Types of NEMA Motor Enclosure : A Comprehensive Guide
NEMA Motor Enclosure refers to the standardised housing for electric motors, as defined by the National Electrical Manufacturers Association (NEMA). It determines the motor's ability to operate reliably in various industrial and commercial environments.
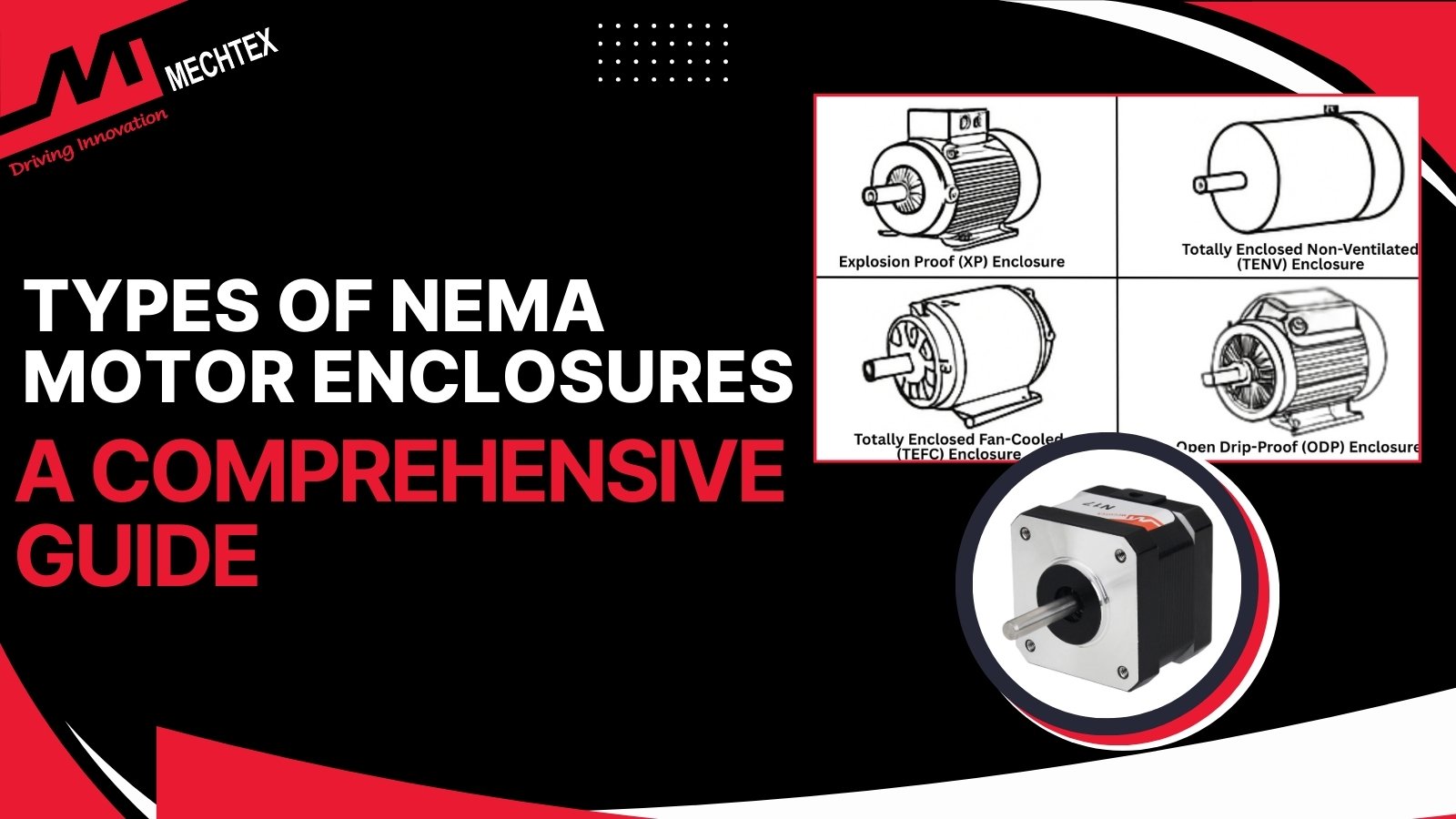
Electric motors are essential components in countless industrial and commercial applications. Choosing the right motor involves more than just selecting voltage, power, and speed. One of the most critical aspects is the enclosure type, which directly impacts a motor's performance, safety, and longevity, especially in varying environmental conditions.
The National Electrical Manufacturers Association (NEMA) has defined various standard motor enclosure types. Each type is suited for different environmental conditions, helping users make informed decisions when selecting motors for specific applications.
In this blog, we’ll explore the most common NEMA motor enclosure types, their design features, applications, and the environments they are best suited for.
What is NEMA Motor Enclosure
NEMA Motor Enclosure refers to the standardised housing for electric motors, as defined by the National Electrical Manufacturers Association (NEMA). These enclosures play a critical role in protecting the motor’s internal components from environmental factors such as dust, moisture, chemicals, and physical damage, while also ensuring user safety.
The design and construction of a NEMA enclosure determine the motor's ability to operate reliably in various industrial and commercial environments. NEMA provides a classification system with specific Type numbers that define the level of protection offered, such as resistance to corrosion, ingress of solid objects, and exposure to water or oil. This classification ensures consistency across manufacturers, making it easier for engineers and technicians to select appropriate motors for specific applications.
Common Types of NEMA Enclosures:
- Open Drip Proof (ODP)
- Totally Enclosed Fan Cooled (TEFC)
- Totally Enclosed Non-Ventilated (TENV)
- Totally Enclosed Air Over (TEAO)
- Explosion Proof (XP)
Industries such as manufacturing, HVAC, agriculture, and oil & gas rely heavily on correctly specified NEMA enclosures to prevent operational failures and meet safety regulations. Understanding NEMA enclosure standards is essential for ensuring that the motor performs optimally in its operating environment, especially where conditions are harsh, wet, or hazardous.
Types of NEMA Motor Enclosures
1. Open Drip-Proof (ODP) NEMA Enclosure
An Open Drip-Proof (ODP) NEMA enclosure is a motor housing designed to allow air flow for cooling while protecting against water and contaminants falling vertically or at a slight angle (up to 15°). It is typically used in clean, dry environments where minimal exposure to moisture or debris is expected.
Key Features:
- Ventilation: Open slots in the frame allow ambient air to cool internal components.
- Drip Protection: Constructed to prevent water droplets from entering the motor from above.
- Cost-Effective: Less expensive than Totally Enclosed motors due to simpler design.
- Lightweight: Fewer components result in reduced weight and ease of handling.
Applications:
- HVAC systems
- Pumps and blowers in indoor environments
- Industrial machinery is located in dry, dust-free areas
2. Totally Enclosed Fan-Cooled (TEFC) NEMA Enclosure
A Totally Enclosed Fan-Cooled (TEFC) NEMA enclosure is a motor housing that prevents external air, dust, and moisture from entering the motor while using an external fan to cool it. The motor is completely enclosed, and a shaft-mounted fan blows air over the ribbed frame to dissipate heat. This design ensures durability and protection in demanding environments.
Key Features:
- Sealed Construction: Blocks entry of dust, dirt, and water into the motor.
- External Cooling Fan: A separate fan circulates air over the housing to maintain optimal temperature.
- Ribbed Frame: Increases surface area for effective heat dissipation.
- Durable Design: Suitable for both indoor and outdoor applications, even in harsh conditions.
Applications:
- Pumps and compressors
- Conveyors in industrial plants
- Outdoor HVAC and ventilation systems
- Agricultural and food processing equipment
3. Totally Enclosed Non-Ventilated (TENV) NEMA Enclosure
A Totally Enclosed Non-Ventilated (TENV) NEMA enclosure is a motor housing that prevents the free exchange of air between the inside and outside of the motor. Unlike ventilated designs, TENV enclosures rely solely on surface cooling and are sealed to protect against external contaminants such as dust, dirt, and moisture.
Key Features:
- Sealed Construction: Prevents entry of airborne particles, moisture, and external elements.
- No External Ventilation: Cooling is achieved through the external surface of the motor.
- Quiet Operation: The absence of airflow results in reduced noise during operation.
- Maintenance-Free: Minimal ingress reduces internal contamination and bearing wear.
Applications:
- Food processing environments
- Pharmaceutical equipment
- Cleanrooms and indoor conveyors
- Outdoor applications with protective covers
TENV enclosures are ideal for clean or semi-protected environments where durability and contamination resistance are critical.
4. Totally Enclosed Air Over (TEAO) NEMA Enclosure
A Totally Enclosed Air Over (TEAO) NEMA enclosure is a motor housing designed to be completely sealed from the environment while using externally supplied airflow for cooling. Unlike non-ventilated motors, TEAO motors require an external fan or airflow source, typically from a connected piece of equipment, to dissipate heat through the motor’s surface.
Key Features:
- Totally Enclosed: Prevents dust, dirt, and moisture from entering the motor.
- Air-Over Cooling: Depends on external airflow over the motor’s frame to maintain optimal temperature.
- Durability: Suitable for harsh or moderately dirty environments.
- Robust Design: Often used in applications with fans or blowers providing forced cooling.
Applications:
- Fans, blowers, and compressors
- Conveyor systems with built-in cooling airflow
- Industrial equipment with external cooling sources
TEAO enclosures balance protection and efficient cooling in systems with available airflow.
5. Explosion Proof (XP) NEMA Enclosure
An Explosion Proof (XP or EXPL) NEMA enclosure is engineered to contain any internal explosions without igniting the surrounding atmosphere, making it essential for hazardous environments with flammable gases, vapours, or dust. These enclosures are robustly built to withstand high pressure and prevent sparks or flames from escaping.
Key Features:
- Sealed and Reinforced: Heavy-duty construction with thick walls and secure joints to contain explosions.
- Certified for Hazardous Locations: Complies with stringent safety standards (e.g., NEC, ATEX) for classified areas.
- Flameproof Design: Prevents ignition of external flammable atmospheres by containing internal arcs or sparks.
- Durability: Resistant to corrosion and mechanical damage.
Applications:
- Oil and gas refineries
- Chemical plants
- Grain handling and processing facilities
- Mining operations
XP enclosures provide critical safety for motors operating in explosive atmospheres, ensuring operational integrity and regulatory compliance.
Conclusion
Motor enclosures are more than just casings—they are the first line of defence against environmental threats and operational hazards. Understanding NEMA enclosure types allows engineers, technicians, and facility managers to choose motors that ensure reliability, longevity, and compliance with safety and environmental standards.
Whether it's a dust-free warehouse, a washdown food processing line, or a flammable gas area, there is a NEMA motor enclosure built for the job. Making the right choice not only protects the motor but enhances system performance and reduces total cost of ownership.