Working Principle of Stepper Motor
Stepper motors work on the principle of electromagnetism, which helps this motor to achieve precise control over its position. When an electrical current flows through the stator winding, it creates a magnetic field. The direction and magnitude of this magnetic field depend on the current’s direction.
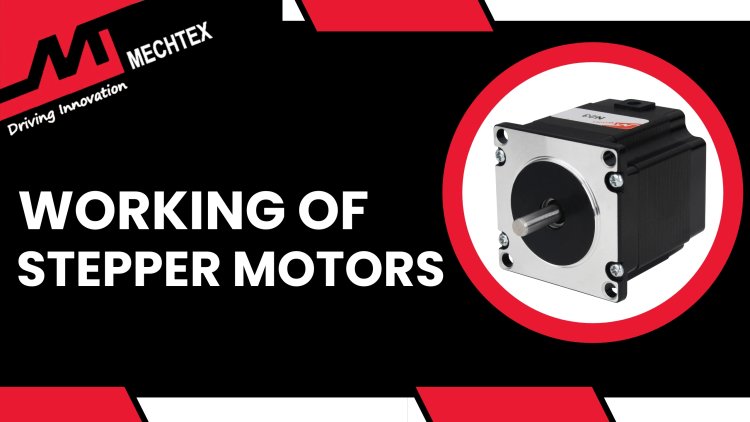
Stepper motors are essential components in modern applications where precise motion is crucial. Unlike conventional motors, which rotate continuously, stepper motor move in fixed or incremental steps allowing for accurate control of position and speed. The working principle of stepper motor is the heart of countless steps with precision and accuracy demanded by various applications. Whether it's a 3D printer, robotic arm, or CNC machine, stepper motors are the preferred choice where movements must be accurate, repeatable, and reliable.
In this blog, we will explore the working principle of stepper motor, how it converts electrical pulses into mechanical rotation that helps an individual to make an informed decision when selecting stepper motors for their application.
What is a Stepper Motor?
A stepper motor is an electric motor that moves in discrete steps and allows for precise control over its speed, position and torque. Unlike other motors that rotate continuously, stepper motors move in small steps with each input pulse, resulting in accurate and repeatable movements. This characteristic makes stepper motors ideal for applications that require precise positioning and accuracy in operation such as 3D printers, CNC machines, and robotics.
A stepper motor consists of two main components: Rotor and Stator. A rotor consists of a permanent magnet and a stator consists of multiple windings. The stator windings are energised in a specific sequence with the help of external circuits. It creates a magnetic field that interacts with the rotor and causes the stepper motor to move in discrete steps. The number of steps per revolution depends upon the motor’s design. The common step angles of the stepper motor range from 0.9° to 1.8° i.e. 200 to 400 steps per revolution.
There are three main types of stepper motor: Permanent Magnet (PM) Stepper Motor, Variable Reluctance (VR) Stepper Motor and Hybrid Stepper Motor.
PM stepper motor consists of a permanent magnet in the rotor and is known for its simple design and low cost. VR stepper motors have non-magnetised tooth rotors that rely on the magnetic reluctance between the stator and rotor. This stepper motor provides high speed with low torque. Hybrid stepper motors are a combination of PM Stepper Motors and VR Stepper Motors. Hybrid stepper motors provide high torque with excellent precision and accuracy, which makes them ideal for applications that require precision in operation.
Also Read
Stepper motors provide high precision and repeat movements, which are advantageous for applications such as 3D printers, and robotics arms where precise positioning is critical. They also have simple control, which makes them easy to integrate into automated systems and reduces the design costs of the system. Additionally, stepper motors have high torque at low speeds, which is beneficial for medical devices which need steady and controlled movements.
Despite various advantages, stepper motors have disadvantages which limit their use in some applications. Stepper motors have low torque at high speed, which is a limitation in applications such as conveyor belts, where quick movements are required. Stepper motors also require external circuits or drivers for operation, which makes their design complex and increases the overall cost of the motor.
Working Principle of Stepper Motor
Stepper motors work on the principle of electromagnetism, where they sequentially energise the windings and generate a rotating magnetic which helps this motor to rotate in precise control. They convert electrical pulses into mechanical shaft movement with precision and accuracy.
A construction stepper motor consists of a rotor and a stator. A rotor is a permanent magnet toothed with an iron core and a stator consists of multiple windings arranged in a circular pattern.
When an electrical current flows through the stator winding, it creates a magnetic field. The direction and magnitude of this magnetic field depend upon the current’s direction. By sequentially energising the stator winding in a controlled manner, the magnetic field rotates around the stator and causes the rotor to rotate in discrete steps.
The sequence of energising the stator winding is controlled by an external driver and controller. The energising sequence determines the rotor’s movement. There are several methods to energise the windings. There are several methods to energise the windings of stepping motors. Some methods are:
Full Step Mode: It energises the two phases of windings of the stepper motor simultaneously, causing the rotor to rotate at a full step (1.8° step) and providing high torque.
Half Step mode: It alternately energises the phases of windings of the stepper motor and causes the rotor to rotate at half step (0.9° step) and offers a good combination of speed and torque.
Micro-stepping mode: It partially energises the multiple phases of windings of the stepper motor simultaneously, which provides smooth movement with high speed and low torque.
Also Read
Explore the different stepping modes of a stepper motor
How Controllers Drive the Stepper Motor
The movement and speed of the stepper motor are controlled with the help of external drivers or controllers. The driver receives the signal from microcontrollers or computers. These signals dictate the timing and sequence of energising the windings, which determines the motor's speed and direction of rotation.
The rotor aligns itself with the first activated magnetic field. With each subsequent electrical pulse, the controller sends a signal to energise the next coil in the sequence, which causes the rotor to align itself with a new magnetic field and rotate in discrete steps.
This process continues with the rotor moving in discrete steps in response to the pulse of the controller. This process provides precise control over the position, speed and torque of the motor.
Conclusion
In summary, the stepper motor operates by converting electrical pulses into mechanical movements through sequential energisation of stator windings. This stepping action ensures controlled, accurate, and repeatable motion. Their ability to offer precise positioning makes stepper motors indispensable in modern applications requiring high accuracy and reliability.