Impact of Voltage and Current on Stepper Motor Performance
Voltage primarily impacts speed and torque at high step rates, while current directly affects torque and thermal characteristics. Voltage and current are critical factors influencing stepper motor performance.
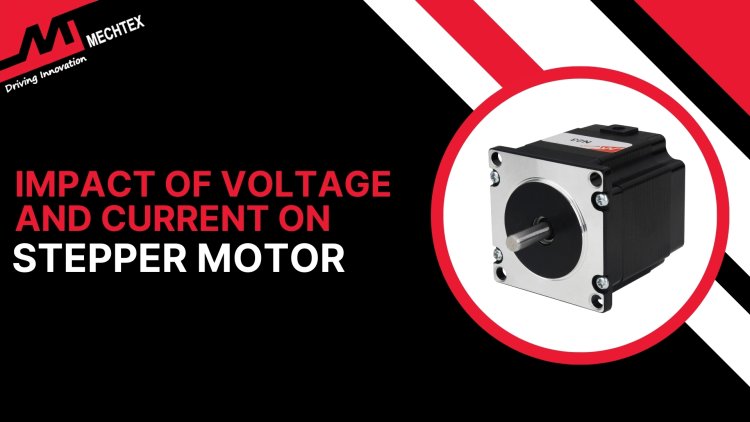
Stepper motors are widely used in applications that require precise control such as robotics, CNC machines, and 3D printers. Voltage and current play crucial roles in determining their performance and influence parameters such as torque, speed and potential accuracy. In this blog, we will delve into the fundamentals of stepper motors, and how voltage and current influence their performance in various applications.
What is Stepper Motor
The Stepper motor is an electromechanical device that converts electrical pulses into mechanical motion. Unlike other motors which rotate continuously, stepper motors move in discrete steps, which makes them ideal for applications that require precise positioning and accuracy.
The key components of the stepper motor include the stator and rotor. The stator is the stationary part of the motor and contains winding, which is energised in sequence to create a rotating magnetic field. The rotor is the rotating part of the motor and contains permanent magnets that align with the stator’s magnetic field and rotate.
Watch the YouTube Video by "Sabins Civil Engineering" to know more about stepper motors.
The working principle of the stepper motor is based on electromagnetic interactions. When current flows through the windings, the rotating magnetic field generates and causes the rotor to align with the magnetic field and rotate. Sequential energisation of the stator winding helps the rotor to move in a fixed angular step.
Stepper motors are widely used in CNC machines, 3D printers, robotics, medical devices, and camera systems due to their precise control and versatility.
Also Read
Understanding the Hybrid Stepper Motor
Voltage and Stepper Motor Performance
In a stepper motor, voltage is the electrical potential applied to its windings to generate the magnetic field and enable the rotor’s precise movement. Voltage directly affects the stepper motor’s performance including speed and torque.
The voltage requirement of the stepper motor depends upon its coil resistance and desired current. Voltage can be calculated using the following formula:
V = I x R
Where,
V = Voltage
I = Current
R = Current Resistance
However, Due to the inductive nature of the stepper motor’s coil, higher voltage is applied to these windings to achieve high torque at high speed.
Impacts of Voltage on Stepper Motor
- Impact on Speed
The speed of the stepper motor is highly dependent on the voltage applied to its windings. It is because of the rise in current in stepper motors winding governed by the inductance and determines how quickly stepper motors can respond to the pulses.
-
- Higher Voltage: An increase in voltage enables a faster rise in current in the windings due to lower inductance lag. This allows the stepper motor to achieve high step rates to improve operational speed.
-
- Lower Voltage: A lower voltage results in lower current build-up which limits the maximum step rate and reduces the operational speed of the stepper motor.
- Impact on Torque
The torque of a stepper motor at high speed is significantly influenced by the voltage applied to its windings. The ability of the stepper motor to maintain sufficient at higher step rates determines the availability of higher torque.
-
- Higher Voltage: Higher voltage enables a faster rise in current and reduces inductive lag to maintain high torque at high speed. This benefits applications like conveyor systems, and robotics arms that require high-speed operation at sufficient torque.
-
- Lower Voltage: Lower voltage causes slower current build-up which results in the drop of torque at high speed. It is beneficial for applications such as medical devices that require lower torque operations.
- Risk of Overvoltage
Overvoltage in stepper motors poses significant risks including overheating and potential damage to the stepper motors winding and driver circuits. Excessive voltage increases the current flow which raises the stepper motor’s temperature and reduces its lifespan. It can also cause erratic motor behaviour or permanent driver failure.
- Impact on Efficiency
Higher voltage enhances stepper motors efficiency by reducing inductive lags and allowing current to establish faster and improve response time. It is beneficial for high-speed or rapid acceleration applications.
Current and Stepper Motor Performance
In a stepper motor, current is the flow of electric charge through the windings to create a magnetic field that drives the rotor. It is specified by its rated current which is the maximum current each winding can handle safely. Stepper drivers regulate the current supplied to enhance its efficiency. Current can be calculated using the following formula:
I = T/Kt
Where,
I = Current
T = Load torque
Kt = Constant torque
Impacts of Current on Stepper Motor
- Impact on Torque
-
- Higher Current: An increase in current strengthens the magnetic field and generates higher torque. It is beneficial in applications that require stepper motors to move heavy loads or resist external loads.
-
- Lower Current: Lower current weakens the magnetic field and generates lower torque. It potentially causes the stepper motor to lose its steps or accuracy under varying load conditions.
- Impact on Speed
At a higher current level, the stepper motor can sustain higher torque across a wide range of speeds. On the other hand, the insufficient current causes a drop in torque as the speed increases which limits the stepper motors performance.
- Precision and Accuracy
Higher current ensures the generation of strong electromagnetic force which aligns between the stator and rotor and improves the positional accuracy of the stepper motor. However, inadequate current causes the stepper motors to skip steps which leads to positioning errors in precise applications.
- Heat Management
Excessive current causes overheating and reduces the stepper motors efficiency and lifespan. It also damages windings and insulation. However, lower current maintains a balance between stepper motors performance and thermal management and avoids overheating.
Interplay Between Voltage and Current in Stepper Motors
Voltage and Current are closely intertwined in the operation of stepper motors and their effective management is critical for optimal performance. Let’s delve deeper into the interplay between the voltage and current:
- Voltage Drives Current
Voltage is the driving force that initiates and sustains current in stepper motors winding. As it operates at a higher speed, the inductance of winding experiences rapid changes in current. This phenomenon is necessary at high voltage to ensure that the current meets the stepper motor requirement, particularly during rapid acceleration or high-speed operation.
- Current Regulation by Drivers
Modern stepper motor drivers employ advanced current regulation techniques and systems. These systems deliver a high voltage to overcome the inductive lagging, to enable rapid current build-up. Once the current rises to the desired level, the driver regulates it to the rated level to ensure high efficiency.
- Impact on Torque and Speed Curves
The interaction of current and voltage directly affects the torque speed curve of the stepper motor. At low speeds, sufficient current ensures high torque. However, as speed increases higher voltage becomes critical to maintain the current level to ensure the stepper motor delivers sufficient torque at varying load conditions.
- Thermal Management
The balance between voltage and current is crucial for thermal management. Excessive voltage or current can generate heat beyond stepper motors thermal limit. Using heat sinks, forced air cooling, or advanced drivers can mitigate these effects and ensure reliable operation.
Also Read
Understanding Torque and Speed Curves of Stepper Motors
Conclusion
Voltage and current are critical factors influencing stepper motor performance. Voltage primarily impacts speed and torque at high step rates, while current directly affects torque and thermal characteristics.
Understanding the interplay between these parameters helps optimise motor performance for specific applications, enhancing efficiency and reliability. By carefully selecting power supplies, configuring drivers, and managing thermal loads, users can maximise the potential of their stepper motors.