4 Potent Damping Solutions for Hunting in Synchronous Motor
Damping refers to methods used to reduce Hunting, the oscillation or vibration in a synchronous motor, to stabilise its operation. It improves the performance of the motor and increases its lifespan.
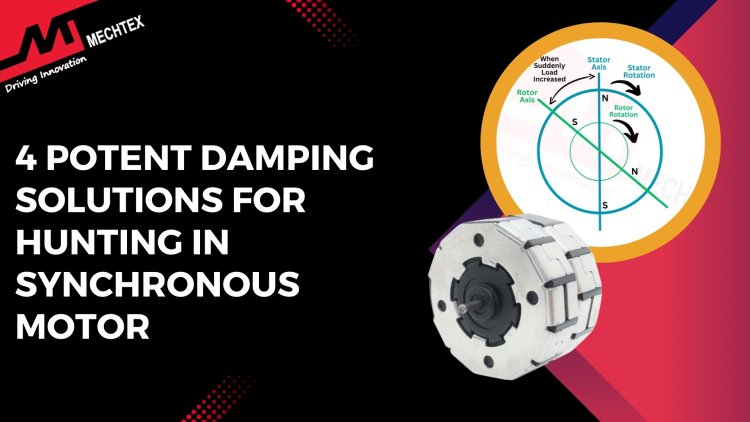
A Synchronous motor is a type of AC motor that operates at constant speed which is synchronised with the frequency of current supplied. Unlike induction motors, which experience slip, synchronous motors do not experience a slip and are known for their efficiency and power factor correction capabilities. This makes synchronous motors ideal for various industrial applications where precise speed control is important.
However, like any other electric motor, synchronous motors also affect certain dynamic issues that affect their overall performance. One such issue is hunting, which disrupts synchronous motors' stability and reduces efficiency. In this blog, we will explore what hunting is, its causes, and how damping mitigates the effects of it.
What is Hunting in Synchronous Motor?
Hunting in synchronous motors refers to the oscillatory behaviour of the rotor around its steady state or synchronous position. When a synchronous motor experiences a sudden disturbance, such as change in load, voltage fluctuation and others. The rotor does not settle immediately into its new condition. Instead, it oscillates back and forth around the synchronous speed before stabilising. This phenomenon is called "hunting in synchronous motor".
The root of hunting lies in the motor's inability to match the electromagnetic torque with altered torque. The rotor speed deviates from synchronism and causes fluctuations in torque and rotor position. These oscillations are not immediate but periodic, and can be sustained or dampened depending on system design.
'
Hunting in synchronous motor affects its performance and can lead to system instability if not properly addressed. To mitigate this, synchronous motors are equipped with damper windings which embedded in the rotor poles. These act similarly to the squirrel cage of an induction motor by providing damping torque through induced currents that counteract the rotor oscillations.
Proper system design, adequate damping, and controlled excitation ensure hunting in synchronous motor can be minimised or eliminated. Maintaining synchronism is essential in applications where stable operation is critical, such as in power generation and high-precision industrial drives.
Also Read
Causes of Hunting in Synchronous Motor
Hunting in synchronous motors can occur due to various factors that lead to oscillation of rotor, speed, and position. The primary causes of hunting in synchronous motors include:
- Sudden Load Changes
When there is a rapid increase or decrease in the mechanical load on a synchronous motor it causes an unbalanced change in torque demand which disrupts the equilibrium between the electromagnetic torque and load torque and leads to oscillations in the rotor.
- Fluctuation in Supply Voltage
Variation in supply voltage leads to changes in the magnetic field strength of the synchronous motor and affects the synchronisation between the stator and rotor’s magnetic field. The sudden change in voltage leads to a temporary phase shift and causes oscillation in the rotor.
- Variation in Frequency
Changes in the frequency of supply can change the constant speed of the synchronous motor. If the rotor’s speed cannot adjust with the change in frequency, it can result in hunting as the rotor tries to re-synchronise with the stator’s magnetic field and starts oscillating.
- Mechanical Resonance
Every synchronous motor has a natural frequency of oscillation. When the frequency of changes in load or external disturbance aligns with the natural frequency, mechanical resonance occurs. This resonance increases the oscillation and makes the hunting effect more effective.
Damping - A Solution to Hunting
Damping in synchronous motor refers to the mitigation of oscillations that occur due to the disturbances experienced by the rotor of synchronous motor. These oscillations are also referred to as "hunting" or "hunting in synchronous motor". It causes the rotor to swing around its steady-state before returning to its synchronous speed. Damping ensures that hunting or oscillation can be minimised and enables synchronous motor to operate at its synchronous speed.
When synchronous motor operates under varying load conditions, the electromagnetic torque mismatch with the mechanical load torque. This mismatch causes the rotor to fluctuate around its synchronous speed. Without damping, these fluctuations can persist and lead to system inefficiencies.
Damping is used to resist these oscillations (hunting) by introducing force which opposes the rotor's deviation from its equilibrium position. As a result, the oscillatory (hunting) movements decay over time and restore the smooth and stable operation of the synchronous motor. Damping not only enhances the operational stability of the synchronous motor but also protects the motor from mechanical integrity.
In applications where synchronous motors are used for precision and reliability—such as power generation, HVAC systems, or industrial automation—damping plays a vital role in ensuring performance consistency and long-term durability.
Methods for Damping in Synchronous Motor
Damping in a synchronous motor refers to methods used to reduce the oscillation or vibration in a synchronous motor rotor that occurs due to disturbances like sudden load changes, supply voltage fluctuation and many more.
This method plays a crucial role in stabilising the synchronous motor’s operation by absorbing the energy of oscillation and preventing hunting. Let’s explore the key methods for damping in synchronous motors:
- Damping Winding
One of the most common methods of counter-hunting in synchronous motors is damping winding or damper bars. These bars are made up of copper or aluminium embedded in the pole which faces the rotor and forms a squirrel cage structure.
When the rotor starts oscillating, the relative motion between the damper bars and the rotating magnetic field induces current. This current produces a magnetic field and opposes the rotor’s oscillation. This method is effective during the start of the synchronous motor as rotor speed needs to align with synchronous speed and help during load changes.
- Automatic Voltage Regulation
An automatic voltage regulation (AVR) helps to maintain a constant voltage across all the terminals of a synchronous motor. By stabilising the voltage supply, it minimises the sudden changes in loads that lead to hunting.
The AVR adjusts the field current in response to changes in load or input voltage and ensures that synchronous motor excitation remains at optimal level. This method helps in reducing oscillation and stabilising the synchronous motor’s operation.
- Load Management Systems
Load management systems control or remove the load from the synchronous motor which helps to avoid sudden changes that cause hunting. Gradual adjustment in load gives the rotor enough time to adapt and reduce the oscillation.
For example, a soft starter can be used to gradually ramp up the load and prevent the motor from experiencing a sudden torque imbalance.
- Tuning of Excitation System
Proper tuning of the excitation system can reduce hunting. It involves setting the parameters of the excitation system such as gain and response time to optimise the performance of the synchronous motor.
Advanced excitation systems include feedback loops that monitor the rotor’s position and adjust the excitation current in real time to improve the synchronous motor’s ability.
Also Read
The Role of Excitation Systems in Synchronous Motors
Effective damping ensures smooth and stable operation by minimising the effect and duration of oscillation. It also reduces the risk of mechanical stress and wear and tear on synchronous motor components which increases the motor’s lifespan. Without adequate damping, a synchronous motor can experience prolonged hunting and lead to inefficient operation and potential damages.
Calculating the Damping Factor
The effectiveness of damping can be quantified using the damping factor (ζ). The damping factor is a measure of how oscillations decay over time. It is calculated based on the system’s natural frequency (ωn) and the damping coefficient (c):
ζ = c/2√mk
Where,
c = damping coefficient (dependent on the damping method)
m = mass of the rotor
k = stiffness of the system
A higher damping factor indicates better suppression of oscillations, while a lower damping factor means that oscillations will persist for a longer time.
Practical Considerations for Damping System
When designing a damping system for a synchronous motor, engineers must consider the following factors:
- Type of Applications
The nature of the application significantly influences the required level of damping mechanism in a synchronous motor. Commonly needed for applications where small speed variations due to hunting lead to performance issues. In these cases, robust damping systems are necessary to maintain tight control over rotor position and speed.
Conversely, in applications where slight speed variation is less critical. In these cases, the damping system requirements are less stringent. A simple and cost-effective damping system is sufficient for these applications.
- Cost vs Complexity
Integrating an effective damping system increases both the cost and complexity of synchronous motors. Using damper winding, or Automatic Voltage Regulation introduces additional electronic components and programming efforts, which can raise overall system costs.
One must consider these factors against the importance of maintaining the stability of the AC motor’s operation. In applications, where instability in operation can cause operational disruption or safety issues, a highly advanced damping system is required.
However, for applications where occasional hunting in synchronous motors poses minimal risk, a simpler and less expensive damping system is required.
- System Inertia
Inertia is the resistance of the rotor and the connected system to change its speed. Higher inertia makes synchronous motors more resistant to changes in speed and helps the damping system to maintain speed and smooth operation of synchronous motors. It is beneficial for applications that require stability.
However, higher inertia requires more energy for acceleration and deceleration, which results in slower responses to load changes and inputs. This can be a drawback for applications that require quick response. Therefore, engineers must balance the inertia with a damping system for smooth and stable operation of synchronous motors.
Conclusion
Hunting in synchronous motors, though a common issue, can be effectively managed through a combination of damping techniques and control systems. From the use of damping windings to advanced voltage regulation and excitation tuning, each approach plays a role in ensuring smooth and stable operation. Understanding the causes and implementing appropriate solutions is essential for maximising the performance and longevity of synchronous motors in industrial applications.
By addressing hunting effectively, synchronous motors can deliver their inherent advantages - constant speed, high efficiency, and precise control - without being hindered by dynamic instability. Proper design, monitoring, and maintenance are key to harnessing the full potential of these versatile machines.