Pulse Width Modulation (PWM) Controls in BLDC Motor
Pulse Width Modulation (PWM) is a technique for controlling the speed of a BLDC motor. It adjusts the voltage supplied to the motor's winding to control the speed and torque of the BLDC Motor. It is a valuable method because it allows precise speed control of BLDC motors with minimum power loss.
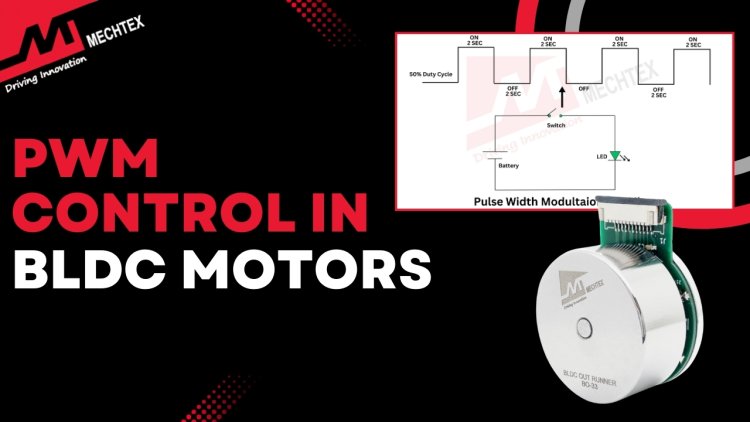
A BLDC motor is an electric motor that uses direct current to operate by using the electronic commutation method. Unlike traditional DC motors, which use brushes, BLDC motors rely on the rotor with a permanent magnet and stator with coils. When DC voltage is supplied to the BLDC motor, it energises the stator winding in a specific sequence and creates a magnetic field. The rotor reacts with the magnetic field and starts to rotate.
The absence of brushes eliminates friction losses and makes BLDC motors more efficient, durable and reliable. However, these motors require specialised methods to control their speed and make them highly efficient and ideal for precision applications.
Pulse Width Modulation (PWM) is one of the most specialised methods used to control the speed of a BLDC motor. In this blog, we’ll explore how Pulse Width Modulation (PWM) works, its role in controlling BLDC motor speed, and the advantages and limitations of this control method.
What is Pulse Width Modulation (PWM)?
Pulse Width Modulation (PWM) is a technique used to control the speed of the BLDC motor by varying the voltage supplied to the motor. In the BLDC motor, the PWM technique adjusts the width of voltage pulses sent to the motor winding. By changing the pulse widths, PWM controls the average voltage and therefore the speed and torque of the BLDC motor.
Watch the YouTube video by "Simply Electronics" to about Pulse Width Modulation (PWM) Control in BLDC Motor.
PWM works with an electronic speed controller (ESC) which rapidly switches the voltage supplied to the BLDC motor windings. When the pulse width is long, the motor receives high voltage and increases its speed. Conversely, when the pulse width is shorter, the BLDC motor receives low voltage and slows down the speed of the motor. The PWM technique efficiently controls the speed of the brushless motor and makes it more energy-efficient.
The PWM technique in brushless DC motors is a valuable technique as it allows precise speed control with minimum power loss. It also enhances the BLDC motor’s responsiveness and stability and makes it ideal for applications requiring variable speeds and efficiency, such as in drones, electric vehicles, and robotics.
Working Principle of Pulse Width Modulation (PWM)
The PWM technique controls the voltage supplied to the BLDC motor windings by switching the motor’s power supply at a high frequency. Here’s a breakdown of how the PWM technique works to control the speed of the BLDC motor:
- Duty Cycle Control
The duty cycle in PWM for BLDC motors is the percentage of time the motor receives power in each cycle. The higher duty cycle means the motor winding gets more voltage which increases the speed of the motor.
Conversely, a low-duty cycle means the BLDC motor winding gets low voltage which reduces the speed of the motor. By adjusting the duty cycle, we control the amount of effective voltage supplied to the motor.
- Torque and Speed Adjustment
As the duty cycle increases, the average voltage supplied to the BLDC motor also increases which increases the current in windings. This results in greater torque which results in the high speed of the motor. PWM allows for fine-tuning of speed without significant energy loss, making it efficient compared to linear regulation methods.
- Efficient Speed Control
The PWM technique helps in the smooth operation of the BLDC motor by delivering continuous pulses which blend into a steady voltage for the windings of the motor due to its inductive characteristic. This method results in efficient and effective speed control with minimal power dissipation.
How PWM Achieves Speed Control in BLDC Motors
Pulse Width Modulation (PWM) plays a crucial role in controlling the speed of Brushless DC (BLDC) motors by adjusting the voltage delivered to the motor windings, ultimately influencing the rotor speed. Here's how PWM achieves speed control in BLDC motors:
- Starting and Acceleration
During the setup, the PWM duty cycle is set to a lower level, by providing an initial current to the BLDC motor winding. As the BLDC motor gains speed, the duty cycle gradually increases to raise the voltage and reach the desired speed.
- Maintaining Constant Speed
Once the BLDC motor reaches the desired speed, the controller adjusts the duty cycle to maintain the speed despite load variations. Closed-loop systems with feedback sensors (hall sensors) are also used for accurate speed control allowing the PWM technique to make adjustments based on real-time data.
- Deceleration and Stopping
For deceleration, the duty cycle is reduced which results in decreasing voltage supplied to the BLDC motor. For an immediate stop, the duty cycle is set to zero, cutting off power to the motor windings.
Benefits of Using PWM for Speed Control in BLDC Motors
Pulse Width Modulation (PWM) offers significant advantages for controlling speed in Brushless DC (BLDC) motors, enhancing both performance and efficiency. Here are the key benefits:
- Precise Speed Control
The PWM technique allows for accurate control over the speed of the BLDC Motor by adjusting the duty cycle or percentage of the time signal. This precision helps maintain constant speed and makes it ideal for applications that require precision.
- Improved Efficiency
By rapidly switching the voltage into the motor winding, the PWM technique minimises energy losses. This efficient control results in less heat generation and consequently reduces the need for additional cooling.
- Reduced Power Consumption
PWM's ability to modulate voltage into the BLDC motor winding ensures that the motor consumes only the necessary power and leads to low power consumption and long battery life.
- Extended LifeSpan
Controlled and efficient speed variation of BLDC motor using PWM technique reduces wear and tear on components and extends motor’s lifespan. This technique also reduces mechanical stress.
- Low Noise and Smooth Operation
The PWM technique provides smooth adjustment to the BLDC motor’s speed which results in low noise and vibration and enhances user experience.
Therefore, the PWM technique remains a popular choice in BLDC motor control due to these benefits, making it ideal for applications that demand precision and energy efficiency.
Conclusion
PWM has proven to be an effective, energy-efficient, and precise method for controlling the speed of BLDC motors. By adjusting the duty cycle, PWM enables accurate voltage control, allowing for smooth acceleration, deceleration, and speed stability across various applications.
Whether in drones, robotics, or electric vehicles, PWM remains a cornerstone of BLDC motor control, providing the flexibility and control needed in modern motor-driven systems. With improvements in efficiency and the emergence of high-performance transistor materials, PWM is set to play an even more significant role in the future of BLDC motor applications.