Microstepping in Stepper Motor
Microstepping is a technique that divides each full step into smaller steps to increase the resolution and smoothness of the stepper motor. It helps in precise control over the motor’s position, which is essential in applications where accurate positioning is critical.
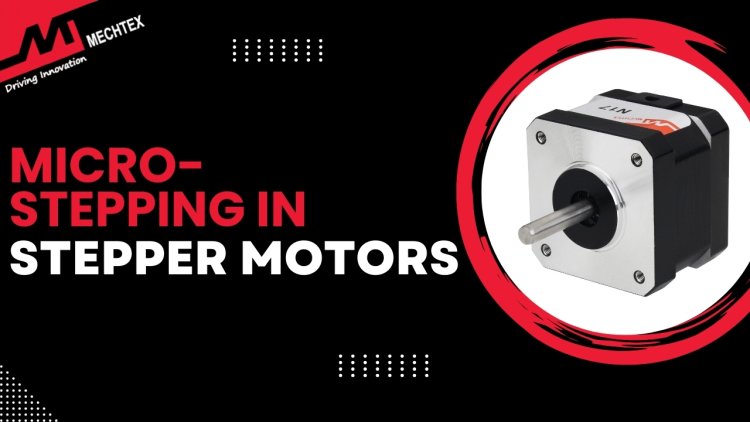
Stepper motors are the fundamental component in various applications requiring precise movement, such as 3D printers, CNC machines, and medical devices. Microstepping is an advanced driving technique that enhances the accuracy, smoothness, and efficiency of the stepper motors. In this blog, we will explore the inner workings of the stepper motor, the concept of micro-stepping and its impact on the performance of the stepper motor.
What is a Stepper Motor?
A Stepper motor is an electromechanical device that converts electrical pulses into discrete mechanical steps. Unlike traditional motors, which rotate continuously, stepper motors rotate at a fixed angle. This angle is also known as “steps” which are based on the number of poles energised within the stepper motor.
Stepper motors work by energising and de-energising coils within the stator in a specific sequence. It allows the rotor to align with the generated magnetic field and rotate at a fixed angle. This energising sequence is referred to as “stepping” and the step angle depends upon the motor design.
For instance, a stepper motor with 200 steps per revolution has a step angle of 1.8° (360°/200). While this precision might be adequate for many tasks, certain applications require finer resolution or smoother motion, which cannot be achieved through standard stepping alone.
The most common types of stepper motors include:
- Permanent Magnet Stepper Motor
PM stepper motor uses a permanent magnet rotor and relies on magnetic attraction for movement.
- Variable Reluctance Stepper Motor
In this stepper motor, the rotor is made up of a soft iron core with no permanent magnet. It relies on magnetic reluctance changes for movement.
- Hybrid Stepper Motor
The hybrid stepper motor combines the quality of both a permanent magnet stepper motor and a variable reluctance stepper motor. It offers fine steps and better precision.
Also Read
What is Microstepping?
Microstepping is a technique used in stepper motors to increase the resolution and smoothness of stepper motor motion by dividing each full step into smaller steps. In traditional stepper motors, the rotor moves in discrete steps, typically 1.8 degrees for a 200-step revolution. However, with micro-stepping each step can be further subdivided into many smaller angles, often reaching 256 microsteps.
Watch the YouTube video by "Zikodrive" to learn more about microstepping in stepper motors
This increased granularity is achieved by controlling the current in the stepper motor’s winding with sinusoidal waveforms, allowing the rotor to align at points between full steps. Microstepping requires sophisticated control electronics, typically a micro-stepping driver which regulates the current flowing through each coil to achieve smooth transitions from one micro-step to the next.
By achieving finer steps, micro-stepping reduces noise and vibration in stepper motors and produces a smooth and quiet operation. Additionally, micro-stepping helps in precise control over the motor’s position, which is essential in applications where accurate positioning is critical.
Working of Microstepping
The working principle of micro-stepping involves dividing each full step of a stepper motor into small steps by carefully controlling the current into the motor’s winding. In traditional stepper motors, each full step is achieved by sequentially energising the windings. However, in micro-stepping a controller adjusts the current in each winding following a sinusoidal pattern, allowing the rotor to stop at intermediate positions between the full steps.
For example, in a two-phase stepper motor, micro-stepping is achieved by varying the current in both windings (A & B) to create the intermediate magnetic field and the rotor aligns with it.
By modulating the current from a series of sinusoidal waveforms, the rotor moves incrementally from one step to another. For instance, if the driver creates 16 intermediate steps between each full step, each micro-step corresponds to 1/16th of the full-step angle, achieving finer movement.
The microstepping driver divides each full step by controlling the amplitude of the current in proportion to the desired micro-step position. This results in smoother motion, reduced resonance, and more accurate control. However, as micro-steps get smaller, the torque available per micro-step also decreases, therefore micro-stepping is often used for improved smoothness rather than maximum torque.
Advantages of Microstepping
Microstepping offers several advantages that enhance the performance and precision of stepper motors:
- Increased Resolution
By dividing full steps into small steps, micro-stepping increases the stepper motor’s positional accuracy. It also enables fine control over its movement to ensure smooth operation. It is particularly valuable in applications such as 3D printing and CNC machining, which require high precision.
- Reduced Vibration
Microstepping smooths out the stepper motor movement by creating smaller and more gradual transitions between the steps. It results in reducing the jerky motion and vibration which is associated with full or half-stepping mode. It leads to a more stable and quieter operation of the stepper motor.
- Improved Smoothness at Low Speed
At low speeds, stepper motors in full step mode can exhibit jerky motion. Microstepping mode experiences a smooth operation by enabling continuous movement without any vibration. It is beneficial in applications such as medical equipment and robotics where smooth operation is essential.
- Greater Torque Control
Microstepping allows for more precise current control in each winding of the stepper motor and helps in optimising the torque output. Though the torque per microstep is lower than in full-step mode, the stepper motor can still achieve efficient torque control at various points.
Conclusion
Microstepping is a powerful technique that extends the capabilities of stepper motors by providing finer control, smoother operation, and improved performance at low speeds.
By subdividing each full step, micro-stepping allows stepper motors to operate in a broader range of applications, from precise CNC machines to quiet medical devices.
While it has some limitations in torque output, the advantages of microstepping make it indispensable in applications that demand high precision and low vibration. Properly implementing microstepping can lead to significant improvements in the quality, efficiency, and reliability of stepper motors. This makes it a vital tool in modern motion control solutions.