Due to their precision and torque capabilities, hybrid stepper motors are widely used in CNC machines, 3D printers, medical equipment, and other applications that require fine positioning and reliable performance.
Also Read
Types of Stepping Modes of Stepper Motor
Stepping modes in stepper motors and hybrid stepper motors mean different sequences to energize the coil of the motor to create specific movements or steps. These modes show how the motor rotates between the discrete steps. Stepping mode in the stepper motor is used to control the movement and position of the rotor. Selecting an accurate stepping mode is important to optimize the motor performance for a particular application.
Let's take a look at different types of stepping modes in stepper motor
-
Full Step Mode
The full step is the basic stepping mode used to control the movement of the motor. In this mode, the motor rotates to one full step for every electrical pulse sent to the coil. In a traditional stepper motor, each phase consists of two coils. To take one full step in these motors, one coil of each phase is energized sequentially.
By controlling the sequence of energising and duration of each pulse, the motor can either clockwise or anti-clockwise. In a full-step mode, the rotor moves at a specific step angle for each pulse sent to the coil. It provides better torque to the motor but changes from one step to another sometimes creating noise and vibration in some applications.
-
Half-Step Mode
Half-step mode is a stepping mode that offers a balance between full-step and micro-stepping mode. In this mode, the motor takes half the size of the step as compared to the full-step mode steps. In a two-phase stepper motor, the coils are energised in such a way that first activates one coil at a time and then activates two coils simultaneously but at a low current level. It results in smaller steps as compared to full steps.
In half-step mode, the motor takes half the step angle for each pulse. This doubles the number of steps as compared to full-step mode but results in smoother operation and better resolution. Half-step mode improves the movement of the motor as smaller steps result in more precise control over the position of the motor and reduce the noise and vibrations.
-
Microstepping Mode
Microstepping mode is an advanced stepping mode used to achieve extremely precise control over the movement of the motor. In this mode, each step is divided into smaller micro steps. As compared to full-step and half-step modes, the micro-stepping mode offers better control over the movement of the motor.
In this mode, rather than energizing the coil fully or alternately, it involves applying various levels of current to the motor coil. By precisely changing the current level in the coil, the rotor can hold positions easily. The number of micro steps between each full step of the motor can be several dozen or more.
Microstepping in a stepper motor is beneficial for applications that require high precision, low vibration, and quiet operations such as CNC machines, 3D printers, and other automation systems.
Comparing the Stepping Modes of Stepper Motor
Full step mode vs Half step mode
In full-step mode, the motor rotates into the specific step angle with each pulse. Each step aligns with energising a single coil at a time. While in half-step mode, each full step is divided into two smaller steps. This mode alternates between energising one coil at a time and then energizing two coils simultaneously but at a low current level.
In full-step mode, the motor rotates a full-step angle, which results in simple and straightforward movement. On the other hand, in half-step mode, the motor rotates half the step angle for every pulse which results in double the number of steps per rotation.
Full-step mode offers high output torque as compared to half-step mode due to energising one coil in each phase at a time. At the same time, half-step mode offers slightly lower torque than full-step mode due to the double number of steps per revolution.
Implementation and control of full-step mode are easy due to energising one coil at a time, while controlling half-step mode is slightly difficult due to the alternate sequence of coil activation.
In full-step mode, the application can experience vibration and noise during operation due to a large number of steps, while in half-step mode, the application experiences low vibration and noise and smooth operation.
Half-step mode vs Micro-stepping mode
In half-step mode, each full step is subdivided into two small steps by energising coils alternatively and then energising two coils simultaneously at a low current level. While in micro-stepping mode, each full step is divided into much smaller steps by varying the current level into the coil.
In half-step mode, the motor moves half the step angle for each pulse, resulting in double the number of steps per revolution and less smooth operation. On the other hand, in micro-stepping mode, the motor breaks each step into much smaller steps, resulting in smooth operation and precise movement of the motor.
Half-step mode offers low torque as compared to micro-stepping mode due to the double number of steps per revolution. On the other hand, the micro-stepping mode maintains good torque to some level and then starts to reduce.
Implementing half-step mode is less complex than micro-stepping mode due to the alternate sequence of energising the coils. While micro-stepping mode is more complex, as it requires control electronics and algorithms. However, it provides the smoothest operation among all the modes.
Half-step mode results in vibration and noise as compared to micro-stepping mode due to small steps. While micro-stepping mode offers low vibration and noise, and results in smooth operation.
Full-step mode vs Micro-stepping mode
In full-step mode, each step corresponds to the activation of a single coil at a time, resulting in the full-step rotation of the motor. In micro-stepping, each full step is divided into much smaller steps by varying current levels into coils.
In full-step mode, the motor moves into full-step angle resulting in simple and direct movement. On the other hand, in micro-stepping mode, the motor moves at a specific angle with numerous micro steps, resulting in smooth operation and continuous movement.
Full-step mode offers high output torque as compared to micro-stepping mode, as one coil is energised at a time in phase. On the other hand, micro-stepping mode offers good output torque to some extent due to micro-steps, then starts to reduce.
Implementing and controlling the full-step mode is easier as compared to the micro-stepping mode due to the simple and direct movement of the motor. While in micro-stepping mode, the implementation and control are complex as they require control electronics and algorithms.
In full-step mode, the application experiences vibration and noise due to a large number of steps. While in micro-stepping mode, the application experiences low vibration and noise during the operation, resulting in smooth operation.
How to choose the right step mode for the stepper motor
Stepping modes play an important role in PM stepper motors and hybrid stepper motors. The Stepping mode determines the sequence and sizes of steps. The stepper motor can operate at different stepping modes such as full-step mode, half-step mode, and micro-stepping mode.
This stepping mode allows easy control over the motor. Sending an electric pulse in a sequence to specific coils at a specific time helps the motor to move in a controlled manner. This control allows precise positioning and accurate control over motor movement and makes stepper motors and hybrid stepper motors suitable for various types of applications.
Consider the following factors while selecting the step mode for the stepper motor
-
Precision Requirement
Precision requirement refers to the level of accuracy needed to control a stepper motor. Different applications demand different levels of precision. For example, CNC machines and 3D printers require high precision and accuracy for operation.
Full-step mode might offer reliability and simple movement but lacks precision due to large steps. On the other hand, micro-stepping mode provides high precision and reliability due to its micro-steps. Therefore selecting the right stepping mode is essential to meet the precision requirement of an application.
-
Application Compatibility
Application compatibility refers to the mechanical and operational requirements of an application. Different applications have different requirements regarding speed, torque, and precision. Selecting the right stepping mode directly impacts the performance of an application.
Some applications require high precision and smooth movement such as CNC machines. Therefore micro-stepping mode is suitable for such application as it offers high precision with its micro-steps.
While some applications require less precision and simple movement such as conveyor belts, therefore full-step mode is suitable for such applications as it offers less precision and simple movement due to its large steps. Choosing the right step mode with the help of application compatibility helps achieve the desired level of precision and control.
-
Torque Requirement
Torque requirement refers to the rotational force required by a motor to help an application perform a specific task. Stepper motors and hybrid stepper motors produce different amounts of torque based on their design and stepping modes. For instance, full-step mode offers high torque at low speed and is suitable for applications that demand high torque.
On the other hand, micro-stepping mode offers high torque to some extent and starts to reduce. It is suitable for applications that require torque at a constant rate. Therefore deciding the step mode based on torque requirement helps to perform specific tasks where accurate control is required.
-
Speed and Dynamics
Speed and dynamics refer to the responsiveness of the stepper motor for different operations. The choice of stepping mode plays an important role in maintaining a balance between speed and dynamics. Full-step mode provides higher torque but limits the speed of the motor to some level.
Half-step mode provides a perfect balance between the speed and dynamic of the motor. Micro-stepping mode offers low torque at high speed to provide highly precise movement. Therefore selecting the right step mode while considering the speed and dynamics of the motor is important for an application to perform optimally
Therefore selecting the right step mode for the stepper motor with the help of the above factors is important as it directly impacts the performance of the motor and the efficiency of applications.
Our stepper motors and hybrid stepper motors are designed with different stepping modes to provide the perfect balance between the speed and torque of the motor for precise and accurate movement of application. If you also want accurate movement of your application for a smooth manufacturing process. Explore our wide range of stepper motors and hybrid stepper motors with their different step angles. We provide customized stepper motors and hybrid stepper motors along with different types of gearboxes as per customer's needs.