How Rotary Encoders Work: A Complete Guide
A rotary encoder is an electromechanical device that converts the angular position or motion of a rotating shaft into digital or analogue signals. It senses the rotation of a shaft and converts it into signals that help control speed, direction, and position in various machines
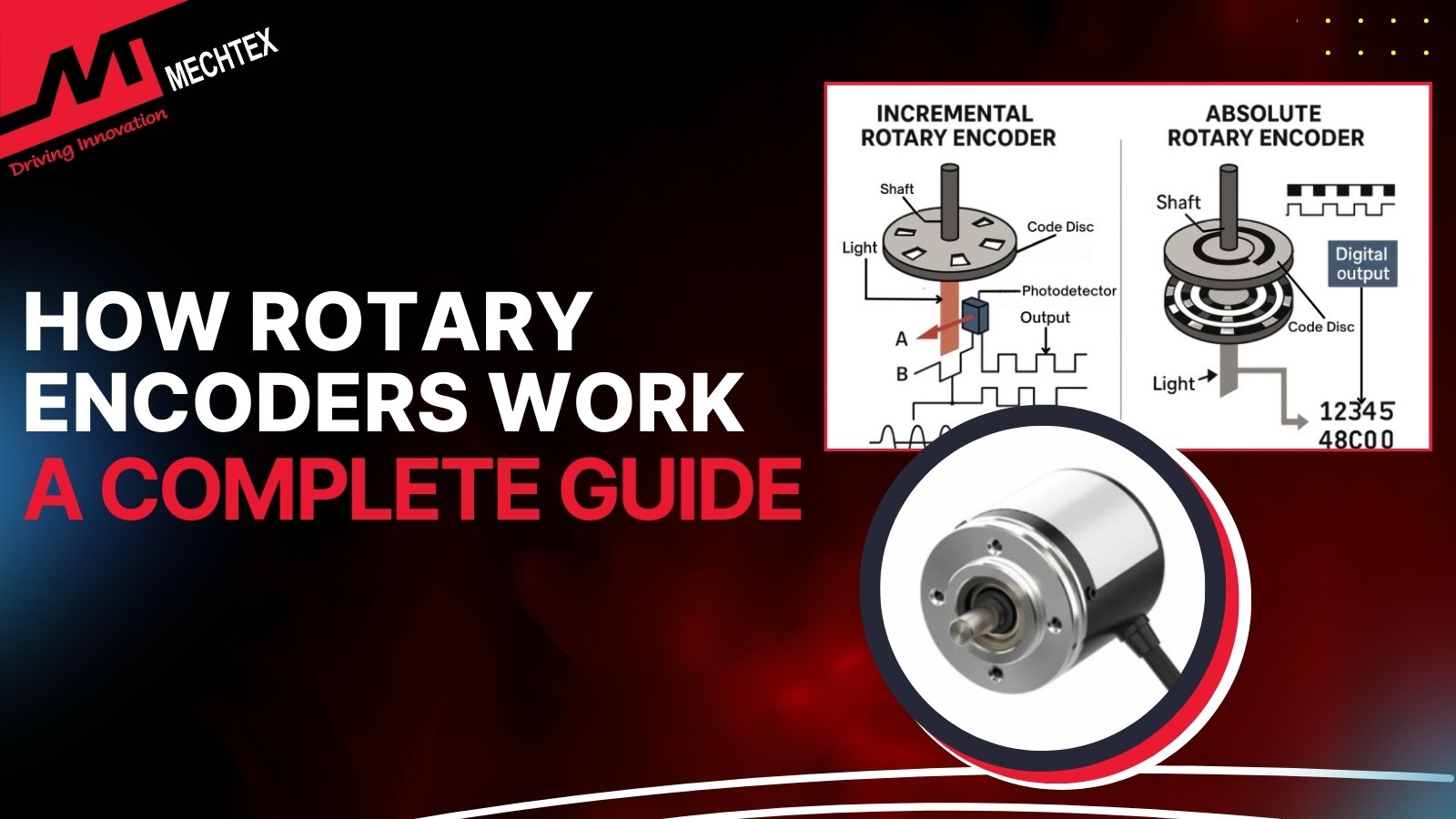
In today’s world of automation, robotics, CNC machines and motion control systems, precision and feedback are crucial. This is where rotary encoders come into play. The rotary encoder converts the angular position or motion of the shaft into an electrical signal that can be read by a control system. They are also referred to as the “eyes” of the motion control system.
In this blog, we will explore what rotary encoders are, their working principle, types and their applications, which help engineers design more accurate and efficient systems.
What is Rotary Encoder?
A rotary encoder is an electromechanical device that converts the angular position or motion of a rotating shaft into digital or analogue signals. It plays a crucial role in systems that require precise control of position, speed and direction.
These encoders enable closed-loop control systems, helping to monitor and adjust the operation in real time. They are also often integrated into the motors to ensure accuracy in speed and position control. Rotary encoders also support direction sensing and provide feedback on the velocity of rotation.
Watch the YouTube video by "JAES Company" to know more about Encoders
The key specifications that determine a rotary encoder’s performance include resolution (number of pulses or positions per revolution), accuracy, response time, and environmental tolerance. Many modern applications rely on magnetic and optical encoders to achieve high resolution and reliability.
Also Read
Internal Construction and Components of a Rotary Encoder
The internal construction of the rotary encoder slightly varies from other types of encoders and depends on its different types. Here is the list of components of rotary encoder:
- Shaft
It is the primary element of the rotary encoder. It is directly connected to the motor and is responsible for transmitting the mechanical rotation to the internal disc.
- Code Disc / Wheel
It is attached to the shaft and usually made up of glass, plastic and metal. In an optical encoder, the disc contains precise slots for positioning, while in a magnetic encoder, it contains alternating magnetic poles.
- LED light source
It is used in an optical rotary encoder to emit a focused beam of light through the code disc. As the disc rotates, the pattern on the disc modulates the light signal.
- Photodetector/Phototransistor Array
It is positioned opposite the light source to sense the interrupted or transmitted light pattern from the rotating disc and convert it into electrical signals.
- Magnetic Sensor
It detects the changes in the magnetic field generated by the rotating magnetic disc, offering a robust solution, especially in dusty or oily environments.
- Signal Processing Circuitry
It interprets the raw signals from the sensor array and amplifies, filters, and processes data into usable output signals such as digital pulses or absolute position codes, ready for feedback systems.
Working of Rotary Encoder
When the motor begins to rotate, the rotary encoder’s shaft, which is mechanically coupled to it, starts rotating. This rotational motion is transferred to an internal disc, which is mounted directly to the encoder shaft. The disc is either optically or magnetically patterned, depending on the type of encoder. A light source, typically an LED, shines through the disc.
As the disc rotates, the interaction between the disc pattern and the sensor generates varying signals. In an optical encoder, photodetector receives the pulses of light or darkness corresponding to the disc pattern. In a magnetic encoder, the magnetic sensor detects changes in the magnetic field caused by spinning the poles.
These detected changes are converted into the raw electrical signals. These signals are then sent to the signal processing circuitry within the encoder. The circuit amplifies the signals and converts them into digital pulses or encoded outputs that correspond to shaft movement.
Finally, the processed signals are sent to the controllers, such as micro-controllers or PID. The controller interprets the encoder feedback to determine the exact position, speed or direction of rotation to enable precise control in automation or motor control systems.
Signal Output of a Rotary Encoder
Rotary encoders generate output signals that represent the movement and position of the shaft. There are two primary types of signal output:
- Incremental Output
It delivers pulses as the shaft rotates. Each pulse corresponds to a specific angular displacement. Incremental encoders have two output channels - A&B for direction detection, and a third channel Z for a reference and zero point. These are often in a square wave format.
- Absolute Output
In this type, each shaft position corresponds to a unique digital code. The encoder provides a binary or grey code output indicating the absolute position of the shaft.
Resolution of a Rotary Encoder
The resolution of the encoder is defined as the number of distinct positions it can detect per revolution. (PPR for incremental or bits for absolute encoders).
- Incremental Resolution (Pulses Per Revolution – PPR)
Higher PPR means finer detection of motion. For example, an encoder with 1000 PPR can detect 0.36° per pulse.
- Absolute Resolution
Defined by the number of bits. A 10-bit encoder provides 210 = 1024 unique positions per revolution. More bits mean higher positional accuracy. Higher resolution enables more precise speed and position control, which is crucial in automation, robotics, and CNC systems.
Applications of Rotary Encoders
Rotary encoders are widely used in industries and systems where precise motion control and position feedback are essential. Some of the applications are:
Rotary encoders are crucial in CNC machines, conveyor systems and automated assembly lines. They help monitor and control motor speed, shaft position, and direction for accurate and efficient operation.
- Robotics
Rotary encoders provide joint and wheel position feedback in robotics arms and mobile robots. This ensures precise movement, path tracking, and coordinated multi-axis control.
- Medical Equipment
High-resolution encoders are used in diagnostic machines, imaging systems, and surgical robots where exact positioning is critical.
- Aerospace and Defence
Used in radar systems, satellite positioning, and navigation equipment for monitoring precise angular motion.
Conclusion
Rotary encoders are indispensable for motion control and automation. By converting mechanical movement into readable signals, they bridge the physical and digital worlds. Understanding how they work — from sensing methods to signal generation and output formats is crucial for engineers, designers, and technicians working in industries where precision and control matter most.
Whether you need basic speed monitoring or advanced multi-axis positioning, there's a rotary encoder tailored for the task.