Understanding the Torque of Synchronous Motor
Torque is the force that rotates the motor’s rotor and drives the mechanical load. It is an important aspect of the synchronous motor as it helps the motor maintain its alignment of magnetic fields and ensures it runs at constant speed which makes it ideal for industrial applications.
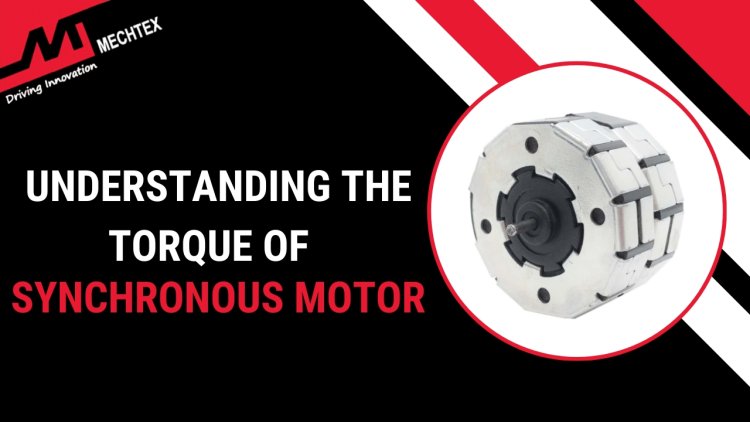
Torque is an important aspect of every motor’s performance, especially in synchronous motors, which are widely used in various industrial applications due to their precision and efficiency.
It maintains the alignment of magnetic fields and ensures the motor runs at a constant, synchronised speed. It prevents the motor from losing step or slipping under load.
To fully utilise the function and capacity of synchronous motors, we must understand the concept of torque and its implications. In this blog, we will delve into the concept of torque, the torque characteristic of synchronous motors, and how it affects the performance of synchronous motors.
What is a Torque?
In simple terms, torque is a rotational force applied to an object that causes it to rotate. In the context of miniature motors, torque is the force that rotates the motor’s rotor and drives the mechanical load. It is typically measured in Newton metres (Nm) and mathematically expressed as
Torque (T) = Force (F) × Radius (®)
The above formula indicates torque is the product of the force applied and the distance of the point of rotation. The greater the force or longer the distance from the point, the higher the torque will be generated.
Watch the YouTube Video posted by "The Engineering Mindset" for a better understanding of torque.
Torque in Synchronous Motor
Synchronous motors generate torque through the interaction between the magnetic field of the stator and the magnetic field of the rotor. Unlike induction motors, where the rotor slips slightly due to friction, synchronous motors operate at synchronous speed. This speed is directly related to the frequency of the electrical supply and the number of poles.
The torque in the synchronous motor is dependent upon torque angle. The torque angle of a synchronous motor is the angle between the stator's magnetic field and the rotor’s magnetic field.
The torque angle plays an important role in determining the amount of torque produced. When a synchronous motor is running, the torque angle is small; it means the synchronous motor is producing sufficient torque to drive the load.
Torque Equation of Synchronous Motor
The torque equation of synchronous is fundamental for understanding how synchronous motor electrical energy is converted into mechanical energy. The torque generated by a synchronous motor can be expressed by the following equation:
T= 3⋅Vs⋅Ef/ ωs ⋅Xs ⋅sin(δ)
Where
- T = Torque produced by the motor (Newton-meters, Nm)
- Stator Voltage (Vs): This is the voltage applied to the stator winding.
- Induced EMF (Ef): The voltage induced in the stator due to the rotating magnetic field created by the rotor.
- Synchronous Speed (ωs): The speed at which the motor's magnetic field rotates, which is constant for a given frequency.
- Synchronous Reactance (Xs): The opposition offered by the inductance of the motor to the flow of alternating current.
- Load Angle (δ): The phase difference between the stator voltage and the induced EMF. This angle plays a critical role in determining the torque.
The above graph shows torque is directly proportional to the sine of the load angle {sin(δ)} This means that the torque increases with the load angle until δ reaches 90 degrees. Beyond this point, the torque decreases.
The maximum torque occurs when δ =90∘ known as the pull-out torque. This equation is vital for analysing the performance of synchronous motors under various load conditions.
Pull Out Torque in Synchronous Motor
Pull-out torque is an important parameter in the working of a synchronous motor. It represents the maximum amount of torque a synchronous motor can handle while maintaining its synchronous speed. If the load exceeds the pull-out torque, the synchronous motor will lose its synchronism. It means the rotor will no longer rotate at synchronous speed leading to a sudden stop or decrease in the performance of the synchronous motor.
The above graph shows the Pull-Out Torque Curve of a synchronous motor. The torque increases as the rotor angle increases, reaching a maximum (pull-out torque) at 90 degrees, after which the torque sharply drops.
This curve visually represents the sinusoidal relationship between the rotor angle and torque, with the peak indicating the maximum torque the motor can sustain before losing synchronism.
This characteristic of a synchronous motor is important in applications where the motor is subject to sudden changes in load. One must ensure that the synchronous motor’s pull-out torque is sufficient to handle such variations without losing synchronism. The pull-out torque is typically two to three times the rated torque of the motor, providing a safety margin to handle unexpected loads.
Starting Torque of Synchronous Motor
One of the common challenges with synchronous motors is the lack of starting torque. At no load condition, the rotor of the synchronous motor is not yet aligned with the rotating magnetic field of the stator. It means there is no torque produced. Unlike induction motors that can produce torque from zero, synchronous motors require external means to start. There are several methods to start a synchronous motor. Some methods are:
- Using an Auxiliary Motor
An auxiliary motor is used to bring the synchronous motor up to its synchronous speed. It is the point at which the rotor can lock itself with the synchronism of the stator’s magnetic field.
- Damper Windings
Some synchronous consists of damper windings which produce starting torque by inducing currents in the rotor. Once the motor reaches the synchronous speed, the damper winding will reduce its effect, and the motor start operating at synchronous speed.
- VFD (Variable Frequency Drive)
A Variable Frequency Drive (VFD) is an electronic device that controls the speed and torque of synchronous motors by adjusting the input frequency and voltage. It improves energy efficiency and provides precise motor control in various applications.
VFD gradually increases the frequency of the supply voltage and allows the synchronous motor to start smoothly and reach its synchronous speed without losing its synchronism.
Also Read
Why Synchronous Motor is not Self-Starting
Conclusion
Synchronous motors are essential in applications requiring precise and consistent speed control. Understanding the torque characteristics of these motors, including the torque equation, pull-out torque, and starting torque, is vital for their efficient and reliable operation.
By considering these factors, one can select and design synchronous motor systems that meet the specific demands of various industrial processes, ensuring optimal performance and longevity.